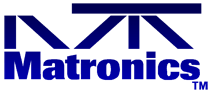 |
Matronics Email Lists Web Forum Interface to the Matronics Email Lists
|
View previous topic :: View next topic |
Author |
Message |
trigo(at)mail.telepac.pt Guest
|
Posted: Thu Feb 06, 2014 7:41 am Post subject: engine pressure senders installation |
|
|
Tim
So, what is the way to mount engine pressure senders not cantilevered?
Carlos
At 03:04 PM 2/5/2014, you wrote:
Quote: | AeroElectric-List message posted by: Tim Andres
<tim2542(at)sbcglobal.net>
|
Most of us probably know this, but cantilever mounted engine pressure
senders is bad practice, steel or brass. I have personally seen steel
ones break.
Tim
| - The Matronics AeroElectric-List Email Forum - | | Use the List Feature Navigator to browse the many List utilities available such as the Email Subscriptions page, Archive Search & Download, 7-Day Browse, Chat, FAQ, Photoshare, and much more:
http://www.matronics.com/Navigator?AeroElectric-List |
|
|
|
Back to top |
|
 |
glastar(at)gmx.net Guest
|
Posted: Thu Feb 06, 2014 8:01 am Post subject: engine pressure senders installation |
|
|
via a flexible hose and the pressure sensors on he FW ( I use the T bar
from Van's to mount them, advantage is I can have a pressure sensor plus
a switch on the same hose for oil pressure. SHould have somewhere some
pictures from my Glastar
On 06.02.2014 16:45, Carlos Trigo wrote:
Quote: |
Tim
So, what is the way to mount engine pressure senders not cantilevered?
|
| - The Matronics AeroElectric-List Email Forum - | | Use the List Feature Navigator to browse the many List utilities available such as the Email Subscriptions page, Archive Search & Download, 7-Day Browse, Chat, FAQ, Photoshare, and much more:
http://www.matronics.com/Navigator?AeroElectric-List |
|
|
|
Back to top |
|
 |
trigo(at)mail.telepac.pt Guest
|
Posted: Thu Feb 06, 2014 8:18 am Post subject: engine pressure senders installation |
|
|
Hi Werner
Well, that one I know, I've used it in the RV-9A and also the -10, but the
senders are also cantilever mounted in the T bar ... I know that the T bar
will not shake as the engine itself, but there are also cantilevered, and
can break as well
Carlos
-----Mensagem original-----
De: owner-aeroelectric-list-server(at)matronics.com
[mailto:owner-aeroelectric-list-server(at)matronics.com] Em nome de Werner
Schneider
Enviada: 6 de fevereiro de 2014 16:00
Para: aeroelectric-list(at)matronics.com
Assunto: Re: engine pressure senders installation
--> <glastar(at)gmx.net>
via a flexible hose and the pressure sensors on he FW ( I use the T bar from
Van's to mount them, advantage is I can have a pressure sensor plus a switch
on the same hose for oil pressure. SHould have somewhere some pictures from
my Glastar
On 06.02.2014 16:45, Carlos Trigo wrote:
Quote: |
--> <trigo(at)mail.telepac.pt>
Tim
So, what is the way to mount engine pressure senders not cantilevered?
|
| - The Matronics AeroElectric-List Email Forum - | | Use the List Feature Navigator to browse the many List utilities available such as the Email Subscriptions page, Archive Search & Download, 7-Day Browse, Chat, FAQ, Photoshare, and much more:
http://www.matronics.com/Navigator?AeroElectric-List |
|
|
|
Back to top |
|
 |
tim2542(at)sbcglobal.net Guest
|
Posted: Thu Feb 06, 2014 8:34 am Post subject: engine pressure senders installation |
|
|
Hi Carlos
Obviously they have to be installed cantilevered, just don't mount them to the vibrating engine.
Remote mount them with a block like this Aircraft spruce part, [url=tel:04-00318]04-00318[/url], mounted on the firewall, run -3 hose to it with a restrictor fitting at the engine to restrict flow if there is a hose failure or fire. This for oil and fuel pressure.
