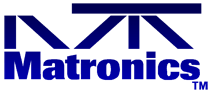 |
Matronics Email Lists Web Forum Interface to the Matronics Email Lists
|
View previous topic :: View next topic |
Author |
Message |
darinh
Joined: 20 Apr 2006 Posts: 327 Location: Utah
|
Posted: Sun Jul 06, 2008 9:35 pm Post subject: Nippondenso alternator question |
|
|
This is my last question...at least for tonight. I have a Rotax 914 and the onboard generator is not enough so I added a optional 40 amp nippondenso alternator. It has the alt. output and a plug labeled "L" and "IG". I assume the "IG" is the field circuit and the "L" is obviously the lamp circuit.
The question is this: I have been told that the alt. must have the indicator lamp installed for it to charge the battery. I don't really want to add another "idiot" light to my panel as I already had two for the turbo control unit and one for my GRT EIS. Can I run it through the EIS light or will this screw it up? If I have to have a light, I may just mount it behind the panel. Lastly, I was told this light cannot be an LED...is this also correct?
| - The Matronics AeroElectric-List Email Forum - | | Use the List Feature Navigator to browse the many List utilities available such as the Email Subscriptions page, Archive Search & Download, 7-Day Browse, Chat, FAQ, Photoshare, and much more:
http://www.matronics.com/Navigator?AeroElectric-List |
|
_________________ Darin Hawkes
Series 7
914 Turbo
Kaysville, Utah |
|
Back to top |
|
 |
info(at)mtfind.com Guest
|
Posted: Mon Jul 07, 2008 6:22 am Post subject: Nippondenso alternator question |
|
|
Depends on the specific ND alternator. The ones I have experience with have
a switch (internal to the regulator) that provides a ground at the "L"
terminal where (in automobiles) an "Idiot Light" is connected across the "L"
to the"IG" and indicates the alternator is getting power to the "IG terminal
but the Alternator's "B" lead Voltage is not high enough to charge the
battery. The ground is removed (and the light goes out) when the alternator
starts supplying power. There are apparently some ND alternators that use
the "L" terminal to power the internal regulator and in that case the "L"
must have a specific light connected to provide starting voltage. In that
case the light is powered by the regulator current before the power from the
"B" lead takes over and the light goes out indicating the alternator is
working properly. I have never seen that type of ND alternator but there are
a few people on other groups who state the Light is required or the
alternator will not provide power. If your alternator requires a light it
should be the light specified in the original application. This provides the
proper current to the regulator.
The only ND alternators I have data for shows the "L" terminal as a simple
switch to ground and personal testing shows the alternator can be turned on
and off while running with no connection to the "L" lead (simply switching
power to the "IG" connection. Turning the alternator off under power is not
recommended as that causes an alternator "load dump" which may damage the
alternator if its disconnected under higher amp charging current. Hasent
happened to me up to a tested 40 amp load dump but still to be avoided
except when the alternator regulator fails high "B" terminal voltage. The
addition of a transorb of sufficient power will shunt the load dump and
protect the alternator but that is a different topic.
ND alternators come in many versions of internal regulators, some sense the
charging voltage thru the IG terminal to accurately charge the battery based
on the battery terminal voltage not the "B: lead voltage.
Thus as originally designed for auto use, the "B" lead is hard wired
directly to the battery. The IGN switch is turned on before starting and the
"idiot light" is powered by the "IG" power input and the regulator internal
ground. There is no requirement for the "L" terminal to be connected to
anything (at least with the ND alternators I have evaluated). If there is a
connection it must limit the current as the internal ground switch may
require external current limiting. In an aircraft application generally
there is no need for any connection to the "L" terminal as the alternator
wiring and its current generation is monitored in a different method. Be
sure your design provides a connection to the battery before starting the
engine.
Sorry but perhaps the supplier of the alternator can tell you. If you
purchased the add on alternator as a specific Kit for your engine. In any
event If the light is required you must install the proper one. Do not
connect the "L" terminal to any thing else other than the proper bulb. Not
an LED as if a light is required the LED with limiting resistor will not
pass enough current and clearly nothing else. If the light is not required
(my personal experience its not) then there is no need if you have other
ways to tell if the alternator is functioning properly like current monitor
or bus voltage. The ND alternator generally requires approx 1500 alternator
RPM to start generation. In an automobile this is generally around the just
above idle rpm of the engine and again in an auto the idiot light can turn
on at slow idle and go out just above that rpm.
Paul
---
| - The Matronics AeroElectric-List Email Forum - | | Use the List Feature Navigator to browse the many List utilities available such as the Email Subscriptions page, Archive Search & Download, 7-Day Browse, Chat, FAQ, Photoshare, and much more:
http://www.matronics.com/Navigator?AeroElectric-List |
|
|
|
Back to top |
|
 |
nuckolls.bob(at)cox.net Guest
|
Posted: Wed Jul 09, 2008 1:36 pm Post subject: Nippondenso alternator question |
|
|
At 10:35 PM 7/6/2008 -0700, you wrote:
Quote: |
This is my last question...at least for tonight. I have a Rotax 914 and
the onboard generator is not enough so I added a optional 40 amp
nippondenso alternator. It has the alt. output and a plug labeled "L" and
"IG". I assume the "IG" is the field circuit and the "L" is obviously the
lamp circuit.
The question is this: I have been told that the alt. must have the
indicator lamp installed for it to charge the battery.
|
Some do, some don't try it without and if the alternator doesn't come
on line, hook a 100 ohm, 1w resistor between "L" and "IG". The IG
terminal is a control lead only that will tell the alternator to come
on line when +12 is applied to the terminal and assuming the alternator
is spinning. Again, depending on the whims of the designers of the
regulator, REMOVING voltage from IG may or may not turn the alternator
OFF. You'll just have to try it an see how your particular
device operates.
Quote: | I don't really want to add another "idiot" light to my panel as I
already had two for the turbo control unit and one for my GRT EIS. Can I
run it through the EIS light or will this screw it up? If I have to have
a light, I may just mount it behind the panel. Lastly, I was told this
light cannot be an LED...is this also correct?
|
Use the resistor crimped right into the spade terminals
at the back of the alternator.
Bob . . .
----------------------------------------)
( . . . a long habit of not thinking )
( a thing wrong, gives it a superficial )
( appearance of being right . . . )
( )
( -Thomas Paine 1776- )
----------------------------------------
| - The Matronics AeroElectric-List Email Forum - | | Use the List Feature Navigator to browse the many List utilities available such as the Email Subscriptions page, Archive Search & Download, 7-Day Browse, Chat, FAQ, Photoshare, and much more:
http://www.matronics.com/Navigator?AeroElectric-List |
|
|
|
Back to top |
|
 |
nuckolls.bob(at)cox.net Guest
|
Posted: Wed Jul 09, 2008 1:37 pm Post subject: Nippondenso alternator question |
|
|
At 07:17 AM 7/7/2008 -0700, you wrote:
Quote: |
Depends on the specific ND alternator. The ones I have experience with have
a switch (internal to the regulator) that provides a ground at the "L"
terminal where (in automobiles) an "Idiot Light" is connected across the "L"
to the"IG" and indicates the alternator is getting power to the "IG terminal
but the Alternator's "B" lead Voltage is not high enough to charge the
battery. The ground is removed (and the light goes out) when the alternator
|
<snip>
Quote: | or bus voltage. The ND alternator generally requires approx 1500 alternator
RPM to start generation. In an automobile this is generally around the just
above idle rpm of the engine and again in an auto the idiot light can turn
on at slow idle and go out just above that rpm.
Paul
|
There's much good data in this posting . . . enough to give it
some credibility . . . but some absolute errors too. This has
been discussed many times in the past and I won't spend any
more time on it now. Suggest interested readers search the
articles on the website and the archives on the List server.
Disinterested readers should disregard the posting in
its entirety.
Bob . . .
----------------------------------------)
( . . . a long habit of not thinking )
( a thing wrong, gives it a superficial )
( appearance of being right . . . )
( )
( -Thomas Paine 1776- )
----------------------------------------
| - The Matronics AeroElectric-List Email Forum - | | Use the List Feature Navigator to browse the many List utilities available such as the Email Subscriptions page, Archive Search & Download, 7-Day Browse, Chat, FAQ, Photoshare, and much more:
http://www.matronics.com/Navigator?AeroElectric-List |
|
|
|
Back to top |
|
 |
info(at)mtfind.com Guest
|
Posted: Wed Jul 09, 2008 5:50 pm Post subject: Nippondenso alternator question |
|
|
I agree that its been much discussed in the past however there are many
false and remaining incorrect mis stated comments in the past that simply do
not apply to the most common ND alternator. These false statements remain in
the past unchallenged but still remain not correct with respect to ND
alternators.
Other than MY having tested many ND alternators as well as a couple of other
brands of Internally regulated Japan brand alternators .I question your
accusation that I have made absolute errors (or any errors of any sort) in
my statements.
For example, all the ND alternators I have tested can be turned on and off
while running and producing power. They also can be "B" lead disconnected
under load with no damage to the alternator IF the alternator contacts are
rated properly ( the common often used contactor are not rated to disconnect
the load dump voltages). The addition of the proper contact voltage and
proper power rated transorb is required to protect any low voltage contactor
from arcing and passing the higher load dump voltage back to the bus. The
subject alternators have internal transorbs but may overheat under the long
contact bounce of the common contactor, in particular if that contactor has
a diode across the coil which extends the opening or the contact from around
5ms to as long as 50 ms with, in several cases, major arcing of dozens of
arc pulses. Using the industry recommended transorb across the contactor
coil minimizes the arcing and opening delay but does not resolve the contact
voltage rating which is overstressed and demonstrated to arc during my
testing. Its one of the repeatable tests that ranged from 2 amps to 40 amps
load
I have performed 100's of repeatable tests to support the analysis of the
above statements including the contact arcing under load of the common
contactor.. As well as fast opening and lack of arcing with the Kilovac in
"B" lead testing
My findings include ND alternators commonly used at the time by NSI, Vans
and others in the mid 1990's have the following features.
1. The IG terminal turns on and off the alternator under load.
Note Its safe as far as the alternator is concerned to turn off the
alternator under load. It must be done with properly rated contactors
however.
2, I have been unable to cause alternator failure even with arcing "B" lead
contactor. Both NSI and Vans at the time was selling rebuilt alternators and
Vans told customers not to use any type of "B" lead crowbar device due to
alternator failure.
Note: This I verified with a personal phone call at the time to Vans. I have
no evidence to suggest your OVP crowbar was the cause but I do suspect the
common contactor was a possible cause due to observed excessive contact
arcing during the extended opening of the contacts due in part to the simple
diode used and the contactor contact V rating.
3. No ND I tested locked up and could not be turned off at any time safely.
4. No ND required anything connected to the "L" terminal.
Clearly its not possible to test all of the hundreds of types of small shell
ND alternators. Further rebuilt alternators may have internal regulators
with difference performance as our application has the alternator wired
differently and the aftermarket rebuilt alternators may have regulators that
only work when installed in an automobile as the original application.
5. Its safe to open the "B" lead under load if the contactor is rated for at
least 200V contact rating. Only the KIlovac and similar HV contactors have
proper voltage ratings. The common contractors for 12V system battery and
starter etc have contacts only rated for under 50V max during the opening
process. They can tolerate higher voltage across the contacts when the
contacts are open. They will arc during the opening of an alternator load
and the result may cause damage to both the alternator and aircraft bus.
Do not use a common diode across a common contactor coil and do not use a
common 45V contactor contact rating as either or both actions greatly
increase of alternator damage
Perhaps you can substantiate your statements with some of your testing of
the commonly used ND alternator. Please provide the Lester number so we all
can verify your test results.
