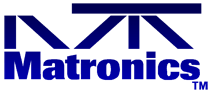 |
Matronics Email Lists Web Forum Interface to the Matronics Email Lists
|
View previous topic :: View next topic |
Author |
Message |
goodings(at)yorku.ca Guest
|
Posted: Sun Nov 26, 2006 9:39 am Post subject: Torquing GSC Propeller Bolts |
|
|
Our CH601HD Zodiac with a Rotax 912S 100 HP engine has a 68-inch, 3-blade
GSC wooden prop. In our installation, there is a prop flange extension.
The prop is held on by 6 1/4-inch bolts (3 through the aluminum blade
roots), and by 6 5/16-inch bolts onto the flange extension. GSC Systems
says use 100 inch pounds of torque for the 1/4 inch bolts, and 140 for the
5/16; these values are critical. Normally, with a washer under both the
head and the nut, one holds the bolt head stationary, and torques the
nylon lock nut; these nyloks are the preferred nuts recommended by GSC.
Because of the design of the prop flange extension, it is not possible to
get the torque wrench onto the nuts. Thus, one holds the nut stationary,
and torques the bolt head. THIS IS NOT THE SAME THING. My son Peter
(co-builder of our aircraft, and a professional mechanical engineer) knows
from practical experience that putting the torque wrench on the bolt head
can undertorque the nut by possibly 20-30%, or even more. It stands to
reason: the bolt shaft (or grip) inevitably experiences some friction in
passing through the parts being bolted together on the way to the nut.
There is a little part called a "crow's foot" to overcome this difficulty,
which goes over the nut, extends radially outward for about an inch, and
has a square hole for attachment of the torque wrench. It happened that I
had always torqued the prop bolts on our aircraft. In setting out to
retorque the bolts yesterday because the weather is now turning cold,
Peter realized right away that there was a problem. I had never used a
crow's foot (I did not know of their existence!). I'm guessing that many
others using this Rotax/GSC prop installation were also unaware of this
problem. What have others done about this? Were they aware of the
problem?
John Goodings, C-FGPJ, CH601HD with R912S, Toronto/Ottawa/Waterloo
| - The Matronics Zenith-List Email Forum - | | Use the List Feature Navigator to browse the many List utilities available such as the Email Subscriptions page, Archive Search & Download, 7-Day Browse, Chat, FAQ, Photoshare, and much more:
http://www.matronics.com/Navigator?Zenith-List |
|
|
|
Back to top |
|
 |
webmaster(at)upac.ca Guest
|
Posted: Mon Nov 27, 2006 4:07 am Post subject: Torquing GSC Propeller Bolts |
|
|
John, I have a similar arrangement of a prop extension on my 601HD but I'm using a 68" Warp Drive prop.
My extension is a simpler arrangement of a heavy walled 6061 tube with match drilled holes that use long prop bolts to directly bolts the whole thing to the prop flange. The main concern on mine is not stripping the threads on either the bolts or the prop flange cause neither are cheap to replace! Rotax recommends a max of 94 ft/Lbs on the prop flange according to my manual. My bolts extend enough past the prop flange to have washers and nuts on the back to keep things from backing out.
Trev Page
C-IDUS 601HD R912
On Nov 26, 2006, at 12:37 PM, John M. Goodings wrote:
[quote]--> Zenith-List message posted by: "John M. Goodings" <goodings(at)yorku.ca (goodings(at)yorku.ca)>
Our CH601HD Zodiac with a Rotax 912S 100 HP engine has a 68-inch, 3-blade
GSC wooden prop. In our installation, there is a prop flange extension.
The prop is held on by 6 1/4-inch bolts (3 through the aluminum blade
roots), and by 6 5/16-inch bolts onto the flange extension. GSC Systems
says use 100 inch pounds of torque for the 1/4 inch bolts, and 140 for the
5/16; these values are critical. Normally, with a washer under both the
head and the nut, one holds the bolt head stationary, and torques the
nylon lock nut; these nyloks are the preferred nuts recommended by GSC.
