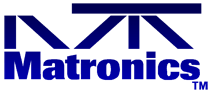 |
Matronics Email Lists Web Forum Interface to the Matronics Email Lists
|
View previous topic :: View next topic |
Author |
Message |
Lynn Matteson
Joined: 10 Jan 2006 Posts: 2778 Location: Grass Lake, Michigan
|
Posted: Sun Jan 23, 2011 10:25 am Post subject: Composites and mold work |
|
|
I made a slight mistake in buying a DVD of a fiberglass project that
some students were doing. One of the best points that I took away
from viewing this DVD was that the *most* important element of
building a mold, or making a product, was the design of the product/
mold. You cannot have negative draft and expect to get the part out
of a one-piece mold. These guys were trying to get a spherical-shaped
part out of a mold, and later realized that the mold must be split at
the widest part of the part, thus eliminating any negative draft in
either of the two parts of the mold. Maybe the male/female corners
could be done this way, eh?
I was taught in Fiberglass 101 (actually an EAA weekend course) to
make up a slurry of resin and filler (filler type depending on the
application) to use in sharp corners....sometimes after the part was
laid up and cured.
Lynn Matteson
Kitfox IV Speedster, taildragger
Jabiru 2200, #2062
Sensenich 62"x 55.5 Wood (winter) until the Prince prop arrives
Electroair direct-fire ignition system
Rotec TBI-40 injection
Status: flying...1078+ hrs (since 3-27-2006)
On Jan 23, 2011, at 11:21 AM, Guy Buchanan wrote:
Quote: |
On 1/23/2011 2:51 AM, great bear wrote:
> I definitely agree that
> vacuum bagging parts is a waste of material and time for the
> projects we are
> doing...if you were building one of rutans space planes or 50 foot
> windmill
> props I could see a reason....but fuel tanks and speedcuffs,
> cowling..little
> fairings....not worth the time and extra material..
Hi. Would you please put your full name, location and aircraft
type / status in your signature line? We, the moderators, find it
makes for a much more congenial atmosphere. Thanks.
Regarding vacuum bagging. It is far more expensive but I
recommended it based on a suggestion of sharp corners in the part.
There's no way to get female corners sharp in a contact laminate,
and male corners are deucedly hard. (Though it can be done with
some crude tooling.) Glasairs and Lancairs and most other composite
kit aircraft were designed very carefully to avoid vacuum bagging,
with all the sharp corners in the provided kit parts.
Guy Buchanan - List moderator
Ramona, CA
Kitfox IV-1200 / 592-C / Warp 3cs / 500 hrs. and grounded
|
| - The Matronics Kitfox-List Email Forum - | | Use the List Feature Navigator to browse the many List utilities available such as the Email Subscriptions page, Archive Search & Download, 7-Day Browse, Chat, FAQ, Photoshare, and much more:
http://www.matronics.com/Navigator?Kitfox-List |
|
_________________ Lynn
Kitfox IV-Jabiru 2200
N369LM |
|
Back to top |
|
 |
Float Flyr
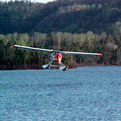
Joined: 19 Jul 2006 Posts: 2704 Location: Campbellton, Newfoundland
|
Posted: Sun Jan 23, 2011 3:35 pm Post subject: Composites and mold work |
|
|
You're right Lynn. However not all resins will cure at room temperature.
The same resins in Pre-preg are available for wet layup. They will require
heat even if applied locally to cure properly. When filling cloth with
resin for the greatest strength and least weight there is a ratio of cloth
to resin by weight which should not be exceeded. Because the stiffness is
caused by the resin and the strength is actually in the cloth too much resin
or too little resin makes for a weaker part.
The process I use is to fill my cloth with resin. I generally weigh the
cloth and the mixed resins. Then I sandwich the cloth in clear plastic and
squeegee out any excess resin. (usually not very much) Then I can put the
cloth "sandwich" rolled up in a refrigerator while making more "sandwiches".
When I have all the cloth I think I'll need in the sandwich from (plastic on
both sides) I then start my lay up... rolling each layer of cloth into the
previous layer. Doing it that way more or less insures me of two things...
an efficient amount of resin in the final product and I can easily see voids
as I do the layup and roll them out.