My reply to the questioner was intended to be general as he did not state
the exact ND Lester number and was it rebuilt or new. With out knowing that
there is no absolute recommendation on how to wire it up
Yes there are alternators of different brands (and perhaps some ND do also,
but not the common ones that I have tested.) that lock up and others that
require a lamp in the wiring to start. perhaps there are also other that
cannot survive a load dump but none in the industry will state that their
regulators lack the universal load dump internal protection (except that
load dumps resulting form extended arcing from contacts or broken wiring are
not protected as overheating or the protection Transorb is possible.
Your cheep un-substantiated comment that I have made absolute errors does
not suit your normally nice style. Lets keep the discussion technical and
not call me a person making false statements please.
No respectable person can let that cheep shot pass. If I made a error please
prove it. How many stock ND alternators used in aircraft have you tested????
Perhaps I missed it in the past and if so I apologize if you show me the
statement. It has been more than 10 years ago when many of my testing was
done and perhaps My memory has failed. To me the discussion on this years
ago was long settled with you on one side and Jet Pilot George (for one) on
the other side.
As side comment many regulators have a OVP built in that limits the output
voltage to around 16V. This will not protect against all failures thus an
external OVP is required. I have experienced 2 regulator failures (over the
past 50 years in autos where the output jumped from 14+ to 16V and held the
output there. One was the common external regulatro YOU long have
recommended as a low cost "ford" style.
Please do not reply and waste bandwidth and all of our time unless you have
specific test data to prove your response. Past history posts that do not
include backed up with actual testing ase just opinion and not worth
considering.
Paul
PS: I do not want to start another often widening discussion. Perhaps I
should have remained silent but you stated you were out of town and I have
had a lot of experience including some from other groups (who in error) make
general statements that ND alternators require a light across the IG and L
connections. Further I have had the impression you have yet to test any
internal ND or any other brand alternator. This was to be done after you had
the test stand up and running.
I have witnessed and peer reviewed test setup and test results to support
the above statements. Only the conclusions have ever been document as I felt
at the time there was no reason to do more than I did. I simply am not
interested in trying to prove anything to anything just pass on real test
results that proved how the auto internal reg alternator can be safely used.
---
| - The Matronics AeroElectric-List Email Forum - | | Use the List Feature Navigator to browse the many List utilities available such as the Email Subscriptions page, Archive Search & Download, 7-Day Browse, Chat, FAQ, Photoshare, and much more:
http://www.matronics.com/Navigator?AeroElectric-List |
|
|
|
Back to top |
|
 |
darinh
Joined: 20 Apr 2006 Posts: 327 Location: Utah
|
Posted: Wed Jul 09, 2008 11:47 pm Post subject: Re: Nippondenso alternator question |
|
|
Thanks guys for the input...mine works without the lamp or the lamp circuit altogether.
| - The Matronics AeroElectric-List Email Forum - | | Use the List Feature Navigator to browse the many List utilities available such as the Email Subscriptions page, Archive Search & Download, 7-Day Browse, Chat, FAQ, Photoshare, and much more:
http://www.matronics.com/Navigator?AeroElectric-List |
|
_________________ Darin Hawkes
Series 7
914 Turbo
Kaysville, Utah |
|
Back to top |
|
 |
nuckolls.bob(at)cox.net Guest
|
Posted: Thu Jul 10, 2008 7:55 am Post subject: Nippondenso alternator question |
|
|
At 06:45 PM 7/9/2008 -0700, you wrote:
I agree that its been much discussed in the past however there are many
false and remaining incorrect mis stated comments in the past that simply
do not apply to the most common ND alternator. These false statements
remain in the past unchallenged but still remain not correct with respect
to ND alternators.
Okay. I do appologize. Forgive me for assuming too
much. Please allow me to back up and start anew . . .
Other than MY having tested many ND alternators as well as a couple of
other brands of Internally regulated Japan brand alternators .I question
your accusation that I have made absolute errors (or any errors of any
sort) in my statements.
For example, all the ND alternators I have tested can be turned on and off
while running and producing power. They also can be "B" lead disconnected
under load with no damage to the alternator IF the alternator contacts are
rated properly ( the common often used contactor are not rated to
disconnect the load dump voltages). The addition of the proper contact
voltage and proper power rated transorb is required to protect any low
voltage contactor from arcing and passing the higher load dump voltage back
to the bus.
Do you have schematics that describe the test setup along
with materials callouts and a description of test conditions
that you can share with us for an exemplar test?
The subject alternators have internal transorbs but may overheat under
the long contact bounce of the common contactor, in particular if that
contactor has a diode across the coil which extends the opening or the
contact from around 5ms to as long as 50 ms with, in several cases, major
arcing of dozens of arc pulses. Using the industry recommended transorb
across the contactor coil minimizes the arcing and opening delay but does
not resolve the contact voltage rating which is overstressed and
demonstrated to arc during my testing. Its one of the repeatable tests that
ranged from 2 amps to 40 amps load.
I have tested, documented and published tests results
that illustrate my findings with respect to various
arc suppression methodologies for relays and contactors.
The increased contact drop out delay for the most agressive
arc suppression technique (plain diode) was predictable
and demonstrated in every test. However, contact spreading
velocity seems to be affected more strongly by spring rates
and growing air-gaps between coil core and armature. Only
the slightest slowing of spreading velocity could be
detected between NO suppression and the most agressive
suppression. the delta-t was on the order of 2-4 percent.
From those tests I extrapolated that while the contactor
was certainly slower to begin opening, it was not significantly
slower in spreading once the armature became detached
from the coil core.
I have performed 100's of repeatable tests to support the analysis of the
above statements including the contact arcing under load of the common
contactor.. As well as fast opening and lack of arcing with the Kilovac in
"B" lead testing.
It's an acknowledged fact that the Kilovac devices
are a different cat bred for improved performance
under certain operating conditions. But to avoid
mixing apples and oranges, I will confine the current
discussion to more rudimentary devices like those
suggested in the Z-figures.
Given the numbers of tests cited, I presume that
you have data recorded from those tests that illustrate
your findings? This is where rubber hits the road
my friend. If your findings differ from my own, then
there is some variable between our testing conditions
or philosophy that will explain the differences. As
teachers, we should KNOW what those variables are
so that they become part of our stock and trade in
helping others understand.
(1) So, the first difference to be resolved is why
your findings report significant differences in
arcing between spreading contacts that are dependent
upon style of arc suppression used.
My findings include ND alternators commonly used at the time by NSI, Vans
and others in the mid 1990's have the following features.
1. The IG terminal turns on and off the alternator under load.
Note Its safe as far as the alternator is concerned to turn off the
alternator under load. It must be done with properly rated contactors however.
I'm confused here. Assuming the IG terminal exerts
absolute control over the inner workings of the alternator
then there is no need to utilize an external b-lead
contactor. Alternators and generators in aircraft
and other DC systems have been turned on and off under
ALL conditions of load since day-one by exerting
positive control over the field current.
The schematics of all internally regulated alternators
I've been privileged to review take the IG lead onto
the integrated circuit chip for the regulator. For
the astute practitioner of failure mode effects analysis,
this raises some flags as to the system should be
designed to DEPEND on functionality of the IG lead
as an absolute control. Damage to the chip can
obviously cause loss of regulation (over voltage)
but it could also cause loss of absolute control.
Another variability comes from my interpretation
of your words that suggest the alternator control
philosophy you're citing is not unlike that which
is described in the first schematic of:
http://aeroelectric.com/articles/Adapting_IR_Alternators_to_Aircraft.pdf
Here, I've assumed that EVEN IF the IG lead
does exert absolute control over a normally operating
alternator, it cannot be depended upon to exert
that control under certain failures of the
integrated circuit. Augmentation of that control
is called for in the form of a b-lead disconnect
device of some suitable design.
(2) so another clarification of control philosophies
suggests that EVEN IF the IG lead works as you've
described in all ND alternators you've tested, would
you not agree that the same functionality cannot be
depended upon for other brands? Further, since we
have no way to guarantee our builder friends that
every device marked "ND" functions the same way . . .
ESPECIALLY if overhauled by an after market activity?
2, I have been unable to cause alternator failure even with arcing "B" lead
contactor. Both NSI and Vans at the time was selling rebuilt alternators
and Vans told customers not to use any type of "B" lead crowbar device due
to alternator failure.
Note: This I verified with a personal phone call at the time to Vans. I
have no evidence to suggest your OVP crowbar was the cause but I do suspect
the common contactor was a possible cause due to observed excessive contact
arcing during the extended opening of the contacts due in part to the
simple diode used and the contactor contact V rating.
Interesting hypothesis that argues with my own observations
that generated question (1) above.
3. No ND I tested locked up and could not be turned off at any time safely.
4. No ND required anything connected to the "L" terminal.
Good data points. but in light of potential for variances
that prompted question (2) COMBINED with the desire to
offer a control philosophy that works with ANY brand
of alternator, would you not agree that a 100 ohm resistor
tied between "L" and "IG" is a sure bet even if not
necessary for the particular alternator in-hand?
Clearly its not possible to test all of the hundreds of types of small
shell ND alternators. Further rebuilt alternators may have internal
regulators with difference performance as our application has the
alternator wired differently and the aftermarket rebuilt alternators may
have regulators that only work when installed in an automobile as the
original application.
ABSOLUTELY! This is the exact thinking that drives my
system design suggestions. The goal is NOT to have my
readers worrying over all the possibilities for his/her
particular alternator in-hand but to offer the simplest,
most universal solution that is free of such worries.
5. Its safe to open the "B" lead under load if the contactor is rated for
at least 200V contact rating. Only the KIlovac and similar HV contactors
have proper voltage ratings. The common contractors for 12V system battery
and starter etc have contacts only rated for under 50V max during the
opening process. They can tolerate higher voltage across the contacts when
the contacts are open. They will arc during the opening of an alternator
load and the result may cause damage to both the alternator and aircraft bus.
Okay, here's where we need to talk about system conditions
at time of opening. IF the alternator is being shut down with
all equipment operating normally (alternator output is under
control of a functioning regulator) then upward excursions
of b-lead voltage is limited by the over-shoot response of
the alternator/regulator combination if the alternator is
under load at time of disconnect.
(3) The next question goes to the magnitude, duration and
energy contained in the transient event of a suddenly
unloaded alternator. The magnitude of these numbers are
CRITICAL to understanding the energy that either needs to
be stood off (by sizing of clamping devices like transorbs)
or withstood (by sizing circuit breaking capabilities of
the b-lead contactor). With the testing you've accomplished,
have you quantified this event and can you share that data?
Do not use a common diode across a common contactor coil and do not use a
common 45V contactor contact rating as either or both actions greatly
increase of alternator damage.
(4) This raises some flags. Exactly how does the arcing
across the spreading contacts of the b-lead disconnect
device stress the alternator? The arc is a sustained (if
not smoothly varying) current that is no greater than
the alternator is rated to deliver. I think we can agree
that the voltage available is no greater than the magnitude
of over-shoot transients which I presume you've sized and
can describe in question (3).
Perhaps you can substantiate your statements with some of your testing of
the commonly used ND alternator. Please provide the Lester number so we all
can verify your test results..
As I mentioned in earlier posts, I try to craft design
philosophies that are NOT constrained by selection of
specific parts. My design goals are (A) craft the simplest,
lowest cost of ownership, failure tolerant system. (B)
deduce ways in which the widest selection of components
can be utilized IRRESPECTIVE of their internal operating
differences.