Because of the design of the prop flange extension, it is not possible to
get the torque wrench onto the nuts. Thus, one holds the nut stationary,
and torques the bolt head. THIS IS NOT THE SAME THING. My son Peter
(co-builder of our aircraft, and a professional mechanical engineer) knows
from practical experience that putting the torque wrench on the bolt head
can undertorque the nut by possibly 20-30%, or even more. It stands to
reason: the bolt shaft (or grip) inevitably experiences some friction in
passing through the parts being bolted together on the way to the nut.
There is a little part called a "crow's foot" to overcome this difficulty,
which goes over the nut, extends radially outward for about an inch, and
has a square hole for attachment of the torque wrench. It happened that I
had always torqued the prop bolts on our aircraft. In setting out to
retorque the bolts yesterday because the weather is now turning cold,
Peter realized right away that there was a problem. I had never used a
crow's foot (I did not know of their existence!). I'm guessing that many
others using this Rotax/GSC prop installation were also unaware of this
problem. What have others done about this? Were they aware of the
problem?
John Goodings, C-FGPJ, CH601HD with R912S, Toronto/Ottawa/Waterloo
-- Please Support Your Lists This Month --
(And Get Some AWESOME FREE Gifts!)
November is the Annual List Fund Raiser. Click on
the Contribution link below to find out more about
this year's Terrific Free Incentive Gifts provided
by:
* AeroElectric www.aeroelectric.com
* The Builder's Bookstore www.buildersbooks.com
* Aeroware Enterprises www.kitlog.com
* HomebuiltHELP www.homebuilthelp.com
List Contribution Web Site
--> http://www.matronics.com/contribution
Thank you for your generous support!
-Matt Dralle, List Admin.
- The Zenith-List Email Forum -
--> http://www.matronics.com/Navigator?Zenith-List
[b]
| - The Matronics Zenith-List Email Forum - | | Use the List Feature Navigator to browse the many List utilities available such as the Email Subscriptions page, Archive Search & Download, 7-Day Browse, Chat, FAQ, Photoshare, and much more:
http://www.matronics.com/Navigator?Zenith-List |
|
|
|
Back to top |
|
 |
n801bh(at)netzero.com Guest
|
Posted: Mon Nov 27, 2006 5:43 am Post subject: Torquing GSC Propeller Bolts |
|
|
I think you mean 94 "inch" pounds, not foot pounds. That foot lb torque would crush the prop hub and need 5/8+ prop bolts...
do not archive
Ben Haas
N801BH
www.haaspowerair.com
-- Trevor Page <webmaster(at)upac.ca> wrote:
John, I have a similar arrangement of a prop extension on my 601HD but I'm using a 68" Warp Drive prop.
My extension is a simpler arrangement of a heavy walled 6061 tube with match drilled holes that use long prop bolts to directly bolts the whole thing to the prop flange. The main concern on mine is not stripping the threads on either the bolts or the prop flange cause neither are cheap to replace! Rotax recommends a max of 94 ft/Lbs on the prop flange according to my manual. My bolts extend enough past the prop flange to have washers and nuts on the back to keep things from backing out.
Trev Page
C-IDUS 601HD R912
On Nov 26, 2006, at 12:37 PM, John M. Goodings wrote:
[quote] --> Zenith-List message posted by: "John M. Goodings" <goodings(at)yorku.ca (goodings(at)yorku.ca)>
Our CH601HD Zodiac with a Rotax 912S 100 HP engine has a 68-inch, 3-blade
GSC wooden prop. In our installation, there is a prop flange extension.
The prop is held on by 6 1/4-inch bolts (3 through the aluminum blade
roots), and by 6 5/16-inch bolts onto the flange extension. GSC Systems
says use 100 inch pounds of torque for the 1/4 inch bolts, and 140 for the
5/16; these values are critical. Normally, with a washer under both the
head and the nut, one holds the bolt head stationary, and torques the
nylon lock nut; these nyloks are the preferred nuts recommended by GSC.