Tim
On Feb 6, 2014, at 7:45 AM, "Carlos Trigo" <trigo(at)mail.telepac.pt (trigo(at)mail.telepac.pt)> wrote:
[quote]--> AeroElectric-List message posted by: "Carlos Trigo" <trigo(at)mail.telepac.pt (trigo(at)mail.telepac.pt)>
Tim
So, what is the way to mount engine pressure senders not cantilevered?
Carlos
At 03:04 PM 2/5/2014, you wrote:
Quote: | AeroElectric-List message posted by: Tim Andres
| <tim2542(at)sbcglobal.net (tim2542(at)sbcglobal.net)>
Most of us probably know this, but cantilever mounted engine pressure
senders is bad practice, steel or brass. I have personally seen steel
ones break.
Tim
http://forums.matr====================================================sp;   href="http://www.matronics.com/contribution">http://www.matronics.com/con=============================================
[b]
| - The Matronics AeroElectric-List Email Forum - | | Use the List Feature Navigator to browse the many List utilities available such as the Email Subscriptions page, Archive Search & Download, 7-Day Browse, Chat, FAQ, Photoshare, and much more:
http://www.matronics.com/Navigator?AeroElectric-List |
|
|
|
Back to top |
|
 |
glastar(at)gmx.net Guest
|
Posted: Thu Feb 06, 2014 10:09 am Post subject: engine pressure senders installation |
|
|
Carlos, mine are vertical so much different scenario, and the vibration
level is magnitudes less then directly on the engine housing. You could
mount it on the hose only and then fix the sensor by a clamp around the
sensor housing that is the least stress on them.
Cheers Werner
On 06.02.2014 17:23, Carlos Trigo wrote:
Quote: |
Hi Werner
Well, that one I know, I've used it in the RV-9A and also the -10, but the
senders are also cantilever mounted
|
| - The Matronics AeroElectric-List Email Forum - | | Use the List Feature Navigator to browse the many List utilities available such as the Email Subscriptions page, Archive Search & Download, 7-Day Browse, Chat, FAQ, Photoshare, and much more:
http://www.matronics.com/Navigator?AeroElectric-List |
|
|
|
Back to top |
|
 |
email(at)jaredyates.com Guest
|
Posted: Thu Feb 06, 2014 10:34 am Post subject: engine pressure senders installation |
|
|
I put a large adel clamp around my oil pressure sender, actually two of them. Then those adel clamps are bolted to smaller clamps that go around two nearby engine mount tubes. As I understand the term cantilevered, I would say that mine is not.
On Thu, Feb 6, 2014 at 1:08 PM, Werner Schneider <glastar(at)gmx.net (glastar(at)gmx.net)> wrote:
[quote] --> AeroElectric-List message posted by: Werner Schneider <glastar(at)gmx.net (glastar(at)gmx.net)>
Carlos, mine are vertical so much different scenario, and the vibration level is magnitudes less then directly on the engine housing. You could mount it on the hose only and then fix the sensor by a clamp around the sensor housing that is the least stress on them.
Cheers Werner
On 06.02.2014 17:23, Carlos Trigo wrote:
Quote: | --> AeroElectric-List message posted by: "Carlos Trigo" <trigo(at)mail.telepac.pt (trigo(at)mail.telepac.pt)>
Hi Werner
Well, that one I know, I've used it in the RV-9A and also the -10, but the
senders are also cantilever mounted
|
====================================
-List" target="_blank">http://www.matronics.com/Navigator?AeroElectric-List
====================================
http://forums.matronics.com
====================================
le, List Admin.
="_blank">http://www.matronics.com/contribution
====================================
[b]
| - The Matronics AeroElectric-List Email Forum - | | Use the List Feature Navigator to browse the many List utilities available such as the Email Subscriptions page, Archive Search & Download, 7-Day Browse, Chat, FAQ, Photoshare, and much more:
http://www.matronics.com/Navigator?AeroElectric-List |
|
|
|
Back to top |
|
 |
rlborger(at)mac.com Guest
|
Posted: Thu Feb 06, 2014 10:46 am Post subject: engine pressure senders installation |
|
|
Carlos,
You can see how I did it at: http://www.europaowners.org/main.php?g2_itemId=67636
The first 11 pictures show how I did a remote mount of the oil pressure sender.