For me, this discussion has never been about the deifying
the ND products or vilifying any other product. It's been
about deducing ways that my readers can use any alternator
they choose. When this goal is achieved, the greatest
concern for selection is that the thing might be a piece
of junk . . . but it doesn't matter because we've designed
a system that if failure tolerant. I.e., ALL failures are
a maintenance expense, not a safety issue.
My reply to the questioner was intended to be general as he did not state
the exact ND Lester number and was it rebuilt or new. With out knowing that
there is no absolute recommendation on how to wire it up.
. . . and I'll suggest that my response for the resistor
was a universally applicable approach that didn't care
about make, model, or functionality of the alternator.
Yes there are alternators of different brands (and perhaps some ND do also,
but not the common ones that I have tested.) that lock up and others that
require a lamp in the wiring to start. perhaps there are also other that
cannot survive a load dump but none in the industry will state that their
regulators lack the universal load dump internal protection (except that
load dumps resulting form extended arcing from contacts or broken wiring
are not protected as overheating or the protection Transorb is possible.
(5) This gives rise to the next question that goes to
the un-quantified "extended arcing". Folks in industry
a fond of talking about such things without numbers that
allow a system integrator to artfully integrate their
products into a consumers system. You have repeated the
phraseology without quantification. It's my goal that
my partner in Douglas-Nuckolls LLC will help me get this
critter . . .
http://aeroelectric.com/Pictures/Alternator_Test_Stand/Alternator_Test_Stand_1.jpg
up and running so that I can expand my personal knowledge
of these questions that have been CRITICAL details of alternator
discussions on this List for 10 years. To date they've
NEVER answered by anyone. If you have access to this
kind of equipment and test articles right now, then
I'll suggest you are in the very best position to advance
the state of our art and the quality of our discussions
to the benefit of anyone interested in reading them.
Your cheep un-substantiated comment that I have made absolute errors does
not suit your normally nice style. Lets keep the discussion technical and
not call me a person making false statements please.
Agreed. I let my frustrations with another matter
bleed over into my work on this List. Explainable
but not excusable. I beg your indulgence.
No respectable person can let that cheep shot pass. If I made a error
please prove it.
How many stock ND alternators used in aircraft have you tested????
My concerns come from the notion that every device
having the ND logo on it is "stock" or "golden"
. . . especially when we know NOTHING about the pedigree
of the alternator in question and even less about how
the regulators are crafted.
Perhaps I missed it in the past and if so I apologize if you show me the
statement. It has been more than 10 years ago when many of my testing was
done and perhaps My memory has failed. To me the discussion on this years
ago was long settled with you on one side and Jet Pilot George (for one) on
the other side.
Describe "sides" . . . my antagonists basically
offered the notion that everything ND was golden
substantiated by nothing more that marketing hype.
I have personally tested NO internally regulated
alternators. ALL of my work with aircraft alternators
and generators has been done on the legacy products
that prevail in type-certificated aircraft. I'm moving
toward the capability to test such devices as noted
above because the data I need for artful design is
has not been forthcoming from other sources. Perhaps
you can assist.
(6) There is one more case for alternator control
that involves understanding how to handle the
fully-excited runaway condition with an external
b-lead contactor . . . but this is a special case
that begs a separate discussion. For now, if you
could share what you know that goes totward (1)
through (5) I'd be more pleased than you can know.
As side comment many regulators have a OVP built in that limits the output
voltage to around 16V.
That claim has been made before . . . and in one discussion,
a reader suggested that when a pilot experienced an
ov condition (that puffed up his battery and zorked a
number of ship's accessories) that the ov condtion
had to have been limited to something on the order
of 16 volts. I presume this statement came from an
interpretation of marketing hype for a particular
product . . . with no guarantees that the failed device
in the guys's airplane had the same feature.
I've often cited the dearth of real data on internally
regulated alternators. This device has been cited
many times in discussions here on the List.
http://aeroelectric.com/Mfgr_Data/Semiconductors/MC33092A.pdf
This is the ONLY hard copy of an internal regulator
design I've been privileged to study. If you trace through
the functionality of this device, you'll discover that
there is OV warning, but no OV protection. Is this
20+ year old device a good example of what's available
today? Who knows? If anyone does know, it has not been
shared here on the List.
Given the lack of information, I have to proceed with
worst case assumptions that treat the built in regulators
with no more reverence than external regulators
of yesteryear . . . hence failure tolerant no matter
what.
If we DID have detailed data on ANY brand and part number
of alternator/regulator . . . it would be of little value
to me as purveyor of universally applicable advice. It's
not my goal to help Joe rivet-bucker integrate a particular
part into his system . . . the goal is to offer ways he
can integrate any part with some reasonable sense of confidence
in failure tolerant design.
This will not protect against all failures thus an external OVP is
required. I have experienced 2 regulator failures (over the past 50 years
in autos where the output jumped from 14+ to 16V and held the output there.
One was the common external regulatro YOU long have recommended as a low
cost "ford" style.
The "ford" style has never been a consistently performing
product. The first pass at this design was this
critter . . .
http://aeroelectric.com/Pictures/Regulators/Ford_EM_Reg.jpg
Pure electro-mechanical. No OV protection. I designed the
first OV protection module . . .
http://aeroelectric.com/Pictures/Schematics/Cessna_OVModule.gif
that was applied to this regulator at Cessna many moons
ago.
Over the years, the EM regulators were replaced with
solid state devices from a number of suppliers including
Ford and typical of this package . . .
http://aeroelectric.com/Pictures/Regulators/Ford_SS_Reg.jpg
http://aeroelectric.com/Pictures/Regulators/Ford_SS_Reg_open.jpg
At this point, features and functionality from model to
model begins to diverge. I've seen them offered with
over current and over voltage protection built in . . .
but with no definitive descriptions of how those features
worked. I.e., no way that the prudent aircraft systems
designer can accomplish FMEA and deduce suitability to
the task. Therefore, in satisfaction of my goal for
universally applicable advice, I assume that ALL such
devices are applicable to my designs if augmented with
OV protection of predicable functionality illustrated in
the Z-figurs.
Please do not reply and waste bandwidth and all of our time unless you have
specific test data to prove your response. Past history posts that do not
include backed up with actual testing ase just opinion and not worth
considering.
I will request the same courtesy from you and I've
cited the items of divergence/confusion above. I have
provided detail process and numerical data on every
experiment I've conducted. It's my intent to gather
the data we all need, everyone talks about but nobody
possesses or has shared if they do possess it. Toward
this goal, no amount of bandwidth is wasted.
Paul
PS: I do not want to start another often widening discussion. Perhaps I
should have remained silent but you stated you were out of town and I have
had a lot of experience including some from other groups (who in error)
make general statements that ND alternators require a light across the IG
and L connections. Further I have had the impression you have yet to test
any internal ND or any other brand alternator. This was to be done after
you had the test stand up and running.
The discussion will be no wider than necessary to
achieve an understanding of how internally regulated
alternators function to the degree that we can craft
the most universal techniques for using them.
I have witnessed and peer reviewed test setup and test results to support
the above statements. Only the conclusions have ever been document as I
felt at the time there was no reason to do more than I did. I simply am not
interested in trying to prove anything to anything just pass on real test
results that proved how the auto internal reg alternator can be safely used.
We can TALK about tests until you-know-where freezes
over but none of this talk has universal value until
the simple-ideas of the physics and magnitude of effects
are documented and shared. Critics of movies and restaurants
can wax eloquently about their favorite topics . . . and
some individuals find value in reading their words. You
and I are on the other side of the stove where understanding
exactly what and why ingredients go into a recipe for success
is critical to understanding.
Kindest regards,
Bob . . .
| - The Matronics AeroElectric-List Email Forum - | | Use the List Feature Navigator to browse the many List utilities available such as the Email Subscriptions page, Archive Search & Download, 7-Day Browse, Chat, FAQ, Photoshare, and much more:
http://www.matronics.com/Navigator?AeroElectric-List |
|
|
|
Back to top |
|
 |
info(at)mtfind.com Guest
|
Posted: Thu Jul 10, 2008 9:31 am Post subject: Nippondenso alternator question |
|
|
[quote] THANK YOU for your very nice reply!!
Please bare with me as the data I have is long many years filed away
and will be hard to resurrect a lot of it other than my conclusions.
The results were so clear to myself and several other local peers as well
as Eric (on the east coast) I simply pressed on. I had no intent to come
up with a universal solution when the specific ND type was discovered to
meet what my group felt was a reasonable recommendation. Low cost, small
and light weight, readily available, and 50-55 amp output which fit most
applications including LYC and most popular auto engine conversions.
I will try to provide information to discuss one part at a time as this
email includes a large range of subjects and can end up being 1,000 lines
long and too long for others to follow. Thus it may take as many as 8-10
different subject strings to cover each subject area
I have specific experience (including test stand load tests up to 40 amps
load) with several types of ND alternators which are different in several
respects. Its clear to me that blessing all ND alternators as suitable is
not true. I also have some experience with two brands of alternators.
These were as I recall MI and HI brands??. I need to look up details as
they had undesirable design features (at least to me) like requiring a
lamp and or locking up. Also the reported failure rate in autos was of
concern. I do not agree that the objective of one solution fits all
brands/types is a reasonable solution but good luck. With my research 99%
of internal reg alternators are ND and of the hundreds of types of ND
available only a couple types are used in any quantity. Thus I settled on
one brand ND and one type for general use. Today there is a second ND Type
that is slightly larger and heavier that is 80-90 amp output that might be
a better choice for the more complex OBAM being today.
In any event its now my turn to start one subject at a time in replying to
your comments and questions.
Paul
---
| - The Matronics AeroElectric-List Email Forum - | | Use the List Feature Navigator to browse the many List utilities available such as the Email Subscriptions page, Archive Search & Download, 7-Day Browse, Chat, FAQ, Photoshare, and much more:
http://www.matronics.com/Navigator?AeroElectric-List |
|
|
|
Back to top |
|
 |
sportav8r(at)gmail.com Guest
|
Posted: Thu Jul 10, 2008 10:03 am Post subject: Nippondenso alternator question |
|
|
Now THIS I'm looking forward to, not with blood-lust, but just the anticipation that we are going to _get somewhere_ as an OBAM community on this lightweight IR alternator issue, with confidence and without too much frustration. Many others, I suspect, are like me - not wanting to do the lab research but certainly to understand the research of others, and waiting patiently for a turn-key solution that works for our planes with a minimum of fuss and procurement headaches.
Play nice, gentlemen. The students are watching
-Bill B
On Thu, Jul 10, 2008 at 1:28 PM, Paul <info(at)mtfind.com (info(at)mtfind.com)> wrote:
[quote] --> AeroElectric-List message posted by: "Paul" <info(at)mtfind.com (info(at)mtfind.com)>
[quote] THANK YOU for your very nice reply!!
Please bare with me as the data I have is long many years filed away and will be hard to resurrect a lot of it other than my conclusions.
The results were so clear to myself and several other local peers as well as Eric (on the east coast) I simply pressed on. I had no intent to come up with a universal solution when the specific ND type was discovered to meet what my group felt was a reasonable recommendation. Low cost, small and light weight, readily available, and 50-55 amp output which fit most applications including LYC and most popular auto engine conversions.
I will try to provide information to discuss one part at a time as this email includes a large range of subjects and can end up being 1,000 lines long and too long for others to follow. Thus it may take as many as 8-10 different subject strings to cover each subject area
I have specific experience (including test stand load tests up to 40 amps load) with several types of ND alternators which are different in several respects. Its clear to me that blessing all ND alternators as suitable is not true. I also have some experience with two brands of alternators. These were as I recall MI and HI brands??. I need to look up details as they had undesirable design features (at least to me) like requiring a lamp and or locking up. Also the reported failure rate in autos was of concern. I do not agree that the objective of one solution fits all brands/types is a reasonable solution but good luck. With my research 99% of internal reg alternators are ND and of the hundreds of types of ND available only a couple types are used in any quantity. Thus I settled on one brand ND and one type for general use. Today there is a second ND Type that is slightly larger and heavier that is 80-90 amp output that might be a better choice for the more complex OBAM being today.