Because of the design of the prop flange extension, it is not possible to
get the torque wrench onto the nuts. Thus, one holds the nut stationary,
and torques the bolt head. THIS IS NOT THE SAME THING. My son Peter
(co-builder of our aircraft, and a professional mechanical engineer) knows
from practical experience that putting the torque wrench on the bolt head
can undertorque the nut by possibly 20-30%, or even more. It stands to
reason: the bolt shaft (or grip) inevitably experiences some friction in
passing through the parts being bolted together on the way to the nut.
There is a little part called a "crow's foot" to overcome this difficulty,
which goes over the nut, extends radially outward for about an inch, and
has a square hole for attachment of the torque wrench. It happened that I
had always torqued the prop bolts on our aircraft. In setting out to
retorque the bolts yesterday because the weather is now turning cold,
Peter realized right away that there was a problem. I had never used a
crow's foot (I did not know of their existence!). I'm guessing that many
others using this Rotax/GSC prop installation were also unaware of this
problem. What have others done about this? Were they aware of the
problem?
John Goodings, C-FGPJ, CH601HD with R912S, Toronto/Ottawa/Waterloo
(And Get Some AWESOME FREE Gifts!)
November is the Annual List Fund Raiser. Click on
this year's Terrific Free Incentive Gifts provided
* AeroElectric www.aeroelectric.com
www.buildersbooks.com
www.kitlog.com
www.homebuilthelp.com
List Contribution Web Site
--> http://www.matronics.com/contribution
Thank you for your generous support!
- The Zenith-List Email Forum -
--> http://www.matronics.com/Navigator?Zenith-List
http://www.matronics.com/contributi========================ics.com/Navigator?Zenith-List">http://www.matronics.com/Navigator?Zenith======================================== [/b]
[b]
| - The Matronics Zenith-List Email Forum - | | Use the List Feature Navigator to browse the many List utilities available such as the Email Subscriptions page, Archive Search & Download, 7-Day Browse, Chat, FAQ, Photoshare, and much more:
http://www.matronics.com/Navigator?Zenith-List |
|
|
|
Back to top |
|
 |
webmaster(at)upac.ca Guest
|
Posted: Mon Nov 27, 2006 12:34 pm Post subject: Torquing GSC Propeller Bolts |
|
|
Actually Ben the Rotax manual does say 94 foot/lbs of torque on the prop flange bolts...(most likely a typo which is not unusual)
Warp Drive says to torque the 8mm prop bolts to 175 inch/lbs
Trev Page
C-IDUS 601HD R912
On Nov 27, 2006, at 1:41 PM, n801bh(at)netzero.com (n801bh(at)netzero.com) wrote:
[quote]
I think you mean 94 "inch" pounds, not foot pounds. That foot lb torque would crush the prop hub and need 5/8+ prop bolts...
do not archive
Ben Haas
N801BH
www.haaspowerair.com
-- Trevor Page <webmaster(at)upac.ca (webmaster(at)upac.ca)> wrote:
John, I have a similar arrangement of a prop extension on my 601HD but I'm using a 68" Warp Drive prop.
My extension is a simpler arrangement of a heavy walled 6061 tube with match drilled holes that use long prop bolts to directly bolts the whole thing to the prop flange. The main concern on mine is not stripping the threads on either the bolts or the prop flange cause neither are cheap to replace! Rotax recommends a max of 94 ft/Lbs on the prop flange according to my manual. My bolts extend enough past the prop flange to have washers and nuts on the back to keep things from backing out.
Trev Page
C-IDUS 601HD R912
On Nov 26, 2006, at 12:37 PM, John M. Goodings wrote:
Quote: | --> Zenith-List message posted by: "John M. Goodings" <goodings(at)yorku.ca (goodings(at)yorku.ca)>
Our CH601HD Zodiac with a Rotax 912S 100 HP engine has a 68-inch, 3-blade
GSC wooden prop. In our installation, there is a prop flange extension.
