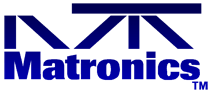 |
Matronics Email Lists Web Forum Interface to the Matronics Email Lists
|
View previous topic :: View next topic |
Author |
Message |
craig(at)craigandjean.com Guest
|
Posted: Fri May 29, 2009 7:10 pm Post subject: Cutting holes with one or more flat sides |
|
|
A number of the items I'm mounting in my panel are designed to be kept from
rotating by a "flat" or two on their threaded shafts. The ignition key
switch and Bose (LEMO) headphone jacks are this way. Short of a custom punch
how do you cut a hole with the matching flats? For the ignition switch I
enlarged a smaller hole with a needle file. It will work but it isn't the
tightest fit. Any other approaches?
-- Craig (701)
| - The Matronics Zenith-List Email Forum - | | Use the List Feature Navigator to browse the many List utilities available such as the Email Subscriptions page, Archive Search & Download, 7-Day Browse, Chat, FAQ, Photoshare, and much more:
http://www.matronics.com/Navigator?Zenith-List |
|
|
|
Back to top |
|
 |
psm(at)att.net Guest
|
Posted: Fri May 29, 2009 7:24 pm Post subject: Cutting holes with one or more flat sides |
|
|
Hi Craig,
Let me recommend the following procedure.
First, make a model of the hole you want out of cardboard, plastic,
plywood, or some other flat material. Then position the model where
you want the hole and mark the outside edge with a Sharpie (I like
ultra fine ones for this). Now all you have to do is remove the
material inside the mark.
I usually start with a small drill followed by a step drill. For a
large hole such as the one needed for a radio I make 4 holes with the
step drill near each corner. That makes enough room to use snips to
start sneaking up on the final line. After the snips, I tend to
use a Dremel tool with a Christmas Tree shaped rotary file. This
allows me to start with the larger diameter to do rough cutting and
finish with progressively smaller diameter portion of the file.
When all done removing material I run a fine file around both sides
of the edge to remove burrs.
I hope this helps.
Paul
XL grounded
At 07:56 PM 5/29/2009, you wrote:
Quote: | A number of the items I'm mounting in my panel are designed to be kept from
rotating by a "flat" or two on their threaded shafts. The ignition key
switch and Bose (LEMO) headphone jacks are this way. Short of a custom punch
how do you cut a hole with the matching flats? For the ignition switch I
enlarged a smaller hole with a needle file. It will work but it isn't the
tightest fit. Any other approaches?
-- Craig (701)
|
| - The Matronics Zenith-List Email Forum - | | Use the List Feature Navigator to browse the many List utilities available such as the Email Subscriptions page, Archive Search & Download, 7-Day Browse, Chat, FAQ, Photoshare, and much more:
http://www.matronics.com/Navigator?Zenith-List |
|
|
|
Back to top |
|
 |
craig(at)craigandjean.com Guest
|
Posted: Sat May 30, 2009 12:08 pm Post subject: Cutting holes with one or more flat sides |
|
|
Thanks, that is essentially what I did for the ignition switch. It won't
rotate but there is some slop. For the smaller parts it will be more
challenging.
-- Craig
--
| - The Matronics Zenith-List Email Forum - | | Use the List Feature Navigator to browse the many List utilities available such as the Email Subscriptions page, Archive Search & Download, 7-Day Browse, Chat, FAQ, Photoshare, and much more:
http://www.matronics.com/Navigator?Zenith-List |
|
|
|
Back to top |
|
 |
Ron Lendon
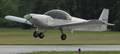
Joined: 10 Jan 2006 Posts: 685 Location: Clinton Twp., MI
|
Posted: Sat May 30, 2009 4:51 pm Post subject: Re: Cutting holes with one or more flat sides |
|
|
The method Paul refers to is the way to go. I call it making a template. It needs to be accurate, but as a template it can be remade or repaired as many times as necessary.
Once the template is right, use it to layout your detail. Now is where skill and patience come into play. Use whatever tools but creep up on the line slowly and DO NOT go past the line. When you get close to the line start test fitting the object. Continue this till you either split the line or the part just slips in.
Hope this helps,
| - The Matronics Zenith-List Email Forum - | | Use the List Feature Navigator to browse the many List utilities available such as the Email Subscriptions page, Archive Search & Download, 7-Day Browse, Chat, FAQ, Photoshare, and much more:
http://www.matronics.com/Navigator?Zenith-List |
|
_________________ Ron Lendon
WW Corvair with Roy's Garage 5th bearing
CH 601 XLB
N601LT - Flying
http://www.mykitlog.com/rlendon
Corvair Engine Prints:
https://sites.google.com/site/corvairenginedata/ |
|
Back to top |
|
 |
|
|
You cannot post new topics in this forum You cannot reply to topics in this forum You cannot edit your posts in this forum You cannot delete your posts in this forum You cannot vote in polls in this forum You cannot attach files in this forum You can download files in this forum
|
Powered by phpBB © 2001, 2005 phpBB Group
|