When we trained in composites we generally used uni-directional cloth but we
also followed a bagging schedule which laid out the direction the warp of
each layer ran. Some bagging schedules had many layers of cloth. Following
the schedule religiously ensured good strength in all directions. You would
be amazed at the strength of a piece of composite glass or graphite two
inches long and 1/8 in thick(in both directions)
There is a problem with vacuum bagged composites which comes up from time to
time. That is it is porous. A small insignificant nick in the finish of say
a 777 cowl can be very dangerous as rain water can seep into the material
through a scratch. At altitude the water freezes and the cowl can be
internally forced apart by the expansion of the freezing water. A slight
rub by a forklift brushing an aluminium cowl may not be of any concern. The
same damage to a composite will ground the aircraft until the cowl is
replaced.... bring MONEY!
The crown who were specializing in composite repair (not me) used to make
forms to mould on. Those Forms (plugs) were made of straw wet with some
kind of plaster for the rough shape then finished with plaster of paris
which can be sanded to final shape and then waxed.
Noel
--
| - The Matronics Kitfox-List Email Forum - | | Use the List Feature Navigator to browse the many List utilities available such as the Email Subscriptions page, Archive Search & Download, 7-Day Browse, Chat, FAQ, Photoshare, and much more:
http://www.matronics.com/Navigator?Kitfox-List |
|
_________________ Noel Loveys
Kitfox III-A
Aerocet 1100 Floats |
|
Back to top |
|
 |
Float Flyr
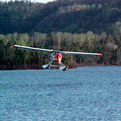
Joined: 19 Jul 2006 Posts: 2704 Location: Campbellton, Newfoundland
|
Posted: Sun Jan 23, 2011 4:13 pm Post subject: Composites and mold work |
|
|
I gotta love that idea!
Noel
--
| - The Matronics Kitfox-List Email Forum - | | Use the List Feature Navigator to browse the many List utilities available such as the Email Subscriptions page, Archive Search & Download, 7-Day Browse, Chat, FAQ, Photoshare, and much more:
http://www.matronics.com/Navigator?Kitfox-List |
|
_________________ Noel Loveys
Kitfox III-A
Aerocet 1100 Floats |
|
Back to top |
|
 |
Lynn Matteson
Joined: 10 Jan 2006 Posts: 2778 Location: Grass Lake, Michigan
|
Posted: Sun Jan 23, 2011 6:48 pm Post subject: Composites and mold work |
|
|
I bought the publication "Moldless Composite Sandwich Aircraft
Construction" by the Rutan Aircraft Factory, and in it there is an
exercise where you make three different pads of fiberglass, each one
to measure 8" x 8". You make one too wet, one too dry and one "just
right", by squeegeeing with many light strokes. After curing, each is
cut to a size of 7" x 7", then weighed and compared. They say the
correct weight should be 2.25 ounces. If the heavy one weighs 2.55
ounces, it will add 35 pounds to the finished VariEze, if this heavy
construction is used throughout the building of the plane. I'm sure
we can guess what happens if the light method is followed.
When I recently made spats for my skis, I did the 8" x 8" pads, but I
was more interested in how thick and how strong 2 plies, versus 3
plies, versus 4 plies would be. I settled on the 2 plies for my
project....the 4 plies (of E-glass) would have been almost strong
enough to make the ski bottoms from....it was stiff!
I've never given any thought to the pre-pregs...how do you "kick off"
the curing activity? There must be something added to the pre-pregged
cloths, isn't there? That technology just seems a bit out of my
league. : )
I used bi-directional E-glass cloth for my spats, because I was
limited by the amount of angle that I could get by using material
that was only 50 inches wide. My method was probably not going to
meet aircraft-building standards, but I feel that it was good enough
for the task of keeping snow off my skis.
Lynn Matteson
Kitfox IV Speedster, taildragger
Jabiru 2200, #2062
Sensenich 62"x 55.5 Wood (winter) until the Prince prop arrives
Electroair direct-fire ignition system
Rotec TBI-40 injection
Status: flying...1080+ hrs (since 3-27-2006)
On Jan 23, 2011, at 6:29 PM, Noel Loveys wrote:
Quote: |
You're right Lynn. However not all resins will cure at room
temperature.