The prop is held on by 6 1/4-inch bolts (3 through the aluminum blade
roots), and by 6 5/16-inch bolts onto the flange extension. GSC Systems
says use 100 inch pounds of torque for the 1/4 inch bolts, and 140 for the
5/16; these values are critical. Normally, with a washer under both the
head and the nut, one holds the bolt head stationary, and torques the
nylon lock nut; these nyloks are the preferred nuts recommended by GSC.
Because of the design of the prop flange extension, it is not possible to
get the torque wrench onto the nuts. Thus, one holds the nut stationary,
and torques the bolt head. THIS IS NOT THE SAME THING. My son Peter
(co-builder of our aircraft, and a professional mechanical engineer) knows
from practical experience that putting the torque wrench on the bolt head
can undertorque the nut by possibly 20-30%, or even more. It stands to
reason: the bolt shaft (or grip) inevitably experiences some friction in
passing through the parts being bolted together on the way to the nut.
There is a little part called a "crow's foot" to overcome this difficulty,
which goes over the nut, extends radially outward for about an inch, and
has a square hole for attachment of the torque wrench. It happened that I
had always torqued the prop bolts on our aircraft. In setting out to
retorque the bolts yesterday because the weather is now turning cold,
Peter realized right away that there was a problem. I had never used a
crow's foot (I did not know of their existence!). I'm guessing that many
others using this Rotax/GSC prop installation were also unaware of this
problem. What have others done about this? Were they aware of the
problem?
John Goodings, C-FGPJ, CH601HD with R912S, Toronto/Ottawa/Waterloo
< 0px; margin-bottom: margin-right: margin-top:>(And Get Some AWESOME FREE Gifts!)
November is the Annual List Fund Raiser. Click on
< 0px; margin-bottom: margin-right: margin-top:>this year's Terrific Free Incentive Gifts provided
* AeroElectric www.aeroelectric.com
www.buildersbooks.com
www.kitlog.com
www.homebuilthelp.com
List Contribution Web Site
< 0px; margin-bottom: margin-right: margin-top:>--> http://www.matronics.com/contribution
< 0px; margin-bottom: margin-right: margin-top:>Thank you for your generous support!
- The Zenith-List Email Forum -
--> http://www.matronics.com/Navigator?Zenith-List
www.homebuilthelp.comtp://www.matronics.com/contribution">http://www.matronics.com/contributi========================ics.com/Navigator?Zenith-List">http://www.matronics.com/Navigator?Zenith===============
href="http://www.aeroelectric.com">www.aeroelectric.com
href="http://www.buildersbooks.com">www.buildersbooks.com
href="http://www.kitlog.com">www.kitlog.com
href="http://www.homebuilthelp.com">www.homebuilthelp.com
href="http://www.matronics.com/contribution">http://www.matronics.com/contribution
href="http://www.matronics.com/Navigator?Zenith-List">http://www.matronics.com/Navigator?Zenith-List
| [b]
| - The Matronics Zenith-List Email Forum - | | Use the List Feature Navigator to browse the many List utilities available such as the Email Subscriptions page, Archive Search & Download, 7-Day Browse, Chat, FAQ, Photoshare, and much more:
http://www.matronics.com/Navigator?Zenith-List |
|
|
|
Back to top |
|
 |
mrbizi(at)yahoo.com Guest
|
Posted: Mon Nov 27, 2006 1:08 pm Post subject: Torquing GSC Propeller Bolts |
|
|
Has everyone seen this?
Crash kills aviation enthusiast; Pellien was only one aboard aircraft when it went down in woods near Bryce
by John Collins
As darkness settled over western Shenandoah County, firefighters and rescue workers stood along the winding Greenview Drive near Bryce Resort. A hoseline was ready, but it wasn’t needed.