Blue skies & tailwinds,
Bob Borger
Europa XS Tri, Rotax 914, Airmaster C/S Prop (50 hrs).
Little Toot Sport Biplane, Lycoming Thunderbolt AEIO-320 EXP
3705 Lynchburg Dr.
Corinth, TX 76208-5331
Cel: 817-992-1117
rlborger(at)mac.com
On Feb 6, 2014, at 9:45 AM, Carlos Trigo <trigo(at)mail.telepac.pt> wrote:
Tim
So, what is the way to mount engine pressure senders not cantilevered?
Carlos
| - The Matronics AeroElectric-List Email Forum - | | Use the List Feature Navigator to browse the many List utilities available such as the Email Subscriptions page, Archive Search & Download, 7-Day Browse, Chat, FAQ, Photoshare, and much more:
http://www.matronics.com/Navigator?AeroElectric-List |
|
|
|
Back to top |
|
 |
tim2542(at)sbcglobal.net Guest
|
Posted: Thu Feb 06, 2014 2:08 pm Post subject: engine pressure senders installation |
|
|
Hi Werner, with respect, it is NOT a much different scenario. Its orientation makes no difference, it's a cantilevered mounted sensor no matter where or how you mount it. It's the mass vibrating on the end of the threaded fitting that may cause the failure.
If you support it like suggested with an Adel clamp that may work, but the correct fix (and good practice) is to remote mount it somewhere other than on the engine.
Tim
[quote] Werner Schneider> Quote: |
Carlos, mine are vertical so much different scenario, and the vibration level is magnitudes less then directly on the engine housing. You could mount it on the hose only and then fix the sensor by a clamp around the sensor housing that is the least stress on them.
Cheers Werner
|
[b]
| - The Matronics AeroElectric-List Email Forum - | | Use the List Feature Navigator to browse the many List utilities available such as the Email Subscriptions page, Archive Search & Download, 7-Day Browse, Chat, FAQ, Photoshare, and much more:
http://www.matronics.com/Navigator?AeroElectric-List |
|
|
|
Back to top |
|
 |
glastar(at)gmx.net Guest
|
Posted: Thu Feb 06, 2014 10:12 pm Post subject: engine pressure senders installation |
|
|
Tim,
mine are mounted remote on the Firewall (which indirectly is written in
my posting (vibration level.....)), directly on the engine IS a bad idea.
Werner
On 06.02.2014 23:06, Tim Andres wrote:
Quote: | Hi Werner, with respect, it is NOT a much different scenario. Its
orientation makes no difference, it's a cantilevered mounted sensor no
matter where or how you mount it. It's the mass vibrating on the end of
the threaded fitting that may cause the failure.
If you support it like suggested with an Adel clamp that may work, but
the correct fix (and good practice) is to remote mount it somewhere
other than on the engine.
Tim
> Werner Schneider>
> Carlos, mine are vertical so much different scenario, and the
> vibration level is magnitudes less then directly on the engine
> housing. You could mount it on the hose only and then fix the
> sensor by a clamp around the sensor housing that is the least
> stress on them.
>
> Cheers Werner
> *
> *
*
*
|
| - The Matronics AeroElectric-List Email Forum - | | Use the List Feature Navigator to browse the many List utilities available such as the Email Subscriptions page, Archive Search & Download, 7-Day Browse, Chat, FAQ, Photoshare, and much more:
http://www.matronics.com/Navigator?AeroElectric-List |
|
|
|
Back to top |
|
 |
mapratherid(at)gmail.com Guest
|
Posted: Wed Feb 12, 2014 10:03 pm Post subject: engine pressure senders installation |
|
|
Nice set of photos Bob.. I wonder if you also went back and provided strain relief for the hose. I believe strain relief for the hose might be more important than remote mounting the sender.
Regards,
Matt-
Quote: | On Feb 6, 2014, at 11:45 AM, Robert Borger <rlborger(at)mac.com> wrote:
Carlos,
You can see how I did it at: http://www.europaowners.org/main.php?g2_itemId=67636
The first 11 pictures show how I did a remote mount of the oil pressure sender.
Blue skies & tailwinds,
Bob Borger
Europa XS Tri, Rotax 914, Airmaster C/S Prop (50 hrs).