The same resins in Pre-preg are available for wet layup. They will
require
heat even if applied locally to cure properly. When filling cloth
with
resin for the greatest strength and least weight there is a ratio
of cloth
to resin by weight which should not be exceeded. Because the
stiffness is
caused by the resin and the strength is actually in the cloth too
much resin
or too little resin makes for a weaker part.
The process I use is to fill my cloth with resin. I generally weigh
the
cloth and the mixed resins. Then I sandwich the cloth in clear
plastic and
squeegee out any excess resin. (usually not very much) Then I can
put the
cloth "sandwich" rolled up in a refrigerator while making more
"sandwiches".
When I have all the cloth I think I'll need in the sandwich from
(plastic on
both sides) I then start my lay up... rolling each layer of cloth
into the
previous layer. Doing it that way more or less insures me of two
things...
an efficient amount of resin in the final product and I can easily
see voids
as I do the layup and roll them out.
When we trained in composites we generally used uni-directional
cloth but we
also followed a bagging schedule which laid out the direction the
warp of
each layer ran. Some bagging schedules had many layers of cloth.
Following
the schedule religiously ensured good strength in all directions.
You would
be amazed at the strength of a piece of composite glass or graphite
two
inches long and 1/8 in thick(in both directions)
There is a problem with vacuum bagged composites which comes up
from time to
time. That is it is porous. A small insignificant nick in the
finish of say
a 777 cowl can be very dangerous as rain water can seep into the
material
through a scratch. At altitude the water freezes and the cowl can be
internally forced apart by the expansion of the freezing water. A
slight
rub by a forklift brushing an aluminium cowl may not be of any
concern. The
same damage to a composite will ground the aircraft until the cowl is
replaced.... bring MONEY!
The crown who were specializing in composite repair (not me) used
to make
forms to mould on. Those Forms (plugs) were made of straw wet with
some
kind of plaster for the rough shape then finished with plaster of
paris
which can be sanded to final shape and then waxed.
Noel
|
| - The Matronics Kitfox-List Email Forum - | | Use the List Feature Navigator to browse the many List utilities available such as the Email Subscriptions page, Archive Search & Download, 7-Day Browse, Chat, FAQ, Photoshare, and much more:
http://www.matronics.com/Navigator?Kitfox-List |
|
_________________ Lynn
Kitfox IV-Jabiru 2200
N369LM |
|
Back to top |
|
 |
Float Flyr
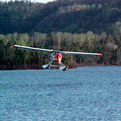
Joined: 19 Jul 2006 Posts: 2704 Location: Campbellton, Newfoundland
|
Posted: Mon Jan 24, 2011 7:58 am Post subject: Composites and mold work |
|
|
Snip:
I've never given any thought to the pre-pregs...how do you "kick off"
the curing activity? There must be something added to the pre-pregged
cloths, isn't there? That technology just seems a bit out of my
league. : )
Pre-Preg is stored in a freezer. It must be thawed to room temperature
several hours before layup. While thawing is should be kept sealed in tis
envelope to protect it from condensation.
Then it is heat which accelerates the curing to 100%. Because epoxy resins
will allow being added to if done in a specific time it is possible to
return a cured part to layup for additional work if necessary. Generally
though you have enough pot time to allow the lay up in one shot. BTW
composites is not only glass and resin. There is also paper honeycomb,
Aluminium sheeting and honeycomb available for composite work. I'll bet
Burt Rutan's book goes into that too.
With composite layup work cleanliness is, never mind next to godliness, it
is godliness! Dust/dirt is a great enemy. Final trimming and finishing,
especially sanding, should be done in a different location. Commercial
plants have huge clean rooms which actually surpass OR requirements.
If I was going to build a glass plane I think I would contract out the
construction of the flight surfaces. Most of the fuselage I would do
myself. If for no other reason than just to have the parts checked by
ultrasound. Believe me the parts would be lighter and definitely stronger!
I went to the "Cozy girls" site... They are my kind of people... Nuts!