All the emergency crews could do was wait as five members of the Virginia State Police started an investigation.
The workers were on the scene of a plane crash that took the life of James J. “Jim” Pellien. State police identified the 58-year-old man as a resident of Alexandria, but resort residents said that Pellien had a house at Bryce.
The state police are investigating the crash, led by Trooper A.S. Waybright. Also studying the crash are the Federal Aviation Administration (FAA) and the National Transportation Safety Board (NTSB).
Authorities released little information about the circumstances of the crash, which occurred at 4:30 p.m. Saturday.
“The aircraft struck trees returning to the airport under unknown circumstances,” said Todd Gunther, an air safety investigator with the NTSB.
On Monday, the fixed-wing aircraft, a Czech-made two-seater propeller plane, remained on the steep hillside where it crashed Saturday. Yellow crime scene tape surrounded the wreckage, about 1 mile northeast of the Sky Bryce Airport.
NTSB investigators hoped to remove the plane later in the day to take it to a secure, undisclosed location for an in-depth inspection.
The plane, commonly called a Zodiac CH601, was upright, facing down the hill among trees and briars. The canopy was shattered, and the wings and tail were mangled.
One of the propeller’s three blades stood straight up, unbent. Everything appeared to be contained to an area of roughly 400 square feet.
While authorities had little to say about the circumstances surrounding the crash, residents in the area shared their observations.
Helen Burton lives down the street from the crash site. She had her kitchen door open because of the unseasonably warm weather Saturday.
She said that it’s not unusual for planes to fly over her house.
“I seem to be in a flight pattern,” Burton said.
The plane went over, and Burton noticed a change in the plane’s sound.
“I was aware that it was not as loud as it was,” she said.
Then came a “very loud” crash, Burton said.
Burton’s neighbor, Lisa Dellinger, also heard the crash, but didn’t immediately realize what she’d heard.
“I heard what I thought was multiple gunshots, because it’s hunting season, but unfortunately, it was the crash,” Dellinger said, looking over the scene from a neighbor’s house.
Burton called Dellinger after hearing the crash.
“I said, ‘I don’t think it was a gunshot. I think it was a plane crash,” Burton said.
Weather did not appear to be a factor in the crash, according to Gunther, who said that there was a 10-mile visibility at the time of the crash. That meant that pilots could fly under visual flight rules (VFR), where they can rely on their vision and not on their instrument panel.
“In other words, the weather was good,” Gunther said.
Saturday’s crash was the second CH601 accident in the U.S. in November. On Nov. 4, two people died in California when their plane went down in what witnesses described as an explosion.
There was no fire in Saturday’s crash, Gunther said.
Aviation enthusiast
Pellien was a man who loved to fly, and who loved to get others in the air, according to Bryce residents.
Pellien’s CH601, built by Czech Aircraft Works in 2005, was the first plane to earn the FAA’s special light-sport aircraft certificate.
Light sport planes were a major part of Pellien’s last years. He owned a business at Sky Bryce Airport, Mid-Atlantic Sports Planes, which he used to sell the planes. Sport planes have less restrictive rules for pilot licensing than do traditional private airplanes.
He also ran a flight school, which was featured in Popular Mechanics one year ago. The flight school offered would-be pilots the chance to earn their sport pilot license in as little as one week.
This past September, Pellien organized an airshow of sport planes at the airport.
After New York Yankees pitcher Cory Lidle died when his plane crashed into a Manhattan high-rise building, the Wall Street Journal did a story on the sport pilot licenses. In the story, Pellien was interviewed about the fact that sport pilots don’t have to pass as many physical criteria for their licenses.
He compared the process to what truckers face, using it as an opportunity to point out what he felt was an inequity for pilots.
“Truckers only need a driver’s license,” Pellien told the Wall Street Journal. “But before sport-pilot licenses, you had to have a special medical certificate to fly a small aircraft less than half the size of an SUV.”
Back at Bryce on Monday, clouds made for a dismal day. But residents remembered Pellien’s love for flying.