Little Toot Sport Biplane, Lycoming Thunderbolt AEIO-320 EXP
3705 Lynchburg Dr.
Corinth, TX 76208-5331
Cel: 817-992-1117
rlborger(at)mac.com
On Feb 6, 2014, at 9:45 AM, Carlos Trigo <trigo(at)mail.telepac.pt> wrote:
Tim
So, what is the way to mount engine pressure senders not cantilevered?
Carlos
|
| - The Matronics AeroElectric-List Email Forum - | | Use the List Feature Navigator to browse the many List utilities available such as the Email Subscriptions page, Archive Search & Download, 7-Day Browse, Chat, FAQ, Photoshare, and much more:
http://www.matronics.com/Navigator?AeroElectric-List |
|
|
|
Back to top |
|
 |
ceengland7(at)gmail.com Guest
|
Posted: Thu Feb 13, 2014 7:15 am Post subject: engine pressure senders installation |
|
|
I'm curious. How many pressure senders have broken *when directly
mounted to the engine*? I see a lot of reports of failures when there's
an extension, adapter, T fitting, etc, but there are thousands (hundreds
of thousands? millions?) of those sensors that live while directly
mounted on all types of automotive, industrial and a/c engines.
I might be wrong, but these are the questions I'd ask: How stiff is a
braided oil line when it's fully pressurized while the engine is
running? What does it weigh? How much vibration gets transmitted up the
fairly stiff pressurized line? How does that weight & vibration affect
the cantilevered *aluminum* adapters connecting it to the pressure
sensor? I suspect that the cantilevered weight of the hose is more than
the weight of the sensor, on its steel mounting threads, and there will
still be a lot of vibration transmitted to the fittings.
Am I mistaken?
Charlie
On 2/12/2014 11:58 PM, Matthew Prather wrote:
Quote: |
Nice set of photos Bob.. I wonder if you also went back and provided strain relief for the hose. I believe strain relief for the hose might be more important than remote mounting the sender.
Regards,
Matt-
> On Feb 6, 2014, at 11:45 AM, Robert Borger <rlborger(at)mac.com> wrote:
>
>
>
> Carlos,
>
> You can see how I did it at: http://www.europaowners.org/main.php?g2_itemId=67636
>
> The first 11 pictures show how I did a remote mount of the oil pressure sender.
>
> Blue skies & tailwinds,
> Bob Borger
> Europa XS Tri, Rotax 914, Airmaster C/S Prop (50 hrs).
> Little Toot Sport Biplane, Lycoming Thunderbolt AEIO-320 EXP
> 3705 Lynchburg Dr.
> Corinth, TX 76208-5331
> Cel: 817-992-1117
> rlborger(at)mac.com
>
> On Feb 6, 2014, at 9:45 AM, Carlos Trigo <trigo(at)mail.telepac.pt> wrote:
>
>
>
> Tim
>
> So, what is the way to mount engine pressure senders not cantilevered?
>
> Carlos
>
|
| - The Matronics AeroElectric-List Email Forum - | | Use the List Feature Navigator to browse the many List utilities available such as the Email Subscriptions page, Archive Search & Download, 7-Day Browse, Chat, FAQ, Photoshare, and much more:
http://www.matronics.com/Navigator?AeroElectric-List |
|
|
|
Back to top |
|
 |
nuckolls.bob(at)aeroelect Guest
|
Posted: Thu Feb 13, 2014 8:17 am Post subject: engine pressure senders installation |
|
|
At 09:12 AM 2/13/2014, you wrote:
Quote: | --> AeroElectric-List message posted by: Charlie England <ceengland7(at)gmail.com>
I'm curious. How many pressure senders have broken *when directly mounted to the engine*? I see a lot of reports of failures when there's an extension, adapter, T fitting, etc, but there are thousands (hundreds of thousands? millions?) of those sensors that live while directly mounted on all types of automotive, industrial and a/c engines. |
We need to sift the simple ideas that drive
levels of concern for this thread. (1) non-ferrous
plumbing/attache hardware that has a finite
service life subjected to the as-installed,
vibration stress levels and (2) lever moments
which are product of mass x arm that produces
the leverage under vibratory acceleration.
