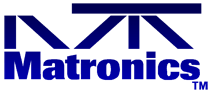 |
Matronics Email Lists Web Forum Interface to the Matronics Email Lists
|
View previous topic :: View next topic |
Author |
Message |
GrummanDude
Joined: 15 Jan 2006 Posts: 926 Location: Auburn, CA
|
Posted: Tue Apr 28, 2009 11:28 am Post subject: Percent power. How to calculate? . . . Survey says! |
|
|
My test condition had to be 30 F degree air for the carb heat rise
test.
I found 30 F degree air at roughly 5000 feet.
My next steps were:
(1) I used the POH (which is not FAA approved) to determine where 75%
power should be.
(2) I eye-balled the 5000 foot condition and it showed that I needed
roughly 2600 rpm and 11 gallons/hour
(2a) The plane had fuel flow so that part was easy.
(2b) The mechanical tach was plus or minus 20 rpm most of the
time.
(3) We did the carb heat rise test. We got the required 90 degree F
temperature rise.
(4) I then went into the POH and iterated on the data to determine the
values for the final test condition of
(4a) 5120 MSL
(4b) 30 F degree air
(4c) 2590 rpm
(4d) 10.8 gph.
(5) The final calculation for 75% power was 2592 rpm at 10.8 gph at 30F
at 2590 feet MSL.
So, my eyeball was close.
Note: I did not have a manifold pressure gauge since a manifold
pressure gauge is not required in a plane with a fixed pitch propeller.
I used the POH since that is what most of the pilots use to determine
percent power.
============
Using the Lycoming Engine Manual:
(1) I have the Lycoming book. In it, my Figure 3-17 on my page 3-33 is
for O-360-A series with a MA-4/5 carb.
OK, the carb shouldn't make that much difference.
(2) I talked to Ken and Gary at Lycon and they tell me they have run
into this problem before with this figure, for fixed pitch props.
Their thought, the Lycoming data was determined from constant rpm at
specific manifold pressures. That is, using a constant speed
propeller, they determined percent power at specific manifold
pressures. The fuel flow they got was for those conditions.
(3) The resolution on the temperature scale on the figures in the
Lycoming book is guesswork at best.
(3a) Let's say, I pick 2600 rpm and 24 inches MAP (roughly wide
open throttle) for A at 5000 feet.
(3b) I use the same starting condition for B
(3c) if I pick, on the figure 3-17 for my Ts, at 5000 feet, I get
something like 40-45 F. Resolution really sucks.
(3d) drawing from C to D, I get about my test condition.
(4) Calculating the correction factor, I get about 1.01 to 1.06. So HP
= 152*1.01 or 1.016 = 153.4 or 154 for E
(5) going back across the chart to 2600 rpm for F,
(6) and dropping down to 2600 rpm for G, my fuel flow should be 12.8
gph and a lot more than 75% power.
(7) Conclusion. Test condition at 5000 feet, is no where near 75%
power with 24 inches MAP and full throttle.
Note: the charts are generated for full throttle operation at constant
rpms.
=============
Three ways to compute % power.
(1) Using the POH from my plane, 75% power is at roughly 10.8 gph. (at
134 knots). Mixture recommended leaned.
(2) Using an FAA approved Flight Manual from a 2005 Tiger, 75% power is
at roughly 11.4 gph
with the mixture at best power. TAS is 128 knots Note: No
reference to rpm in Flight Manual.
(3) Using Lycomings chart, 75% power comes in at 11 gph at 2600, back
calculating . . . .
BUT, ONLY IF I START WITH AN INITIAL CONDITION OF 21.5 MAP AT
2600 RPM.
(3a) I could say this to the FAA, that these were my conditions,
but, without manifold pressure, I couldn't substantiate it.
=============
In hind site, I wish I had installed a manifold pressure gauge. Both
the DER and I believed the POH is what pilots would be using to fly at
75% power. We had no idea that 75% power meant different things in
different references. We had no idea the FAA approved flight manual
for the AG5B would be a gallon an hour more under the same conditions.
=============
Question (1) : Does anyone use the POH (or FAA approved Flight Manual)
to fly at percent power?
Question (2): IF so, just for grins, given what you know,
IF you were flying at 5000 feet and 30 degree air
What rpm and fuel flow would you be aiming for?
Question (3): Do you use the Lycoming reference to determine percent
power?