Kevin Urbine attended Our Lady of the Shenandoah Catholic Church with Pellien.
“He loved flying. I know that,” he said.
In fact, according to Urbine, it’s both fortunate and unusual that nobody was with Pellien in the plane when it went down.
“[It’s] surprising he didn’t have someone else with him,” Urbine said.
NTSB investigates
The National Transportation Safety Board is tasked by Congress with investigating every civil aviation accident that results in substantial damage or serious injury. That amounts to approximately 2,000 investigations per year, Gunther said.
The agency’s goal, he said, is to find the cause of the accident and examine the “facts, conditions and circumstances that relate to a transportation accident.”
Three NTSB investigators and an FAA representative responded to the crash site Saturday night from Washington, D.C. They conducted field investigations that night and all day Sunday, Gunther said.
The on-site investigation features interviews with ear and eyewitnesses, as well as examining the crash site through photos, measurements and plenty of note-taking.
Eventually, the NTSB workers will examine everything that could have contributed to the crash, including the aircraft’s structure, assembly and fuel, control and hydraulic systems. They will look at the weather and the terrain of the crash site, as well as the performance and health of the pilot.
“We don’t eliminate anything,” Gunther said.
In the first seven to 10 days after the accident, the NTSB will release a preliminary report. Six to nine months later, they will release a longer factual report, which will be followed in 30 to 60 days by a statement of probable cause.
The last fatal aviation accident in Shenandoah County was in May of 2001 when a plane suffered engine failure and came up short of an emergency landing at New Market Airport.
Trevor Page <webmaster(at)upac.ca> wrote:
[quote] Actually Ben the Rotax manual does say 94 foot/lbs of torque on the prop flange bolts...(most likely a typo which is not unusual)
Warp Drive says to torque the 8mm prop bolts to 175 inch/lbs
Trev Page
C-IDUS 601HD R912
On Nov 27, 2006, at 1:41 PM, n801bh(at)netzero.com (n801bh(at)netzero.com) wrote:
[quote] I think you mean 94 "inch" pounds, not foot pounds. That foot lb torque would crush the prop hub and need 5/8+ prop bolts...
do not archive
Ben Haas
N801BH
www.haaspowerair.com
-- Trevor Page <webmaster(at)upac.ca (webmaster(at)upac.ca)> wrote:
John, I have a similar arrangement of a prop extension on my 601HD but I'm using a 68" Warp Drive prop.
My extension is a simpler arrangement of a heavy walled 6061 tube with match drilled holes that use long prop bolts to directly bolts the whole thing to the prop flange. The main concern on mine is not stripping the threads on either the bolts or the prop flange cause neither are cheap to replace! Rotax recommends a max of 94 ft/Lbs on the prop flange according to my manual. My bolts extend enough past the prop flange to have washers and nuts on the back to keep things from backing out.
Trev Page
C-IDUS 601HD R912
On Nov 26, 2006, at 12:37 PM, John M. Goodings wrote:
[quote] --> Zenith-List message posted by: "John M. Goodings" <goodings(at)yorku.ca (goodings(at)yorku.ca)>
Our CH601HD Zodiac with a Rotax 912S 100 HP engine has a 68-inch, 3-blade
GSC wooden prop. In our installation, there is a prop flange extension.
The prop is held on by 6 1/4-inch bolts (3 through the aluminum blade
roots), and by 6 5/16-inch bolts onto the flange extension. GSC Systems
says use 100 inch pounds of torque for the 1/4 inch bolts, and 140 for the
5/16; these values are critical. Normally, with a washer under both the
head and the nut, one holds the bolt head stationary, and torques the
nylon lock nut; these nyloks are the preferred nuts recommended by GSC.