There's nothing inherently risky about mounting
a sensor right to the engine. It's done on cars
all the time . . . and probably less vibration
stress. Consider this oil pressure transducer.
[img]cid:.0[/img]
All steel structure, short moment arm, light
mass . . . risk approaching zero.
Consider this one . . .
[img]cid:.1[/img]
Hmmm . . . fatter, longer, but still steel . . .
probably still okay plugged right into the engine.
But consider the installation that demands
multiple 'sensors' . . . say one of these
fat rascals, stuck into a brass tee-fitting opposite
a low oil pressure warning switch. Now put
a not-so-close brass nipple. The high risk
joint is where the brass screws into the
engine with all that stuff hung off the
end.
There's are ancillary concerns for deciding
whether or not to mount a sensor directly
to the engine . . . temperature and vibration
effects on the transducer itself . . .generally
low risk but a question to ask and answer.
Quote: | I might be wrong, but these are the questions I'd ask: How stiff is a braided oil line when it's fully pressurized while the engine is running? What does it weigh? How much vibration gets transmitted up the fairly stiff pressurized line? How does that weight & vibration affect the cantilevered *aluminum* adapters connecting it to the pressure sensor? I suspect that the cantilevered weight of the hose is more than the weight of the sensor, on its steel mounting threads, and there will still be a lot of vibration transmitted to the fittings.
Am I mistaken? |
Stresses that a flexible line would put on
the threads at the engine are minimal . . . if
the threads are steel . . . the risks are zero.
Risks risk sharply with high moment installations
on rigid, brass, pot-metal or aluminum, christmas-trees.
Bob . . .
| - The Matronics AeroElectric-List Email Forum - | | Use the List Feature Navigator to browse the many List utilities available such as the Email Subscriptions page, Archive Search & Download, 7-Day Browse, Chat, FAQ, Photoshare, and much more:
http://www.matronics.com/Navigator?AeroElectric-List |
|
Description: |
|
Filesize: |
23.54 KB |
Viewed: |
5772 Time(s) |
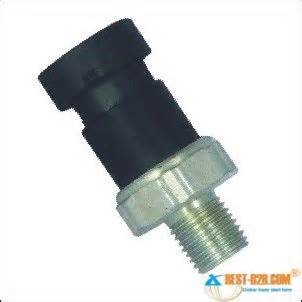
|
Description: |
|
Filesize: |
17.55 KB |
Viewed: |
5772 Time(s) |
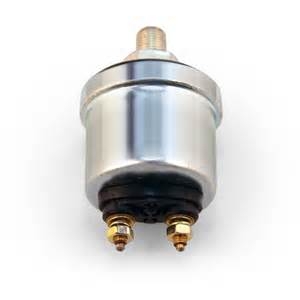
|
|
|
Back to top |
|
 |
ceengland7(at)gmail.com Guest
|
Posted: Thu Feb 13, 2014 8:39 am Post subject: engine pressure senders installation |
|
|
| - The Matronics AeroElectric-List Email Forum - | | Use the List Feature Navigator to browse the many List utilities available such as the Email Subscriptions page, Archive Search & Download, 7-Day Browse, Chat, FAQ, Photoshare, and much more:
http://www.matronics.com/Navigator?AeroElectric-List |
|
|
|
Back to top |
|
 |
rlborger(at)mac.com Guest
|
Posted: Thu Feb 13, 2014 9:00 am Post subject: engine pressure senders installation |
|
|
Hi Charlie,
My original concern for having the oil pressure sender mounted on the engine was a result of a series short time of oil pressure sender failures which were reported on the Rotax and Europa lists a number of years ago. Due to the placement of the sender on the engine it was surmised that these were failures from the sender being repeatedly shaken during engine start and stop. The recommendation was made by someone on the list that the sender be removed from the engine and remote mounted on the firewall to get it out of the vibrational environment of the engine.