Question (4): What speed (TAS) would you expect to see?
| - The Matronics TeamGrumman-List Email Forum - | | Use the List Feature Navigator to browse the many List utilities available such as the Email Subscriptions page, Archive Search & Download, 7-Day Browse, Chat, FAQ, Photoshare, and much more:
http://www.matronics.com/Navigator?TeamGrumman-List |
|
_________________ Gary
AuCountry Aviation
Home of Team Grumman |
|
Back to top |
|
 |
Phil(at)ReliantAir.com Guest
|
Posted: Tue Apr 28, 2009 1:49 pm Post subject: Percent power. How to calculate? . . . Survey says! |
|
|
My 1979 Grumman Tiger's POH is published by Gulfstream Aerospace, Issued
9/30/76 and last revised (rev. 4) 5/12/1983. The title page contains the
this statement: "THIS HANDBOOK INCLUDES THE MATERIAL REQUIRED TO BE
FUNISHED TO THE PILOT BY FAR PART 23". Since it contains performance
information I would assume that it is required by the FAR'S and meets those
requirements, but who knows.
To answer your four questions:
- I have always used the POH to set power.
- 5,000' (at) 30 degree pwr setting would be 2600 rpm 10.7 gph. Interpolated
because 30F degrees is not an option in the charts.
- I only use the Lycoming power chart with Turbo charged engines.
- I would expect to see 134 Kts.
--
| - The Matronics TeamGrumman-List Email Forum - | | Use the List Feature Navigator to browse the many List utilities available such as the Email Subscriptions page, Archive Search & Download, 7-Day Browse, Chat, FAQ, Photoshare, and much more:
http://www.matronics.com/Navigator?TeamGrumman-List |
|
|
|
Back to top |
|
 |
GrummanDude
Joined: 15 Jan 2006 Posts: 926 Location: Auburn, CA
|
Posted: Tue Apr 28, 2009 9:02 pm Post subject: Percent power. How to calculate? . . . Survey says! |
|
|
I flew a 2005 Tiger today with a JPI EDM 800 in it. The 800, as you
know, calculates percent power. It also has manifold pressure.
Between Concorde and Auburn at 5500 feet I found 2 C degree air (38.6
F).
Altimeter setting was 30.50 inches.
I went full throttle and got 23.8 inches of manifold pressure.
(Now, as we all should know by now, the inlet on the AG5B eats
about an inch of pressure so I would suspect the actual manifold
pressure should have been 24.5 inches or so.)
The MAX RPM I could turn was 2650 rpm. Leaned.
The JPI showed 78 percent power.
Fuel flow was 11.7 gph.
----------------------------------------------------------------------
I throttled back to 2590 rpm,
I set the fuel flow for 10.8 gph
MAP was 22.8 inches
The calculated percent power was 75%
It did bounce up to 76% for about 5 minutes so it could
have been on the edge of the calculated power band.
True Air Speed was 132 knots. as measure on the Garmin 430.
----------------------------------------------------------------------
Note, this is no where near the calculated values from the Lycoming
Operators manual.
Note, it is very close to my POH.
Note, compared to the approved flight manual (FM) in the 2005 Tiger
LLC,
what I saw was a faster plane on less fuel at 75% power than
the FM claims.
Note, Given 23.8 MAP and 2650 rpm, at wide open throttle
if I use figure 3-17, Lycoming's Sea-Level and Altitude
Performance, I get 155 hp at 13.5 gph.
(that's 86% power)
----------------------------------------------------------------------
Something is not copasetic.
----------------------------------------------------------------------
I wish my plane was back together. I'd like to run a comparison with
mine and the same airbox/inlet as on the test plane.
--
| - The Matronics TeamGrumman-List Email Forum - | | Use the List Feature Navigator to browse the many List utilities available such as the Email Subscriptions page, Archive Search & Download, 7-Day Browse, Chat, FAQ, Photoshare, and much more:
http://www.matronics.com/Navigator?TeamGrumman-List |
|
_________________ Gary
AuCountry Aviation
Home of Team Grumman |
|
Back to top |
|
 |
flyv35b(at)minetfiber.com Guest
|
Posted: Wed Apr 29, 2009 4:54 am Post subject: Percent power. How to calculate? . . . Survey says! |
|
|
Quote: | In hind site, I wish I had installed a manifold pressure gauge. Both the
DER and I believed the POH is what pilots would be using to fly at 75%
power. We had no idea that 75% power meant different things in different
references. We had no idea the FAA approved flight manual for the AG5B
would be a gallon an hour more under the same conditions.
|
When I installed the O-320 engine in my AA-1C I installed a MP gauge because
I knew there was no data for this engine combination and knowing MP was
almost mandatory to be able to have any reasonable idea of what the power
setting was. This has turned out to be a very good way to determine and
adjust power setting. I can take the power chart from my Bonanza which
shows % power for various RPM and MP settings and temperatures and use it to
determine power with the Grumman. It won't be far off. I would also
install a MP gauge in a Tiger if I owned one even though the factory has
provided info as I believe that MP is important even for a fixed pitch prop
installation. For example: what is your power setting in a dive or even a
500 fpm descent at 2700 rpm? If you don't know the MP you have no idea what
it is! You might be operating at 15" hg. In your case, Gary, with your
engine and prop I would think you would absolutely want a MP gauge.