In any event its now my turn to start one subject at a time in replying to your comments and questions.
Paul
---
| - The Matronics AeroElectric-List Email Forum - | | Use the List Feature Navigator to browse the many List utilities available such as the Email Subscriptions page, Archive Search & Download, 7-Day Browse, Chat, FAQ, Photoshare, and much more:
http://www.matronics.com/Navigator?AeroElectric-List |
|
|
|
Back to top |
|
 |
nuckolls.bob(at)cox.net Guest
|
Posted: Thu Jul 10, 2008 12:39 pm Post subject: Nippondenso alternator question |
|
|
At 10:28 AM 7/10/2008 -0700, you wrote:
Quote: |
>THANK YOU for your very nice reply!!
>
>Please bare with me as the data I have is long many years filed away
>and will be hard to resurrect a lot of it other than my conclusions.
>
>The results were so clear to myself and several other local peers as well
>as Eric (on the east coast) I simply pressed on. I had no intent to come
>up with a universal solution when the specific ND type was discovered to
>meet what my group felt was a reasonable recommendation. Low cost, small
>and light weight, readily available, and 50-55 amp output which fit most
>applications including LYC and most popular auto engine conversions.
|
Understand . . . and from the perspective of
needing to design a product, one needs to
be much more specific as to the numbers that
appear on a bill of materials . . .
Quote: | >I will try to provide information to discuss one part at a time as this
>email includes a large range of subjects and can end up being 1,000 lines
>long and too long for others to follow. Thus it may take as many as 8-10
>different subject strings to cover each subject area
>
>I have specific experience (including test stand load tests up to 40 amps
>load) with several types of ND alternators which are different in several
>respects. Its clear to me that blessing all ND alternators as suitable is
>not true. I also have some experience with two brands of alternators.
>These were as I recall MI and HI brands??. I need to look up details as
>they had undesirable design features (at least to me) like requiring a
>lamp and or locking up. Also the reported failure rate in autos was of
>concern. I do not agree that the objective of one solution fits all
>brands/types is a reasonable solution but good luck.
|
Not so much a dependence on good luck but a degree
of protection from bad luck. Too many of the dark-n-stormy-night
stories on electrical system issues demonstrate a gross lack
of understanding on the part of pilots and an unimpressive
demonstration of design goals on the part of TC aircraft
manufacturers for failure tolerant design. But given that aircraft
and medicine are probably the two most regulated industries
in our nation, we need only look to those to craft law to
understand why these industries are ham-strung.
Given the millions of alternators and many dozens of brands/styles
on the road that provide good service, it's not unreasonable to
suggest that an OBAM aircraft owner has a huge pallet of colors
from which to paint their electrical system. Risk for a bad choice?
Sure . . . but relatively low. Especially If we can prevent a bad
choice from becoming a safety issue.
Now, if any individual has a product performance report to share
with other builders that suggests a good value, that's fine with
me but outside my mission. I don't work in a venue where I can
recommend choices among alternators, switches, engines, tires,
instruments, upholstery materials, etc. But I CAN craft architectures
that minimize cost of ownership, weight, parts count and RISK.
Quote: | > With my research 99% of internal reg alternators are ND and of the
> hundreds of types of ND available only a couple types are used in any
> quantity. Thus I settled on one brand ND and one type for general use.
> Today there is a second ND Type that is slightly larger and heavier that
> is 80-90 amp output that might be a better choice for the more complex
> OBAM being today.
|
An your selection for your application is probably the
ideal fit to your design goals. For customers to are
willing to pay my outrageous fees, I'm equally specific.
But for the folks who hang out on this List, I don't
want to close any doors and windows for parts selection
except where there is perceived increases in risk.
Quote: | >In any event its now my turn to start one subject at a time in replying
>to your comments and questions.
|
Looking forward to a productive exchange of ideas!
Bob . . .
| - The Matronics AeroElectric-List Email Forum - | | Use the List Feature Navigator to browse the many List utilities available such as the Email Subscriptions page, Archive Search & Download, 7-Day Browse, Chat, FAQ, Photoshare, and much more:
http://www.matronics.com/Navigator?AeroElectric-List |
|
|
|
Back to top |
|
 |
rampil
Joined: 04 May 2007 Posts: 870
|
Posted: Thu Jul 10, 2008 2:48 pm Post subject: Re: Nippondenso alternator question |
|
|
Gee,
Has anyone thought to go to http://www.globaldensoproducts.com/em/a/
Root around and get actual information about their specific model
alternator from their library?
I got the info I needed on the specs of my aux ND alternator derived
from the 3 cyl Geo Metro.
| - The Matronics AeroElectric-List Email Forum - | | Use the List Feature Navigator to browse the many List utilities available such as the Email Subscriptions page, Archive Search & Download, 7-Day Browse, Chat, FAQ, Photoshare, and much more:
http://www.matronics.com/Navigator?AeroElectric-List |
|
_________________ Ira N224XS |
|
Back to top |
|
 |
Bill Schlatterer
Joined: 09 Jan 2006 Posts: 195
|
|
Back to top |
|
 |
info(at)mtfind.com Guest
|
Posted: Thu Jul 10, 2008 8:11 pm Post subject: Nippondenso alternator question |
|
|
---
| - The Matronics AeroElectric-List Email Forum - | | Use the List Feature Navigator to browse the many List utilities available such as the Email Subscriptions page, Archive Search & Download, 7-Day Browse, Chat, FAQ, Photoshare, and much more:
http://www.matronics.com/Navigator?AeroElectric-List |
|
|
|
Back to top |
|
 |
nuckolls.bob(at)cox.net Guest
|
Posted: Sat Jul 12, 2008 4:57 pm Post subject: Nippondenso alternator question |
|
|
At 10:28 AM 7/10/2008 -0700, you wrote:
Quote: |
>THANK YOU for your very nice reply!!
>
|
<snip>
Quote: | >In any event its now my turn to start one subject at a time in replying
>to your comments and questions.
|
Paul, how about we avoid turning this into an unnecessary and/or
unproductive research/science project . . . It would be useful to
craft a sort of mission statement where goals, impediments to
goals, questions and plans for acquiring data that go to aswering
those questions are identified up front. To that effort I'll offer
the following:
1) Since day-one, electrical systems in aircraft have offered
a means by which engine driven power sources may be turned on
and off at will of the pilot. This absolute ON/OFF control goes
to a number of issues that include but are not limited to
preflight testing, load management, ability to take a mis-behaving
system off line, and plan-B activities crafted to mitigate
effects of failure. I.e., failure tolerance.
2) The modern automotive alternator has a proven track record
in ground based vehicles that eclipses anything flying
by an order of 1000:1 or more. It's inarguable that sources
of automotive components from salvage yards up through the
chain to manufacturers of modern components offer the OBAM
aircraft community a treasure-trove of choices.
3) The shear magnitude of choices can be a boon in terms
of potential return on investment for performance and
reliability . . . and a bane in terms of the complexity
for choosing "suitable" hardware from an overwhelming
universe of products and sources.
4) As knowledgeable and experienced practitioners of the
art and sciences we can relieve OBAM aircraft owner/operator
concern for making choices while minimizing risk for having made
a "bad" choice? I'll have to qualify "bad" . . . EVERY
piece of hardware we choose to bolt to an airplane will fail
at some point in time irrespective of its source or perceived
quality. Failure can be due to quality issues . . . operation
outside design limits . . . or the thing simply wears out.
5) My personal preference for minimizing risk is to craft
failure tolerant architectures . . . if we do
that job well, then it doesn't matter if the platinum
plated part fails because some kid didn't tighten a
bolt (quality issue). . . or failed because the part is
one step above junk (design or manufacturing issue).
Failure tolerance is the most powerful tool for risk
management we can bring to the table.
6) You appear to be crafting a risk mitigation
approach along with relief of the decision making process
in the form of specific architectures crafted from
specific part numbers. You believe this approach
is attractive to potential customers. This is the
essence of entrepreneurial opportunity in what is
still (unlike TC aviation) a relatively free marketplace.
Your approach borrows from the legacies of TC aviation
by specifying a design and more controlled suite of
components. No doubt here are/will-be customers
attracted to this approach and I'm sure we all wish
you well in your endeavor. My entrepreneurial leanings
go to system integration hardware, products that help
the OBAM aircraft builder comfortably integrate a host
of choices into the airplane. But first, I need to achieve
an understanding of the simple-ideas that go into
our respective inventions . . . ingredients that drive
recipes for success.
7) We have a common need to exercise a solid grasp
of the same simple-ideas even if our respective inventions
have no competitive features. The most pressing question
for me is understanding the load-dump characteristics
of our favorite alternators under conditions likely to
be encountered in a typical installation on a Lycoming -
spinning like a whirling dervish and subject to
unloading under any condition between zero and full
output with normal regulation. This means knowing the magnitude,
source impedance and timing of the transient that occurs
after sudden load removal at all corners of the
operating envelope.
The very first experiment I plan to conduct after
the alternator drive stand is running is based on
the sketch at:
On a 60A machine with battery disconnected,
I'd get data plots of load dumps at 4, 6, 8, 10
and 12KRPM for fixed load of 50A with a 10A dump,
fixed load of 40A with 10A and 20A dumps, fixed
of 30A and 10, 20 30A dumps . . . I think you'll see
the pattern here.
The goal would be to calculate/measure the peak
voltage, total energy and duration of each overshoot
event (or series of overshoots assuming the regulator
control loop is poorly damped). I would probably
set up to run external regulators (of the type
normally installed inside) so that I could explore
the differences between various regulators while
holding the alternator constant.
Obviously a big task to gather enough data to
be reasonably sure we understand the majority of
the fleet . . . assuming we discover wide variances.
(9) The next tests would involve system behavior under
runaway conditions. Artificially fail a regulator
and plot dv/dt at the bus and di/dt at the battery
with various fixed loads . . . one suite of plots
with a fresh battery, another with a battery that
has fallen to 1/2 capacity or less.
Having this data on only one combination of
alternator/regulator would set the order of magnitude
for energies involved. Once the equipment for the
testing is in place and the procedure tuned, it would
probably take less than a half hour to test any other
combination.
I ran all these tests that supported products I designed
for Beech and others many moons ago. But the only
data acquisition we had then were storage 'scopes and
chart recorders. You could "eyeball" the data for gross
suitability to task but real energy studies were exceedingly
difficult . . . they were never done. We can do a much
better job today.
The task is to characterize the dynamic response to
load change for a normally functioning as well as
a runaway alternator. The data collected would allow
a designer to craft systems that deal quietly and
capably with the voltages, currents and energies that
are present during recovery from both a load-dump
and hard-failure conditions.
This was the kind of data I was hoping to gather
some years back when there was discussion about
you and Eric teaming on some sort of activity. I
wasn't sure exactly what equipment you were going to
have access to . . . or what testing satisfied
curiosities for your project . . . but I had hopes
of piggy-backing studies above if you didn't already
have similar data.
Do I presume that for your needs, no further
investigation is necessary/useful to your task?
Know that all of my own test results will be published
on aeroelectric.com and that my equipment will be available
to you (or anyone else in the OBAM aviation community)
should new questions arise.
