nuckolls.bob(at)aeroelect Guest
|
Posted: Thu May 14, 2009 6:28 am Post subject: Of pop rivets and lock nuts . . . |
|
|
Yesterday I offered a short list of simple ideas that
went to the task of getting life-of-the-airplane
joints between a wire and the airframe. Specifically,
how to get a wire "grounded" in a way that it stays
grounded.
Discussions here on the List have considered the goals
of achieving low resistance, high-longevity connection
between two conductors in a variety contexts. Some
tasks call for temporary or "service" connections
between two wires. In this case, we look to the products
offered by skilled designers and manufacturers of
connectors. They spend a LOT of time figuring out
the simple ideas that keep two mechanically independent
pins in low resistance contact with each other in
spite of moisture, vibration, temperature cycles,
electron flow, etc., etc.
These same designers have reasonable expectations
that users of their products will understand that
while we purchased their product for it's 'temporary'
connection features, the user still has to make the
'permanent' connections between pins and wires.
There are further considerations for supporting the
joint adjacent to the transition between 'permanent'
and 'flexible' segments of the assembly.
When we purchase crimp tools appropriate to the
well considered-components (like PIDG terminals)
then much of the process sensitive actions are
taken care of . . . as long as we follow instructions.
We have a further interest in being able to evaluate
the end-product of our labors. Did we use the right
components/tools? Was the wire properly inserted?
Was the crimp fully seated? etc. etc.
Understanding and acknowledging the skill of folks
who supply us with terminals, crimp tools, and
connectors illuminates a need for the OBAM aircraft
builder to consider his/her part in maintaining the
overall strength of the chain . . .
[img]cid:.0[/img]
No matter how 'good' the rest of the chain's links
might be, inattention to detail at any point negates
the integrity of the whole.
Yesterday I offered a means by which a properly installed
terminal can be electrically and mechanically attached
to the airframe for the purpose of effecting a good
ground connection. I suggested that a combination of
10-32 screw, washer and lock nut would apply mate-up
forces would produce a very satisfactory joint in
terms of performance and longevity. I suggested that
a little silicone grease in the interface would be
a further hedge against ingress of moisture.
This was a best-we-know-how-to-do alternative to
the use of the pop-rivet joint that raised a list
member's curiosity as to potential loss of joint
integrity. There is some value in expanding this
discussion
The driven rivet can be both electrically and
mechanically robust. A #4 (.125) rivet set in a
#30 (.128) hole swells up during the driving process
to apply great pressure (tons per square inch)
against the walls of the hole. Further, sheets of
aluminum assembled with aluminum rivets offer no
risk for effects of dissimilar metals in presence
of moisture/oxygen for electrolytic corrosion. It's
fair to say that an aluminum grounding tab for a
rear mounted battery installed with 4-6 properly
driven rivets has a life-of-the-airplane shot for
performing as intended.
The pop-rivet is a hollow fastener that also
swells in the hole . . . and like it's driven cousin,
applies some forces in tension that holds the
parts together. But unless you use un-plated,
aluminum pop-rivets, there are dissimilar metal
issues (Yeah, you can get monel rivets too).
Further, since the device is hollow, it
cannot generate and maintain the mate-up forces
offered by it's driven cousins. In the case that
prompted this thread, the finished joint was loose
enough to allow the mated up parts to move under
ordinary manipulation with the fingers.
One might deduce from this observation that attaching
the battery ground tab with pop-rivets is
problematic . . . even if the mounted bracket can't
spin on the fastener.
Yesterday, I suggested a 10-32 screw for the works-
good-lasts-a-long-time joint. How much smaller can
we go without serious degradation of the joint?
For grounding of medium wires, say 14AWG or lighter,
an 8-32 is probably fine. Grounding small wires
(20-22AWG) can be tied down with 6-32 hardware.
In all cases, bringing clean surfaces together
with forces equal to the capabilities of the fastener
is required. The use of all-metal lock washers makes
the screw look more like a rivet. The addition of
moisture ingress protection is also a useful ingredient
in this recipe for success.
This little dissertation is not intended to demean
the lowly pop-rivet. Keep in mind that John Thorpe's
very successful T-18 was assembled with "pulled" or
"pop" rivets. See:
http://tinyurl.com/pdhszb
When use within their performance limits, the pop-rivet
has a role to perform in many plays. However, making
up lasts-a-long-time, gas-tight joints for airframe
grounds just isn't one of them.
Bob . . .
| - The Matronics AeroElectric-List Email Forum - | | Use the List Feature Navigator to browse the many List utilities available such as the Email Subscriptions page, Archive Search & Download, 7-Day Browse, Chat, FAQ, Photoshare, and much more:
http://www.matronics.com/Navigator?AeroElectric-List |
|
Description: |
|
Filesize: |
28.41 KB |
Viewed: |
1083 Time(s) |
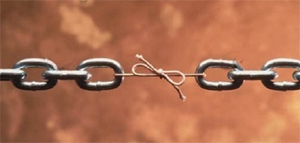
|
|
|