Because of the design of the prop flange extension, it is not possible to
get the torque wrench onto the nuts. Thus, one holds the nut stationary,
and torques the bolt head. THIS IS NOT THE SAME THING. My son Peter
(co-builder of our aircraft, and a professional mechanical engineer) knows
from practical experience that putting the torque wrench on the bolt head
can undertorque the nut by possibly 20-30%, or even more. It stands to
reason: the bolt shaft (or grip) inevitably experiences some friction in
passing through the parts being bolted together on the way to the nut.
There is a little part called a "crow's foot" to overcome this difficulty,
which goes over the nut, extends radially outward for about an inch, and
has a square hole for attachment of the torque wrench. It happened that I
had always torqued the prop bolts on our aircraft. In setting out to
retorque the bolts yesterday because the weather is now turning cold,
Peter realized right away that there was a problem. I had never used a
crow's foot (I did not know of their existence!). I'm guessing that many
others using this Rotax/GSC prop installation were also unaware of this
problem. What have others done about this? Were they aware of the
problem?
John Goodings, C-FGPJ, CH601HD with R912S, Toronto/Ottawa/Waterloo
< 0px; margin-bottom: margin-right: margin-top:>(And Get Some AWESOME FREE Gifts!)
November is the Annual List Fund Raiser. Click on
< 0px; margin-bottom: margin-right: margin-top:>this year's Terrific Free Incentive Gifts provided
* AeroElectric www.aeroelectric.com
www.buildersbooks.com
www.kitlog.com
www.homebuilthelp.com
List Contribution Web Site
< 0px; margin-bottom: margin-right: margin-top:>--> http://www.matronics.com/contribution
< 0px; margin-bottom: margin-right: margin-top:>Thank you for your generous support!
- The Zenith-List Email Forum -
--> http://www.matronics.com/Navigator?Zenith-List
www.homebuilthelp.comtp://www.matronics.com/contribution">http://www.matronics.com/contributi========================ics.com/Navigator?Zenith-List">http://www.matronics.com/Navigator?Zenith===============
href="http://www.aeroelectric.com">www.aeroelectric.com href="http://www.buildersbooks.com">www.buildersbooks.com href="http://www.kitlog.com">www.kitlog.com href="http://www.homebuilthelp.com">www.homebuilthelp.com href="http://www.matronics.com/contribution">http://www.matronics.com/contribution href="http://www.matronics.com/Navigator?Zenith-List">http://www.matronics.com/Navigator?Zenith-List
| - The Matronics Zenith-List Email Forum - | | Use the List Feature Navigator to browse the many List utilities available such as the Email Subscriptions page, Archive Search & Download, 7-Day Browse, Chat, FAQ, Photoshare, and much more:
http://www.matronics.com/Navigator?Zenith-List |
|
|
|
Back to top |
|
 |
Float Flyr
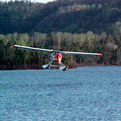
Joined: 19 Jul 2006 Posts: 2704 Location: Campbellton, Newfoundland
|
Posted: Mon Nov 27, 2006 5:39 pm Post subject: Torquing GSC Propeller Bolts |
|
|
Don't forget to calibrate the torque wrench before torquing down the bolts. in the meantime check with the folks at Rotax to verify the max torque on the flange.... 94 inch pounds seems a bit slight. 94 ft. lb. way over the top! Unless you are talking about the torque required to mount the flange to the crank.
Noel [quote]
--
| - The Matronics Zenith-List Email Forum - | | Use the List Feature Navigator to browse the many List utilities available such as the Email Subscriptions page, Archive Search & Download, 7-Day Browse, Chat, FAQ, Photoshare, and much more:
http://www.matronics.com/Navigator?Zenith-List |
|
_________________ Noel Loveys
Kitfox III-A
Aerocet 1100 Floats |
|
Back to top |
|
 |
|
|
You cannot post new topics in this forum You cannot reply to topics in this forum You cannot edit your posts in this forum You cannot delete your posts in this forum You cannot vote in polls in this forum You cannot attach files in this forum You can download files in this forum
|
Powered by phpBB © 2001, 2005 phpBB Group
|