In my case I used a length of Aeroquip 666 1/8” hose which is braided stainless steel over teflon with stainless steel fittings. I have never weighed the line but it isn’t very heavy. Just went out to the shop and weighed a similar length of 666 with fittings and it weighs 2 oz. I doubt it is any stiffer pressurized than it is unpressurized. There are no aluminum fittings connecting to the engine. A steel AN fitting was used to connect the hose to the engine. The weight of the hose as supported by the engine fitting is considerably less than the weight of the sender ~16 oz. Considerably less than an ounce on the fitting. I have confirmed that there are no vibrations being transmitted through the hose back to the sender or its fittings. The hose seems to do a good job of absorbing rather than transmitting vibrations.
Hope this helps.
Blue skies & tailwinds,
Bob Borger
Europa XS Tri, Rotax 914, Airmaster C/S Prop (50 hrs).
Little Toot Sport Biplane, Lycoming Thunderbolt AEIO-320 EXP
3705 Lynchburg Dr.
Corinth, TX 76208-5331
Cel: 817-992-1117
rlborger(at)mac.com
On Feb 13, 2014, at 9:12 AM, Charlie England <ceengland7(at)gmail.com> wrote:
I'm curious. How many pressure senders have broken *when directly mounted to the engine*? I see a lot of reports of failures when there's an extension, adapter, T fitting, etc, but there are thousands (hundreds of thousands? millions?) of those sensors that live while directly mounted on all types of automotive, industrial and a/c engines.
I might be wrong, but these are the questions I'd ask: How stiff is a braided oil line when it's fully pressurized while the engine is running? What does it weigh? How much vibration gets transmitted up the fairly stiff pressurized line? How does that weight & vibration affect the cantilevered *aluminum* adapters connecting it to the pressure sensor? I suspect that the cantilevered weight of the hose is more than the weight of the sensor, on its steel mounting threads, and there will still be a lot of vibration transmitted to the fittings.
Am I mistaken?
Charlie
| - The Matronics AeroElectric-List Email Forum - | | Use the List Feature Navigator to browse the many List utilities available such as the Email Subscriptions page, Archive Search & Download, 7-Day Browse, Chat, FAQ, Photoshare, and much more:
http://www.matronics.com/Navigator?AeroElectric-List |
|
|
|
Back to top |
|
 |
ceengland7(at)gmail.com Guest
|
Posted: Thu Feb 13, 2014 10:57 am Post subject: engine pressure senders installation |
|
|
Hi Bob,
I do understand worrying about stress & vibration issues. What caught my
attention was what appeared to be aluminum adapters on the pressure
sensor itself, cantilevering the right angle adapter and hose away from
the sensor's mount. I could imagine the aluminum adapters being at risk
more than the steel threaded sensor.
What was the nature of the failures? I was envisioning the sender
breaking off at the threads. Was it some sort of internal failure,
instead? Most current RV-x builders do remote mount the sensor, but they
seem to survive on a lot of motors when they are direct- mounted. If
there is a high percentage of failures on the Rotax, I wonder if it's
caused by the very different frequency of vibration from the Rotax,
compared to most other engines running at constant-RPM.
Charlie
On 2/13/2014 10:57 AM, Robert Borger wrote:
Quote: |
Hi Charlie,
My original concern for having the oil pressure sender mounted on the engine was a result of a series short time of oil pressure sender failures which were reported on the Rotax and Europa lists a number of years ago. Due to the placement of the sender on the engine it was surmised that these were failures from the sender being repeatedly shaken during engine start and stop. The recommendation was made by someone on the list that the sender be removed from the engine and remote mounted on the firewall to get it out of the vibrational environment of the engine.
In my case I used a length of Aeroquip 666 1/8” hose which is braided stainless steel over teflon with stainless steel fittings. I have never weighed the line but it isn’t very heavy. Just went out to the shop and weighed a similar length of 666 with fittings and it weighs 2 oz. I doubt it is any stiffer pressurized than it is unpressurized. There are no aluminum fittings connecting to the engine. A steel AN fitting was used to connect the hose to the engine. The weight of the hose as supported by the engine fitting is considerably less than the weight of the sender ~16 oz. Considerably less than an ounce on the fitting. I have confirmed that there are no vibrations being transmitted through the hose back to the sender or its fittings. The hose seems to do a good job of absorbing rather than transmitting vibrations.
Hope this helps.