I'm going to have Zach start stripping out the automotive
test setup wiring from the test stand next week. We'll
leave only the 3-phase motor drive wiring intact. We'll
Z-12 and Z-13/8 architectures in the stand. I already
have a small drive stand for second alternators up to 20A.
I have a static phase converter to install in the
big stand. We'll see we can get the motor and variable
speed drives to run. That will be a BIG step. Not sure
if we'll be able to do real testing before we have to
pack up and move to M.L. I have a contractor running
a fat 240 feeder to the shop at the same time we excavate
for a new retaining wall at the back of the yard. So the
heavy/dirty/ugly work should be behind us at both
locations this summer.
Bob . . .
| - The Matronics AeroElectric-List Email Forum - | | Use the List Feature Navigator to browse the many List utilities available such as the Email Subscriptions page, Archive Search & Download, 7-Day Browse, Chat, FAQ, Photoshare, and much more:
http://www.matronics.com/Navigator?AeroElectric-List |
|
|
|
Back to top |
|
 |
info(at)mtfind.com Guest
|
Posted: Sat Jul 12, 2008 10:02 pm Post subject: Nippondenso alternator question |
|
|
Well (very sadly but it did seem too good to be true and I am not surprised)
I had hoped for mutual cooperation but I guess you want to do it all your
self. Good timing as I was just finishing the first part of the planned
discussion.
Be my guest, I had thought you had changed. Clearly you want yo frive the
discussion VS get the benefit of my extensive work.
Random comments as its not worth my time to put them in ordered sequence. I
have made some suggestions about how and what to test to avoid missing
information that is not gathered just using your sketched circuit.
You are incorrect about my approach and intent and about my past analysis
and testing which is in my opinion adequate to determine the problem and I
have "crafted" a proven solution. In my opinion there is ZERO need for more
testing other for self aggrandizement. I find this sad as you have not seen
any real results of my testing nor the scope of it. Reading your suggested
approach I find little to agree with so there is no point in my being a part
of your long promised study.
Further most of your below comments about my position are totally incorrect
assumptions which is not surprising as you have never spent the time to find
out what my approach is; the amount of analysis, investigation nor testing
setup and results. I will not tolerate testing as anything other as proof of
pre testing design analysis. I also simply will not design using assumptions
or unofficial verbal assurances from one manufacturer its safe to exceed the
specifications as that is simply a high risk approach no engineer will do.
My results are identical design solution for all reasonable alternator but
clearly its not reasonable to allow any alternator to be covered and that
position indicates to me a lack of modern alternator designs etc. Further
you seem fixated on maintaining several design flexibilities and pilot
control that I feel is not only not required but potentially dangerous.
Also your sketch does not reproduce the real world load dump conditions what
with fixed load and relay contact bounce in the real circuit. Finally it
appears you intend to have a constant string of load dumps which is very
likely to destroy the internal to the regulator load dump protection
components. Each single load dump needs time for the protection circuits to
cool down.
Hopefully you will end up with far more evaluation, studying, and testing
than what you listed below as its not adequate nor has it addressed ALL the
problems I have addressed. You really should test all the brands of
alternators you intend to approve of and in the several different types and
amps in each style. There are differences to consider. For example different
regulator transient response as well as the winding charactericts which will
determine the load dump information.
Further you should take note of the fact just how much (or more important,
how little) is replaced in rebuilt alternators as if you know what is
replaced you would never recommend a rebuilt alternator (rebuilt is a
misnomer minimal repair is what actually happens).Junk yard is not a source
for ANY aircraft as who knows how close to failure the parts are. In any
event testing alone, with out first doing an analysis and manufacturers
detailed data is NEVER sufficient. Both Myself and Jet Pilot found getting
more detailed information was not easy and getting past the sales staff if
difficult at best. However a lot of useful information was passed on and
po-poed on this groups list.
Also be sure to test with a full load current and zero fixed load. Note my
selected 50 amp rated alternator is specified to put out 70 amps at 13V and
more amps at lower voltages so a full output failure results in a much
higher current than your suggested testing which based on my testing is not
nearly worst case! Another comment about getting the real data first. My NEW
alternator came with a computer printout of the actual alternator during
final test prior to shipment. Note the full amp output is a lot higher than
past comments have been clearly assumed on this list in the past. 40% higher
is not small in my opinion and under load dump conditions the load being
dumped is much higher energy as well as the peak voltage. My testing was
based on a real duplication of a typical aircraft wiring including wire
gauge and lengths as well as flight batteries. It started with your OVP and
contactor with the diode on the contactor coil. Very different than what
your sketch shows. Also very long alternator failure point to final
contactor opening requiring voltage clamping during that time of a lot more
energy than what has been assumed in one of your tests from years ago.
But then we have a large and fundamental difference on how to design any
electrical (including aircraft) systems. My approach is to discard many of
the proven pilot opportunities to mess up that have been a reason for past
crashes and leap into the 21st century. Building on the past and not address
the fundamental cause of most accidents is not progress in my opinion. The
more pilot required actions greatly increases the pilots lack or incorrect
action. Today there is no need to do things manually in most cases. Every
manual control available to the pilot 's another opportunity to make a
mistake that can lead to a crash. Today we have Integrated Solid state
switches/circuit breakers. Schottly diodes are not really needed much less
silicon bridges which have no use in aircraft. Yes Solid state switching is
easy to make with full bi-directional isolation and ON resistance less that
of mechanical relays etc switching (as low as 0.002 ohms ON resistance). The
pilot needs to be notified of any CB failure not by finding out by failure
of the component to work for example.
The aircraft instruments have migrated from steam gauges to flat panels yet
we still find the old contactor relay// switch approach of 1950 etc and that
ignores the modern components available today that are far more reliable and
more pilot friendly.
Its a fact that pilot error is the major cause of accidents. Its pilot error
if you run out of fuel, deplete the battery based on an assumption of
battery condition and electrical load etc etc. The requirement to throw a
switch in an emergency is bad design if there is a reasonable solution that
eliminates the mechanical pilot action and its done automatically. Its sad
that there is no truly modern system available at a reasonable price on the
market today that automates the system and provides the pilot with useful
real time electrical system conditions. My designs have been peer reviewed
by my (multiple) peers and all have stated its both more reliable and a
great improvement to current 1950's parts and today's arrangements and
approaches. You have long promoted fly the airplane and trouble shoot back
on the ground which is not what your design requirement to turn on and off
the alternator in flight and a simple voltage check is enough for preflight.
Personal situation has delayed getting my system on the market.
The E bus is a good example where there is a design requirement to have a
group of avionics disabled during part of the flight and then guess about
how much battery life is left. A simple additional electrical instrument I
have designed allows the pilot to simply see the real flight time left and
change the load and have the flight time left update. It also determines the
true battery life dynamically. If I am IFR I may need a different set of
avionics than what is on the E bus for example depending on the actual
flight conditions. Or what if the battery power left at any point is less
that what was predicted or measured months ago?. I know of several off
field crashes due to the battery being depleted well before the expected
time. Another bad design to assume something in particular when it ns not
required to assume. Fuel tank gauges system when the only accurate
requirement is full and empty has been replaced with fuel flow measurement
and totalized as seen in modern automobiles. No reason the battery cannot be
treated the same way, sure its a little more complex but not hard to do with
reasonable accuracy.
There are many ways to make flying safer than having a check list of which
switches to throw under different failure modes and make assumptions of
flight time left for example. How about a warning and a count down display
that tells the time left to fly and updates as the pilot changes the
equipment powered on. No action is required if the time remaining is long
enough.
Your insistence of performing your own testing is fine but you are
discarding months of investigation as well as hundreds of hours of testing
and analysis. On the other hand it will save me a lot of time producing a
machine readable copy etc.
A lot of people blindly used your OVP crowbar until it was used with Vans
aircraft and had many reported failures. As far as I know there was never
and failure analysis to prove the true reason for the failures. My own
testing found fault at least two faults with the OVP design but they only
caused false tripping and the real reason appeared to be the use of the
contactor and perhaps rebuilt alternators with possible second rate (read
lower cost) regulators that could not stand up to the resulting load dump
voltage peaks. In any event the OVP design was not properly desinged in the
first place likely due to the test first and skip the analysis under
transient conditions.
It is true I had intended to produce an engineering document VS a
technicians experimental results
I have far too much to do, so its easy to simply bow out. Further I will not
comment on your results as I have better things to do. There is no need to
try to discuss your approach as your mind is seemingly always made up ahead
of time.
You win and I think the group looses. Jet Pilot tried with a lot of real
research and was not listened to either.
We have very very different backgrounds and approaches to design. I had
hoped we could work together but that is not to be. I simply do not have the
time, nor can I stand the frustration of writing one paragraph and getting a
response of several pages of comments which are mostly, to me, not to the
point.
Best wishes
Paul
---
| - The Matronics AeroElectric-List Email Forum - | | Use the List Feature Navigator to browse the many List utilities available such as the Email Subscriptions page, Archive Search & Download, 7-Day Browse, Chat, FAQ, Photoshare, and much more:
http://www.matronics.com/Navigator?AeroElectric-List |
|
|
|
Back to top |
|
 |
nuckolls.bob(at)cox.net Guest
|
Posted: Sun Jul 13, 2008 8:50 am Post subject: Nippondenso alternator question |
|
|
To: aeroelectric-list(at)matronics.com
Subject: Re: Nippondenso alternator question
At 10:59 PM 7/12/2008 -0700, you wrote:
Well (very sadly but it did seem too good to be true and I am not surprised)
I had hoped for mutual cooperation but I guess you want to do it all your
self. Good timing as I was just finishing the first part of the planned
discussion.
WHOA! There was no intent on my part to exert any
form of control over how you responded to this
new initiative. If you have information to share
on any topic and in any form, I'm sure it will
be welcomed by many including myself . . .
Be my guest, I had thought you had changed. Clearly you want to frive the
discussion VS get the benefit of my extensive work.
Absolutely! However, I just finish an archiological dig
through records and drives looking for work I did on a
project at Beech some years back. The $time$ expended looking
COULD have been well spent looking . . . but in this case,
BETTER spent repeating the work which I am going to have
to do anyway. I was only attempting to perhaps relieve you
of some efforts trying to resurrect past work.
Random comments as its not worth my time to put them in ordered sequence. I
have made some suggestions about how and what to test to avoid missing
information that is not gathered just using your sketched circuit.
You are incorrect about my approach and intent and about my past analysis
and testing which is in my opinion adequate to determine the problem and I
have "crafted" a proven solution. In my opinion there is ZERO need for more
testing other for self aggrandizement.
Wrong. The repeatable experiment is the CORE of good science.
No how much testing your or I do, there is always risk of
error, variability in process or materials, and variability
in interpretation of results. Finally, there are individuals
in our society that will stand up, point a finger and accuse
the tester of having some hidden agenda. There is no stronger
validation of anyone's work than to say, "Here's what I did,
here's what happened, here's the significance of the data.
Oh, by the way, Mr. X in Arizona and Ms. Y in Georgia did
similar if not identical work and our respective conclusions
support each other." Besides, I need that equipment and test
set-up for other activities.
I find this sad as you have not seen
any real results of my testing nor the scope of it. Reading your suggested
approach I find little to agree with so there is no point in my being a part
of your long promised study.
Paul . . . I don't know what I can write that
encourages you not to respond to what I do in the
worst possible light. You have not published one
White Paper, not one schematic, not one explanation
of features that helps me or anyone else understand
diddly-squat about what you're proposing.
Further most of your below comments about my position are totally incorrect
assumptions which is not surprising as you have never spent the time to find
out what my approach is; the amount of analysis, investigation nor testing
setup and results.