Good nuts though. Their process of lowvac bagging seems to be a good
compromise between true wet layup and vacuum bagging commercially but there
is no way their procedure can expect to be as strong as what is achieved on
a daily basis at a commercial facility. Their two large advantages are they
can make changes to the design on the fly (sorry Pun) and of course the
cost.
Noel
| - The Matronics Kitfox-List Email Forum - | | Use the List Feature Navigator to browse the many List utilities available such as the Email Subscriptions page, Archive Search & Download, 7-Day Browse, Chat, FAQ, Photoshare, and much more:
http://www.matronics.com/Navigator?Kitfox-List |
|
_________________ Noel Loveys
Kitfox III-A
Aerocet 1100 Floats |
|
Back to top |
|
 |
Lynn Matteson
Joined: 10 Jan 2006 Posts: 2778 Location: Grass Lake, Michigan
|
Posted: Mon Jan 24, 2011 10:55 am Post subject: Composites and mold work |
|
|
You mean if I ordered pre-pregs, they would be shipped frozen? Not
bloody likely, mate! Oops, never mind that remark...I just read
where " the material can be shipped...etc, at room temperature, blah,
blah, blah, and cured at up to 310 degrees..." That is a bit too
convoluted for my brain to wrap itself around, so I'll just stick to
plain ol' fiberglass, E-glass, and the more common forms of
'glassing for my simple projects.
By the way, a friend of mine showed me a roll...100 yards...of carbon
fiber, 12k, I think it was.....something in the neighborhood of
$5,000 with shipping?
Lynn Matteson
Kitfox IV Speedster, taildragger
Jabiru 2200, #2062
Sensenich 62"x 55.5 Wood (winter) until the Prince prop arrives
Electroair direct-fire ignition system
Rotec TBI-40 injection
Status: flying...1080+ hrs (since 3-27-2006)
do not archive
On Jan 24, 2011, at 10:55 AM, Noel Loveys wrote:
Quote: |
Snip:
I've never given any thought to the pre-pregs...how do you "kick off"
the curing activity? There must be something added to the pre-pregged
cloths, isn't there? That technology just seems a bit out of my
league. : )
Pre-Preg is stored in a freezer. It must be thawed to room
temperature
several hours before layup. While thawing is should be kept sealed
in tis
envelope to protect it from condensation.
Then it is heat which accelerates the curing to 100%. Because
epoxy resins
will allow being added to if done in a specific time it is possible to
return a cured part to layup for additional work if necessary.
Generally
though you have enough pot time to allow the lay up in one shot. BTW
composites is not only glass and resin. There is also paper
honeycomb,
Aluminium sheeting and honeycomb available for composite work.
I'll bet
Burt Rutan's book goes into that too.
With composite layup work cleanliness is, never mind next to
godliness, it
is godliness! Dust/dirt is a great enemy. Final trimming and
finishing,
especially sanding, should be done in a different location.
Commercial
plants have huge clean rooms which actually surpass OR requirements.
If I was going to build a glass plane I think I would contract out the
construction of the flight surfaces. Most of the fuselage I would do
myself. If for no other reason than just to have the parts checked by
ultrasound. Believe me the parts would be lighter and definitely
stronger!
I went to the "Cozy girls" site... They are my kind of people...
Nuts!
Good nuts though. Their process of lowvac bagging seems to be a good
compromise between true wet layup and vacuum bagging commercially
but there
is no way their procedure can expect to be as strong as what is
achieved on
a daily basis at a commercial facility. Their two large advantages
are they
can make changes to the design on the fly (sorry Pun) and of course
the
cost.
Noel
|
| - The Matronics Kitfox-List Email Forum - | | Use the List Feature Navigator to browse the many List utilities available such as the Email Subscriptions page, Archive Search & Download, 7-Day Browse, Chat, FAQ, Photoshare, and much more:
http://www.matronics.com/Navigator?Kitfox-List |
|
_________________ Lynn
Kitfox IV-Jabiru 2200
N369LM |
|
Back to top |
|
 |
|
|
You cannot post new topics in this forum You cannot reply to topics in this forum You cannot edit your posts in this forum You cannot delete your posts in this forum You cannot vote in polls in this forum You cannot attach files in this forum You can download files in this forum
|
Powered by phpBB © 2001, 2005 phpBB Group
|