Blue skies & tailwinds,
Bob Borger
Europa XS Tri, Rotax 914, Airmaster C/S Prop (50 hrs).
Little Toot Sport Biplane, Lycoming Thunderbolt AEIO-320 EXP
3705 Lynchburg Dr.
Corinth, TX 76208-5331
Cel: 817-992-1117
rlborger(at)mac.com
On Feb 13, 2014, at 9:12 AM, Charlie England <ceengland7(at)gmail.com> wrote:
I'm curious. How many pressure senders have broken *when directly mounted to the engine*? I see a lot of reports of failures when there's an extension, adapter, T fitting, etc, but there are thousands (hundreds of thousands? millions?) of those sensors that live while directly mounted on all types of automotive, industrial and a/c engines.
I might be wrong, but these are the questions I'd ask: How stiff is a braided oil line when it's fully pressurized while the engine is running? What does it weigh? How much vibration gets transmitted up the fairly stiff pressurized line? How does that weight & vibration affect the cantilevered *aluminum* adapters connecting it to the pressure sensor? I suspect that the cantilevered weight of the hose is more than the weight of the sensor, on its steel mounting threads, and there will still be a lot of vibration transmitted to the fittings.
Am I mistaken?
Charlie
|
| - The Matronics AeroElectric-List Email Forum - | | Use the List Feature Navigator to browse the many List utilities available such as the Email Subscriptions page, Archive Search & Download, 7-Day Browse, Chat, FAQ, Photoshare, and much more:
http://www.matronics.com/Navigator?AeroElectric-List |
|
|
|
Back to top |
|
 |
kleh(at)dialupatcost.ca Guest
|
Posted: Thu Feb 13, 2014 12:54 pm Post subject: engine pressure senders installation |
|
|
Years ago while touring a rotax overhaul facility I noticed the vdo
electro-mechanical pressure senders had a significant added weight
attached to them. The story was that this was to lower the resonant
frequency below what the engine would excite to prevent them from
breaking off. Those engines run at twice the rpm that a Lycoming runs at.
ken
do not archive
Quote: | If
there is a high percentage of failures on the Rotax, I wonder if it's
caused by the very different frequency of vibration from the Rotax,
compared to most other engines running at constant-RPM.
Charlie
|
| - The Matronics AeroElectric-List Email Forum - | | Use the List Feature Navigator to browse the many List utilities available such as the Email Subscriptions page, Archive Search & Download, 7-Day Browse, Chat, FAQ, Photoshare, and much more:
http://www.matronics.com/Navigator?AeroElectric-List |
|
|
|
Back to top |
|
 |
rlborger(at)mac.com Guest
|
Posted: Thu Feb 13, 2014 5:41 pm Post subject: engine pressure senders installation |
|
|
Charlie,
Yes, there are Al fittings on the sender in the pictures. They were only for test fitting purposes. Matter of fact, the installation ended up quite different from the build pictures. I ended up using a longer length of 666 which was routed over the engine to the sensor. It was covered in firesleeve & heat shield and tied off a couple times along the way. I also used steel fittings on the sensor. The aircraft is down for some repair work and Annual Condition Inspection so I was able to take some pictures today.
[img]cid:5A82E680-55F2-4062-A706-C04743AD60C9[/img]
[img]cid:E14A28D5-58F4-43DA-9410-C9006979AA2B[/img]
Vibration transmitted to the sensor is pretty close to zero.
The oil pressure senders died from internal failures. The either stopped sending or sent invalid readings. There were no physical failures of the attachment to the engine. Those only seemed to occur when additional fittings were installed between the sender and oil pump.
As was pointed out in another e-mail, a brass weight ring was added to the sender to modify the harmonic frequency and reduce vibration issues. I don’t know if this was effective or not. Haven’t seen any complaints of oil pressure sender failures for a couple year.
Yes, there are much different vibration issues with the Rotax. Cruise RPM in a 91X is 5000 to 5500 RPM. There’s a 2.43:1 gearbox to the prop so it is turning at .41 of the engine speed. All these things make for a challenging vibrational environment.
I’m presently building a Little Toot Sport Biplane and I will probably direct mount the oil pressure sender to the engine as it is a Lycoming IO-320.