But Paul, you have not shared even the smallest part of what
you've accomplished. I've reviewed our past exchanges and
the majority of your efforts were directed at tearing down
what I had been doing successfully for decades. The only
data you cited came from manufacturer's data sheets.
I will not tolerate testing as anything other as proof of
pre testing design analysis. I also simply will not design using assumptions
or unofficial verbal assurances from one manufacturer its safe to exceed the
specifications as that is simply a high risk approach no engineer will do.
If you're talking about crow-barring breakers, exactly WHAT
limit was being violated? I cited the Mil Std under which all
those breakers were certified that requires they function as
advertised when subjected to fault currents of over 1000 amps.
Many times the values cited in guaranteed performance curves. Curves you
chose to interpret as limits.
My results are identical design solution for all reasonable alternator but
clearly its not reasonable to allow any alternator to be covered and that
position indicates to me a lack of modern alternator designs etc. Further
you seem fixated on maintaining several design flexiblities and pilot
control that I feel is not only not required but potentially dangerous.
??? Now I'm really lost. Are you suggesting that alternators
can and should be used for aircraft in the manner we've accepted
for cars? No control whatsoever, no ov protection, no ability
to manage loads and power generation in multiple alternator
systems? Is it your suggestion that the design and operation
protocols common to 99.999% of all aircraft flying can be
summarily dispensed with?
Also your sketch does not reproduce the real world load dump conditions what
with fixed load and relay contact bounce in the real circuit.
The sketch depicts only the energy sources and sinks and the
organization needed to explore the characteristics of an alternator.
No more. Exploration of contactor performance in the task of
energy control is a separate experiment.
Finally it
appears you intend to have a constant string of load dumps which is very
likely to destroy the internal to the regulator load dump protection
components. Each single load dump needs time for the protection circuits to
cool down.
The "string" for T(off) can be ANYTHING out to infinity. This is a general
arrangement I used 30 years ago to fine tune the dynamics of
voltage regulator designs. Obviously, getting the energy signature
from a particular combination of L(fixed)+L(switched) can be done
with very few events. The schematic was intended to describe setup,
not process details.
But your statement raises a new question. Where and what are the
components of "load dump protection" that might be expected to
sink the overshoot energy? Is this some new feature of an alternator
for which we are not familiar? What are these energy-sinking devices
that need resting between events to cool off?
Hopefully you will end up with far more evaluation, studying, and testing
than what you listed below as its not adequate nor has it addressed ALL the
problems I have addressed.
Never suggested it was. It's a beginning that goes to satisfaction
of my own curiosity and the sketch was offered as a means for
revealing those thoughts to you . . . nothing more.
You really should test all the brands of
alternators you intend to approve of and in the several different types and
amps in each style. There are differences to consider. For example different
regulator transient response as well as the winding charactericts which will
determine the load dump information.
Yup . . . not a simple task and it won't happen quickly.
It can happen quicker if folks interested in doing such things
share their work, deduce where variables cited dilute the
value of comparisons.
Obviously, we'll never test every brand/configuration of
alternator available . . . but there are statistical
sampling techniques that improve the accuracy on upper
and lower bounds that you adopt for designing a new
product or system.
Further you should take note of the fact just how much (or more important,
how little) is replaced in rebuilt alternators as if you know what is
replaced you would never recommend a rebuilt alternator (rebuilt is a
misnomer minimal repair is what actually happens).Junk yard is not a source
for ANY aircraft as who knows how close to failure the parts are.
Really? If the system is truly failure tolerant, why
would we dissuade anyone from using a salvage yard take-off?
Who knows, maybe he can find a good deal for a device of
a Mercedes or something. The goal of failure tolerant design
is to take reliability concerns for safety out of the decision.
In any
event testing alone, with out first doing an analysis and manufacturers
detailed data is NEVER sufficient. Both Myself and Jet Pilot found getting
more detailed information was not easy and getting past the sales staff if
difficult at best. However a lot of useful information was passed on and
poo-pooed on this groups list.
Forgive me. What information beyond hearsay? I have seen
no documents the manufacturing community offered here. Have
I missed something? Paul, it's precisely these kinds of
words that raise concerns for your own "hidden agenda". You
appear to totally dismiss failure tolerance and absolute
control as noble design goals. As one who has made a living
in this environment for nearly 40 years, I'm perplexed by this.
If these are NOT noble goals, then what goals would you suggest
replaces them? I've not seen one white paper, not one schematic,
not one array of test data and interpretation of its significance . . .
Yup, so in lieu of good data from the source, we gather
what we can in the field and then utilize those products
ways that do not compromise safety.
Also be sure to test with a full load current and zero fixed load. Note my
selected 50 amp rated alternator is specified to put out 70 amps at 13V and
more amps at lower voltages so a full output failure results in a much
higher current than your suggested testing which based on my testing is not
nearly worst case!
Yes . . . that's a subsequent test investigation that looks at
runaway conditions where the alternator is force to max-out. Or
if severly overloaded, one might expect greater-than-nameplate
output current. Name plates are often but should not be LIMITS
to performance but guanranteed (like those breaker curves?). There
are explainable conditions under which larger (and smaller) values
can be expected.
Another comment about getting the real data first. My NEW
alternator came with a computer printout of the actual alternator during
final test prior to shipment. Note the full amp output is a lot higher than
past comments have been clearly assumed on this list in the past.
I have assumed nothing . . . and I don't think others here on
the List have assumed anything either.
. . . .40% higher
is not small in my opinion and under load dump conditions the load being
dumped is much higher energy as well as the peak voltage.
Your opinion may be well based . . . so? This means we design
load dump mitigation for some head-room over name-plate-value.
That's all part of the ball game.
My testing was
based on a real duplication of a typical aircraft wiring including wire
gauge and lengths as well as flight batteries. It started with your OVP and
contactor with the diode on the contactor coil. Very different than what
your sketch shows. Also very long alternator failure point to final
contactor opening requiring voltage clamping during that time of a lot more
energy than what has been assumed in one of your tests from years ago.
Paul, I was only trying to explain my strongest curiosities for
the moment that focused on alternator/regulator performance that
was in no way influenced by methodology for control or OV protection.
I was hoping that you might have data that went to those questions.
The sketch illustrated a tool for getting just that data. I WAS hoping
to focus on one item at a time starting with alternator/regulator then
control philosophies/techniques and finally over-voltage protection.
But then we have a large and fundamental difference on how to design any
electrical (including aircraft) systems. My approach is to discard many of
the proven pilot opportunities to mess up that have been a reason for past
crashes and leap into the 21st century. Building on the past and not address
the fundamental cause of most accidents is not progress in my opinion. The
more pilot required actions greatly increases the pilots lack or incorrect
action. Today there is no need to do things manually in most cases. Every
manual control available to the pilot 's another opportunity to make a
mistake that can lead to a crash.
What percentage of crashes have root causes in electrical system
failures? What scenarios (FMEA) can you imagine that the complexities
of any of the Z-Figures present extra-ordinary operational problems
to the pilot? A light comes on, two switches are repositioned, DONE.
Your words suggest a marketing philosophy based on a climate of
fear . . . one of the most powerful behavior modification tools
available to Madison Avenue (or government). Please assuage my
concerns. IF a tool supporting your endeavors is to scare the socks
off (and dollars out?) of the ignorant consumer, then your purpose
and actions here are unwelcome. I'd rather we share good science.
Today we have Integrated Solid state
switches/circuit breakers. Schottky diodes are not really needed much less
silicon bridges which have no use in aircraft. Yes Solid state switching is
easy to make with full bi-directional isolation and ON resistance less that
of mechanical relays etc switching (as low as 0.002 ohms ON resistance). The
pilot needs to be notified of any CB failure not by finding out by failure
of the component to work for example.
CB failure? I have worked ONE, count 'em, ONE CB failure issue in
decades. That had to do with a design flaw in the product. Recall when
we discussed the consequences of not having the spring-insulator shown
in:
http://aeroelectric.com/Pictures/Breakers/W31_1.jpg
Circuit breakers/fuses are just not high on my list of performance concerns.
Paul, you seem to be working on another plane of
existence. A plane that is shared by many of my customers in the
VLJ business. I'm seeing trends toward a LOT of bells and whistles
driven by software and the latest in electro-whizzies. I design
my products to integrate with those systems . . . it's my job
and I get paid well for it. But we're working with RV's and
Kitfoxes. There are very few Lancairs or Glasairs interested in
what the 'Connection has to offer. Those folks have so much invested
in their projects that most simply farm their electrical system
out to whoever offers the most attractive combination of glass and price
. . .
architecture and understanding their airplane is WAAAyyyy down
on the list of concerns.
Dave Saylor, are you reading this? How many of your Lancair
customers give a rat's patootie about components of their airplane's
electrical system work? What percentage would welcome offloading
understanding and responsibility to the operation of some electronics
behind the touch-screen?
The aircraft instruments have migrated from steam gauges to flat panels yet
we still find the old contactor relay// switch approach of 1950 etc and that
ignores the modern components available today that are far more reliable and
more pilot friendly.
Excellent marketing hype. Please quantify "reliability" as it relates to
safety or cost of ownership in a failure tolerant system. In particular,
tie this to return on investment in an airplane that on average is
flown 50 hours a year and seldom ventures into IMC and spends very
time flying in the dark.
It would be interesting to survey the OBAM aircraft marketplace and
see how often the guy uses/needs all those electro-whizzies on
the panel. I have 850 or so logged hours. I've punched perhaps
a dozen cloud layers. Except for punching layers, all of my flying
from J-3 to A-36 could have been handily accomplished with the
electrical system shut down - using hand-helds and flashlight
from my flight bag.
I'll suggest that for the majority of readers on this List
the electrical system in their project will offer no greater
criticality than I have experienced over the last 27 years.
Its a fact that pilot error is the major cause of accidents. Its pilot error
if you run out of fuel, deplete the battery based on an assumption of
battery condition and electrical load etc etc. The requirement to throw a
switch in an emergency is bad design if there is a reasonable solution that
eliminates the mechanical pilot action and its done automatically. Its sad
that there is no truly modern system available at a reasonable price on the
market today that automates the system and provides the pilot with useful
real time electrical system conditions. My designs have been peer reviewed
by my (multiple) peers and all have stated its both more reliable and a
great improvement to current 1950's parts and today's arrangements and
approaches. You have long promoted fly the airplane and trouble shoot back
on the ground which is not what your design requirement to turn on and off
the alternator in flight and a simple voltage check is enough for preflight.
Personal situation has delayed getting my system on the market.
Okay, Paul's agenda identified? I have a customer who asked for some
advice some years ago about designing a glass-panel, does-everything-
but-wash-dishes, power management system for light aircraft. He
threw in a programmable check list to boot. The thing markets for
over $5,000.
Paul, I'm writing and designing for folks who choose NOT to
worry and have FUN building, maintaining and flying an airplane.
You appear focused on "reliability" and preventing Joe Cool
pilot from loosing his cool when presented with an electrical
system conundrum. I prefer to offer solutions where the electrical
system components are easily acquired, easily understood by the user,
and TOTAL cost is probably under $2,000. Further, Joe Cool is
qualified to operate his behaving or mis-behaving system in confidence.
The E-bus is a good example where there is a design requirement to have a
group of avionics disabled during part of the flight and then guess about
how much battery life is left.
This statement demonstrates that you've NOT read and understood
the design goals for the e-bus and the admonition that the most
reliable electrical system flies on a battery of KNOWN capacity.