Cliff
--
We are a community of 6 million users fighting spam.
The Professional version does not have this message
| - The Matronics TeamGrumman-List Email Forum - | | Use the List Feature Navigator to browse the many List utilities available such as the Email Subscriptions page, Archive Search & Download, 7-Day Browse, Chat, FAQ, Photoshare, and much more:
http://www.matronics.com/Navigator?TeamGrumman-List |
|
|
|
Back to top |
|
 |
flyv35b(at)minetfiber.com Guest
|
Posted: Wed Apr 29, 2009 5:02 am Post subject: Percent power. How to calculate? . . . Survey says! |
|
|
Quote: | Between Concorde and Auburn at 5500 feet I found 2 C degree air (38.6 F).
Altimeter setting was 30.50 inches.
I went full throttle and got 23.8 inches of manifold pressure.
(Now, as we all should know by now, the inlet on the AG5B eats
about an inch of pressure so I would suspect the actual manifold
pressure should have been 24.5 inches or so.)
|
I don't think you would achieve 24.5" with your plane. Even the very best
induction systems loose about 1" MP through the air filter and induction
plumbing (at sea level and full throttle). At 5500 ft you would be down to
25" minus the induction system loss of 1" say or maybe 1.5" on the AG-5B.
So 23.8" is reasonable (for the AG-5B induction system). A MP gauge will
tell you a lot about this as you see what the actual MP is on takeoff when
you apply full throttle. You can also take out the air filter and possible
see what effect it has.
Cliff
--
We are a community of 6 million users fighting spam.
The Professional version does not have this message
| - The Matronics TeamGrumman-List Email Forum - | | Use the List Feature Navigator to browse the many List utilities available such as the Email Subscriptions page, Archive Search & Download, 7-Day Browse, Chat, FAQ, Photoshare, and much more:
http://www.matronics.com/Navigator?TeamGrumman-List |
|
|
|
Back to top |
|
 |
GrummanDude
Joined: 15 Jan 2006 Posts: 926 Location: Auburn, CA
|
Posted: Wed Apr 29, 2009 8:52 am Post subject: Percent power. How to calculate? . . . Survey says! |
|
|
Hi Cliff,
My plane does have manifold pressure. As does the Tiger I flew with
the 800. It's just that the Tiger used for the flight tests didn't.
We didn't think it was necessary since the plane didn't come with it.
We thought the POH was enough. Which it should be.
| - The Matronics TeamGrumman-List Email Forum - | | Use the List Feature Navigator to browse the many List utilities available such as the Email Subscriptions page, Archive Search & Download, 7-Day Browse, Chat, FAQ, Photoshare, and much more:
http://www.matronics.com/Navigator?TeamGrumman-List |
|
_________________ Gary
AuCountry Aviation
Home of Team Grumman |
|
Back to top |
|
 |
flyv35b(at)minetfiber.com Guest
|
Posted: Wed Apr 29, 2009 11:04 am Post subject: Percent power. How to calculate? . . . Survey says! |
|
|
I didn't realize you were using someone else's plane for the certification
tests.
Cliff
---
| - The Matronics TeamGrumman-List Email Forum - | | Use the List Feature Navigator to browse the many List utilities available such as the Email Subscriptions page, Archive Search & Download, 7-Day Browse, Chat, FAQ, Photoshare, and much more:
http://www.matronics.com/Navigator?TeamGrumman-List |
|
|
|
Back to top |
|
 |
GrummanDude
Joined: 15 Jan 2006 Posts: 926 Location: Auburn, CA
|
Posted: Wed Apr 29, 2009 10:10 pm Post subject: Percent power. How to calculate? . . . Survey says! |
|
|
The first plane to get my cowling, that is, a cowling that had been
conformed by the FAA to match the tooling and drawings I submitted
(even though my cowling came out of the same tooling) was Greg Ketell's
old plane, N1976T, currently owned by Jeff Keesaman from San Diego.
I've asked Jeff to post his experiences with the cowling on this forum.
Maybe he will someday.
| - The Matronics TeamGrumman-List Email Forum - | | Use the List Feature Navigator to browse the many List utilities available such as the Email Subscriptions page, Archive Search & Download, 7-Day Browse, Chat, FAQ, Photoshare, and much more:
http://www.matronics.com/Navigator?TeamGrumman-List |
|
_________________ Gary
AuCountry Aviation
Home of Team Grumman |
|
Back to top |
|
 |
|
|
You cannot post new topics in this forum You cannot reply to topics in this forum You cannot edit your posts in this forum You cannot delete your posts in this forum You cannot vote in polls in this forum You cannot attach files in this forum You can download files in this forum
|
Powered by phpBB © 2001, 2005 phpBB Group
|