Blue skies & tailwinds,
Bob Borger
Europa XS Tri, Rotax 914, Airmaster C/S Prop (50 hrs).
Little Toot Sport Biplane, Lycoming Thunderbolt AEIO-320 EXP
3705 Lynchburg Dr.
Corinth, TX 76208-5331
Cel: 817-992-1117
rlborger(at)mac.com (rlborger(at)mac.com)
On Feb 13, 2014, at 12:56 PM, Charlie England <ceengland7(at)gmail.com (ceengland7(at)gmail.com)> wrote:
--> AeroElectric-List message posted by: Charlie England <ceengland7(at)gmail.com (ceengland7(at)gmail.com)>
Hi Bob,
I do understand worrying about stress & vibration issues. What caught my attention was what appeared to be aluminum adapters on the pressure sensor itself, cantilevering the right angle adapter and hose away from the sensor's mount. I could imagine the aluminum adapters being at risk more than the steel threaded sensor.
What was the nature of the failures? I was envisioning the sender breaking off at the threads. Was it some sort of internal failure, instead? Most current RV-x builders do remote mount the sensor, but they seem to survive on a lot of motors when they are direct- mounted. If there is a high percentage of failures on the Rotax, I wonder if it's caused by the very different frequency of vibration from the Rotax, compared to most other engines running at constant-RPM.
Charlie
| - The Matronics AeroElectric-List Email Forum - | | Use the List Feature Navigator to browse the many List utilities available such as the Email Subscriptions page, Archive Search & Download, 7-Day Browse, Chat, FAQ, Photoshare, and much more:
http://www.matronics.com/Navigator?AeroElectric-List |
|
Description: |
|
Filesize: |
55.97 KB |
Viewed: |
5760 Time(s) |
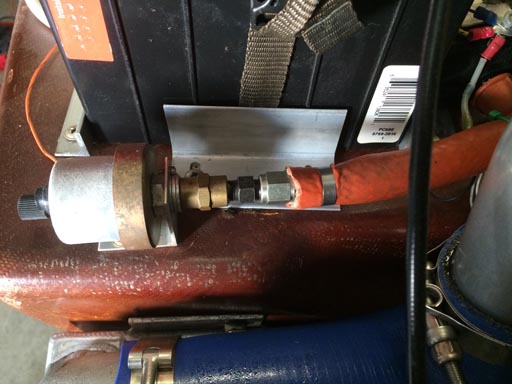
|
Description: |
|
Filesize: |
55.93 KB |
Viewed: |
5760 Time(s) |

|
|
|
Back to top |
|
 |
nuckolls.bob(at)aeroelect Guest
|
Posted: Fri Feb 14, 2014 10:31 am Post subject: engine pressure senders installation |
|
|
At 12:56 PM 2/13/2014, you wrote:
Quote: |
<ceengland7(at)gmail.com>
Hi Bob,
What was the nature of the failures? I was envisioning the sender
breaking off at the threads.
|
Yes . . . that's the bottom end of the moment arm
upon which mass of the attached hardware is vibrated.
Quote: | Was it some sort of internal failure, instead? Most current RV-x
builders do remote mount the sensor, but they seem to survive on a
lot of motors when they are direct- mounted. If there is a high
percentage of failures on the Rotax, I wonder if it's caused by the
very different frequency of vibration from the Rotax, compared to
most other engines running at constant-RPM.
|
The short, low mass sensor is just fine threaded into
it's designated port on the engine. It's the extension
with non-ferrous materials and adding more mass on the
end that sets up the scenario for failure.
Bob . . .
| - The Matronics AeroElectric-List Email Forum - | | Use the List Feature Navigator to browse the many List utilities available such as the Email Subscriptions page, Archive Search & Download, 7-Day Browse, Chat, FAQ, Photoshare, and much more:
http://www.matronics.com/Navigator?AeroElectric-List |
|
|
|
Back to top |
|
 |
|
|
You cannot post new topics in this forum You cannot reply to topics in this forum You cannot edit your posts in this forum You cannot delete your posts in this forum You cannot vote in polls in this forum You cannot attach files in this forum You can download files in this forum
|
Powered by phpBB © 2001, 2005 phpBB Group
|