. . . A simple additional electrical instrument I
have designed allows the pilot to simply see the real flight time left and
change the load and have the flight time left update. It also determines the
true battery life dynamically. If I am IFR I may need a different set of
avionics than what is on the E bus for example depending on the actual
flight conditions. Or what if the battery power left at any point is less
that what was predicted or measured months ago?. I know of several off
field crashes due to the battery being depleted well before the expected
time. Another bad design to assume something in particular when it ns not
required to assume. Fuel tank gauges system when the only accurate
requirement is full and empty has been replaced with fuel flow measurement
and totalized as seen in modern automobiles. No reason the battery cannot be
treated the same way, sure its a little more complex but not hard to do with
reasonable accuracy.
There are many ways to make flying safer than having a check list of which
switches to throw under different failure modes and make assumptions of
flight time left for example. How about a warning and a count down display
that tells the time left to fly and updates as the pilot changes the
equipment powered on. No action is required if the time remaining is long
enough.
Do you have ANY idea what it takes to get such a product
onto a TC aircraft? There are valid (if not overworked)
concerns about the accuracy, reliability and effects on
pilot mind-set when we put highly automated devices into
the flight management loop. I'm not suggesting that your
product is any less valuable if you do NOT jump all the
regulatory hoops but I am suggesting that when you replace
UNDERSTANDING and COMPETENT operation with an electro-whizzy,
the potential for unintended consequences are there. Further,
when we design and sell such devices, we're in essence taking
on responsibility for operation of that portion of the aircraft.
I don't mention this from any perspective of assumed liability,
only from the perspective of Joe Cool pilot who is now even
more ignorant of his system and more dependent upon his suppliers
to manage it. Yes, modern electronics lets us do many interesting
and sometimes amazing things. We'll have to leave it up to
our customers to decide what dollars are better spent on
the panel as opposed to fuel and tires.
I prefer to preach the doctrine of low parts count, low
cost of ownership, simple-operations backed up by UNDERSTANDING
of how the system works. I don't believe that products and
ideas from a 787 trickle down well into an RV.
Your insistence of performing your own testing is fine but you are
discarding months of investigation as well as hundreds of hours of testing
and analysis. On the other hand it will save me a lot of time producing a
machine readable copy etc.
I am discarding nothing. It was my hope that I SUPPORT
what you've accomplished and that things you're doing would
SUPPORT what I'm doing. That appears not to be part of your
professional modus operandi.
A lot of people blindly used your OVP crowbar until it was used with Vans
aircraft and had many reported failures.
And not one user of the crowbar OVP system contacted me
for his/her money back. Not one user came forward even
when offered a $50 bonus on top of money back if they
would help me understand the circumstances under which
their problems occurred.
As far as I know there was never
and failure analysis to prove the true reason for the failures.
. . . but my requests for data from folks who were ostensibly
in communication with "victims" produced no feedback from
the field.
My own
testing found fault at least two faults with the OVP design but they only
caused false tripping and the real reason appeared to be the use of the
contactor and perhaps rebuilt alternators with possible second rate (read
lower cost) regulators that could not stand up to the resulting load dump
voltage peaks. In any event the OVP design was not properly designed in the
first place likely due to the test first and skip the analysis under
transient conditions.
It is true I had intended to produce an engineering document VS a
technicians experimental results.
Excellent! There is nothing anyone has said that argues with
that. I produced and published volumes of data and analysis
that argued with your assertions with no responses other than
to aspersions cast upon my skills and integrity as a designer.
To date (including my most recent, narrow request for data
that would define alternator/regulator overshoot performance)
I don't recall that you've answered a single direct question.
I have far too much to do, so its easy to simply bow out. Further I will not
comment on your results as I have better things to do. There is no need to
try to discuss your approach as your mind is seemingly always made up ahead
of time.
You win and I think the group looses. Jet Pilot tried with a lot of real
research and was not listened to either.
Other than a lot of tense words in e-mails, he produced no documents
worthy of a teacher who has practical assemblage of simple-ideas to share.
I have a standing offer to ANYONE . . . George, Eric, yourself . . .
anyone to publish any credible work. If you'd like your work-product
published and indexed on aeroelectric.com, you need only produce it.
We have very very different backgrounds and approaches to design. I had
hoped we could work together but that is not to be. I simply do not have the
time, nor can I stand the frustration of writing one paragraph and getting a
response of several pages of comments which are mostly, to me, not to the
point.
Absolutely agree. You don't embrace failure tolerance . . . else
your tools for scaring the potential consumer are crippled. You
don't embrace teaching your customers how components of their
system work toward the goal of competent assemblage and
operation by the user. Those are the points I write and design
to.
Paul, it's apparent to me now that nothing has changed in
either your goals, confrontational mind-set, and inability/
unwillingness to discuss simple-ideas as they relate to
servicing our respective constituents with practical designs.
I'll suggest that your design philosophy and products are
better suited to pilots who have evolved in the "padded
cockpit" environment and like to "drive" high-dollar,
high-performance airplanes. Your offerings might find more
favorable reception on a Lancair List. If you really believe
this group has lost, then start your own group. There are about
1,500 folks on this List who are potential consumers of your
philosophical and physical work product. If you can entice them
away from this group, then more power to you sir. If you have
a better way, then sell it. The marketplace is our ultimate judge
of success. I wish you well.
Bob . . .
| - The Matronics AeroElectric-List Email Forum - | | Use the List Feature Navigator to browse the many List utilities available such as the Email Subscriptions page, Archive Search & Download, 7-Day Browse, Chat, FAQ, Photoshare, and much more:
http://www.matronics.com/Navigator?AeroElectric-List |
|
|
|
Back to top |
|
 |
jbr79r(at)yahoo.com Guest
|
Posted: Sun Jul 13, 2008 12:08 pm Post subject: Nippondenso alternator question |
|
|
Hi Bob
I have been trying to follow this thread with little luck, mainly because I got in late and I don't have time for it. But, that said I want to say there are a lot of Glasairs other than my own that swear by your info and are flying your systems. My Glll has the dual bat dual alternator system and has run perfectly for 4 yrs. Others I know, the same. Keep up the good work
Jim Robinson
Glll N79R
--- On Sun, 7/13/08, Robert L. Nuckolls, III <nuckolls.bob(at)cox.net> wrote:
From: Robert L. Nuckolls, III <nuckolls.bob(at)cox.net>
Subject: Re: Nippondenso alternator question
To: aeroelectric-list(at)matronics.com
Date: Sunday, July 13, 2008, 10:47 AM
<nuckolls.bob(at)cox.net>
To: aeroelectric-list(at)matronics.com
Subject: Re: Nippondenso alternator question
At 10:59 PM 7/12/2008 -0700, you wrote:
<info(at)mtfind.com>
Well (very sadly but it did seem too good to be true and I am not surprised)
I had hoped for mutual cooperation but I guess you want to do it all your
self. Good timing as I was just finishing the first part of the planned
discussion.
WHOA! There was no intent on my part to exert any
form of control over how you responded to this
new initiative. If you have information to share
on any topic and in any form, I'm sure it will
be welcomed by many including myself . . .
Be my guest, I had thought you had changed. Clearly you want to frive the
discussion VS get the benefit of my extensive work.
Absolutely! However, I just finish an archiological dig
through records and drives looking for work I did on a
project at Beech some years back. The $time$ expended looking
COULD have been well spent looking . . . but in this case,
BETTER spent repeating the work which I am going to have
to do anyway. I was only attempting to perhaps relieve you
of some efforts trying to resurrect past work.
Random comments as its not worth my time to put them in ordered sequence. I
have made some suggestions about how and what to test to avoid missing
information that is not gathered just using your sketched circuit.
You are incorrect about my approach and intent and about my past analysis
and testing which is in my opinion adequate to determine the problem and I
have "crafted" a proven solution. In my opinion there is ZERO need
for more
testing other for self aggrandizement.
Wrong. The repeatable experiment is the CORE of good science.
No how much testing your or I do, there is always risk of
error, variability in process or materials, and variability
in interpretation of results. Finally, there are individuals
in our society that will stand up, point a finger and accuse
the tester of having some hidden agenda. There is no stronger
validation of anyone's work than to say, "Here's what I did,
here's what happened, here's the significance of the data.
Oh, by the way, Mr. X in Arizona and Ms. Y in Georgia did
similar if not identical work and our respective conclusions
support each other." Besides, I need that equipment and test
set-up for other activities.
I find this sad as you have not seen
any real results of my testing nor the scope of it. Reading your suggested
approach I find little to agree with so there is no point in my being a part
of your long promised study.
Paul . . . I don't know what I can write that
encourages you not to respond to what I do in the
worst possible light. You have not published one
White Paper, not one schematic, not one explanation
of features that helps me or anyone else understand
diddly-squat about what you're proposing.
Further most of your below comments about my position are totally incorrect
assumptions which is not surprising as you have never spent the time to find
out what my approach is; the amount of analysis, investigation nor testing
setup and results.
But Paul, you have not shared even the smallest part of what
you've accomplished. I've reviewed our past exchanges and
the majority of your efforts were directed at tearing down
what I had been doing successfully for decades. The only
data you cited came from manufacturer's data sheets.
I will not tolerate testing as anything other as proof of
pre testing design analysis. I also simply will not design using assumptions
or unofficial verbal assurances from one manufacturer its safe to exceed the
specifications as that is simply a high risk approach no engineer will do.
If you're talking about crow-barring breakers, exactly WHAT
limit was being violated? I cited the Mil Std under which all
those breakers were certified that requires they function as
advertised when subjected to fault currents of over 1000 amps.
Many times the values cited in guaranteed performance curves. Curves you
chose to interpret as limits.
My results are identical design solution for all reasonable alternator but
clearly its not reasonable to allow any alternator to be covered and that
position indicates to me a lack of modern alternator designs etc. Further
you seem fixated on maintaining several design flexiblities and pilot
control that I feel is not only not required but potentially dangerous.
??? Now I'm really lost. Are you suggesting that alternators
can and should be used for aircraft in the manner we've accepted
for cars? No control whatsoever, no ov protection, no ability
to manage loads and power generation in multiple alternator
systems? Is it your suggestion that the design and operation
protocols common to 99.999% of all aircraft flying can be
summarily dispensed with?
Also your sketch does not reproduce the real world load dump conditions what
with fixed load and relay contact bounce in the real circuit.
The sketch depicts only the energy sources and sinks and the
organization needed to explore the characteristics of an alternator.
No more. Exploration of contactor performance in the task of
energy control is a separate experiment.
Finally it
appears you intend to have a constant string of load dumps which is very
likely to destroy the internal to the regulator load dump protection
components. Each single load dump needs time for the protection circuits to
cool down.
The "string" for T(off) can be ANYTHING out to infinity. This is a
general
arrangement I used 30 years ago to fine tune the dynamics of
voltage regulator designs. Obviously, getting the energy signature
from a particular combination of L(fixed)+L(switched) can be done
with very few events. The schematic was intended to describe setup,
not process details.
But your statement raises a new question. Where and what are the
components of "load dump protection" that might be expected to
sink the overshoot energy? Is this some new feature of an alternator
for which we are not familiar? What are these energy-sinking devices
that need resting between events to cool off?
Hopefully you will end up with far more evaluation, studying, and testing
than what you listed below as its not adequate nor has it addressed ALL the
problems I have addressed.
Never suggested it was. It's a beginning that goes to satisfaction
of my own curiosity and the sketch was offered as a means for
revealing those thoughts to you . . . nothing more.
You really should test all the brands of
alternators you intend to approve of and in the several different types and
amps in each style. There are differences to consider. For example different
regulator transient response as well as the winding charactericts which will
determine the load dump information.
Yup . . . not a simple task and it won't happen quickly.
It can happen quicker if folks interested in doing such things
share their work, deduce where variables cited dilute the
value of comparisons.
Obviously, we'll never test every brand/configuration of
alternator available . . . but there are statistical
sampling techniques that improve the accuracy on upper
and lower bounds that you adopt for designing a new
product or system.
Further you should take note of the fact just how much (or more important,
how little) is replaced in rebuilt alternators as if you know what is
replaced you would never recommend a rebuilt alternator (rebuilt is a
misnomer minimal repair is what actually happens).Junk yard is not a source
for ANY aircraft as who knows how close to failure the parts are.
Really? If the system is truly failure tolerant, why
would we dissuade anyone from using a salvage yard take-off?
Who knows, maybe he can find a good deal for a device of
a Mercedes or something. The goal of failure tolerant design
is to take reliability concerns for safety out of the decision.
In any
event testing alone, with out first doing an analysis and manufacturers
detailed data is NEVER sufficient. Both Myself and Jet Pilot found getting
more detailed information was not easy and getting past the sales staff if
difficult at best. However a lot of useful information was passed on and
poo-pooed on this groups list.
Forgive me. What information beyond hearsay? I have seen
no documents the manufacturing community offered here. Have
I missed something? Paul, it's precisely these kinds of
words that raise concerns for your own "hidden agenda". You
appear to totally dismiss failure tolerance and absolute
control as noble design goals. As one who has made a living
in this environment for nearly 40 years, I'm perplexed by this.
If these are NOT noble goals, then what goals would you suggest
replaces them? I've not seen one white paper, not one schematic,
not one array of test data and interpretation of its significance . . .
Yup, so in lieu of good data from the source, we gather
what we can in the field and then utilize those products
ways that do not compromise safety.
Also be sure to test with a full load current and zero fixed load. Note my
selected 50 amp rated alternator is specified to put out 70 amps at 13V and
more amps at lower voltages so a full output failure results in a much
higher current than your suggested testing which based on my testing is not
nearly worst case!
Yes . . . that's a subsequent test investigation that looks at
runaway conditions where the alternator is force to max-out. Or
if severly overloaded, one might expect greater-than-nameplate
output current. Name plates are often but should not be LIMITS
to performance but guanranteed (like those breaker curves?). There
are explainable conditions under which larger (and smaller) values
can be expected.
Another comment about getting the real data first. My NEW
alternator came with a computer printout of the actual alternator during
final test prior to shipment. Note the full amp output is a lot higher than
past comments have been clearly assumed on this list in the past.
I have assumed nothing . . . and I don't think others here on
the List have assumed anything either.
. . . .40% higher
is not small in my opinion and under load dump conditions the load being
dumped is much higher energy as well as the peak voltage.
Your opinion may be well based . . . so? This means we design
load dump mitigation for some head-room over name-plate-value.
That's all part of the ball game.
My testing was
based on a real duplication of a typical aircraft wiring including wire
gauge and lengths as well as flight batteries. It started with your OVP and
contactor with the diode on the contactor coil. Very different than what
your sketch shows. Also very long alternator failure point to final
contactor opening requiring voltage clamping during that time of a lot more
energy than what has been assumed in one of your tests from years ago.
Paul, I was only trying to explain my strongest curiosities for
the moment that focused on alternator/regulator performance that
was in no way influenced by methodology for control or OV protection.
I was hoping that you might have data that went to those questions.
The sketch illustrated a tool for getting just that data. I WAS hoping
to focus on one item at a time starting with alternator/regulator then
control philosophies/techniques and finally over-voltage protection.
But then we have a large and fundamental difference on how to design any
electrical (including aircraft) systems. My approach is to discard many of
the proven pilot opportunities to mess up that have been a reason for past
crashes and leap into the 21st century. Building on the past and not address
the fundamental cause of most accidents is not progress in my opinion. The
more pilot required actions greatly increases the pilots lack or incorrect
action. Today there is no need to do things manually in most cases. Every
manual control available to the pilot 's another opportunity to make a
mistake that can lead to a crash.
What percentage of crashes have root causes in electrical system
failures? What scenarios (FMEA) can you imagine that the complexities
of any of the Z-Figures present extra-ordinary operational problems
to the pilot? A light comes on, two switches are repositioned, DONE.
Your words suggest a marketing philosophy based on a climate of
fear . . . one of the most powerful behavior modification tools
available to Madison Avenue (or government). Please assuage my
concerns. IF a tool supporting your endeavors is to scare the socks
off (and dollars out?) of the ignorant consumer, then your purpose
and actions here are unwelcome. I'd rather we share good science.
Today we have Integrated Solid state
switches/circuit breakers. Schottky diodes are not really needed much less
silicon bridges which have no use in aircraft. Yes Solid state switching is
easy to make with full bi-directional isolation and ON resistance less that
of mechanical relays etc switching (as low as 0.002 ohms ON resistance). The
pilot needs to be notified of any CB failure not by finding out by failure
of the component to work for example.
CB failure? I have worked ONE, count 'em, ONE CB failure issue in
decades. That had to do with a design flaw in the product. Recall when
we discussed the consequences of not having the spring-insulator shown
in:
http://aeroelectric.com/Pictures/Breakers/W31_1.jpg
Circuit breakers/fuses are just not high on my list of performance concerns.
Paul, you seem to be working on another plane of
existence. A plane that is shared by many of my customers in the
VLJ business. I'm seeing trends toward a LOT of bells and whistles
driven by software and the latest in electro-whizzies. I design
my products to integrate with those systems . . . it's my job
and I get paid well for it. But we're working with RV's and
Kitfoxes. There are very few Lancairs or Glasairs interested in
what the 'Connection has to offer. Those folks have so much invested
in their projects that most simply farm their electrical system
out to whoever offers the most attractive combination of glass and price
. . .
architecture and understanding their airplane is WAAAyyyy down
on the list of concerns.
Dave Saylor, are you reading this? How many of your Lancair
customers give a rat's patootie about components of their airplane's
electrical system work? What percentage would welcome offloading
understanding and responsibility to the operation of some electronics
behind the touch-screen?
The aircraft instruments have migrated from steam gauges to flat panels yet
we still find the old contactor relay// switch approach of 1950 etc and that
ignores the modern components available today that are far more reliable and
more pilot friendly.
Excellent marketing hype. Please quantify "reliability" as it
relates to
safety or cost of ownership in a failure tolerant system. In particular,
tie this to return on investment in an airplane that on average is
flown 50 hours a year and seldom ventures into IMC and spends very
time flying in the dark.
It would be interesting to survey the OBAM aircraft marketplace and
see how often the guy uses/needs all those electro-whizzies on
the panel. I have 850 or so logged hours. I've punched perhaps
a dozen cloud layers. Except for punching layers, all of my flying
from J-3 to A-36 could have been handily accomplished with the
electrical system shut down - using hand-helds and flashlight
from my flight bag.
I'll suggest that for the majority of readers on this List
the electrical system in their project will offer no greater
criticality than I have experienced over the last 27 years.
Its a fact that pilot error is the major cause of accidents. Its pilot error
if you run out of fuel, deplete the battery based on an assumption of
battery condition and electrical load etc etc. The requirement to throw a
switch in an emergency is bad design if there is a reasonable solution that
eliminates the mechanical pilot action and its done automatically. Its sad
that there is no truly modern system available at a reasonable price on the
market today that automates the system and provides the pilot with useful
real time electrical system conditions. My designs have been peer reviewed
by my (multiple) peers and all have stated its both more reliable and a
great improvement to current 1950's parts and today's arrangements and
approaches. You have long promoted fly the airplane and trouble shoot back
on the ground which is not what your design requirement to turn on and off
the alternator in flight and a simple voltage check is enough for preflight
| - The Matronics AeroElectric-List Email Forum - | | Use the List Feature Navigator to browse the many List utilities available such as the Email Subscriptions page, Archive Search & Download, 7-Day Browse, Chat, FAQ, Photoshare, and much more:
http://www.matronics.com/Navigator?AeroElectric-List |
|
|
|
Back to top |
|
 |
info(at)mtfind.com Guest
|
Posted: Sun Jul 13, 2008 12:25 pm Post subject: Nippondenso alternator question |
|
|
----Bob: If you knew my background you would understand how wrong you are
about
my design approach as well as nearly all your comments in this and many
other responses.
My resume includes personal congratulations from the President of the USA
for outstanding scientific excellence, Another is the Presidents award for
outstanding engineering performance at Lockheed. Also there is the multiple
management positions typically manager of the command and control systems
for spacecraft including the Space Telescope.
I have published OBAM designs and design details on several other groups, my
web site, and three national mags. I guess there is a world outside of
aeroelectric.
But this post is breaking my comment not to post again.
I do congratulant your efforts in supporting the group and best wishes.
Paul
- Original Message -----
From: "Robert L. Nuckolls, III" <nuckolls.bob(at)cox.net>
To: <aeroelectric-list(at)matronics.com>
Sent: Sunday, July 13, 2008 9:47 AM
Subject: Re: Nippondenso alternator question
| - The Matronics AeroElectric-List Email Forum - | | Use the List Feature Navigator to browse the many List utilities available such as the Email Subscriptions page, Archive Search & Download, 7-Day Browse, Chat, FAQ, Photoshare, and much more:
http://www.matronics.com/Navigator?AeroElectric-List |
|
|
|
Back to top |
|
 |
mrspudandcompany(at)veriz Guest
|
Posted: Sun Jul 13, 2008 1:10 pm Post subject: Nippondenso alternator question |
|
|
Thank you Paul, for going silent!!
Your negative contribution to this forum has taken a lot of time and has
accomplished nothing. Since you have only tried to tear down Bob's work,
with NO positive contributions. Trying to promote your agenda by trashing
someone else does not work.
Bob, as opposed to Paul, has published many documents to assist the OBAM
community. There are a variety of different approaches to suit the needs of
most builders. I have asked questions on several occasions and got a good
accurate professional reply. In my opinion, the KISS approach with
attention to failure tolerance is the best method for the average builder.
I must commend Bob for the volumes of useful info, free for the taking.
Thanks Bob, and keep up the good work.
Roger
| - The Matronics AeroElectric-List Email Forum - | | Use the List Feature Navigator to browse the many List utilities available such as the Email Subscriptions page, Archive Search & Download, 7-Day Browse, Chat, FAQ, Photoshare, and much more:
http://www.matronics.com/Navigator?AeroElectric-List |
|
|
|
Back to top |
|
 |
henador_titzoff(at)yahoo. Guest
|
Posted: Sun Jul 13, 2008 1:42 pm Post subject: Nippondenso alternator question |
|
|
Here's what's really strange about Paul's reply. I've worked in the aerospace field for decades. I've never known engineers to receive USA Presidential awards unless they were way up at the top and extremely good politicians, totally away from true engineering. Usually these guys are so far removed from the lab and from where the real action is that they do not know what's going on. Instead, they are at meeting after meeting determinng budgets and how to kill programs, who to promote, who to lay off, taking credit for what people far below have done, etc. So Paul and whatever your last name is, if you truly have received awards from the USA president, congratulations, you are a great politician.
Henador Titzoff
---
| - The Matronics AeroElectric-List Email Forum - | | Use the List Feature Navigator to browse the many List utilities available such as the Email Subscriptions page, Archive Search & Download, 7-Day Browse, Chat, FAQ, Photoshare, and much more:
http://www.matronics.com/Navigator?AeroElectric-List |
|
|
|
Back to top |
|
 |
|
|
You cannot post new topics in this forum You cannot reply to topics in this forum You cannot edit your posts in this forum You cannot delete your posts in this forum You cannot vote in polls in this forum You cannot attach files in this forum You can download files in this forum
|
Powered by phpBB © 2001, 2005 phpBB Group
|