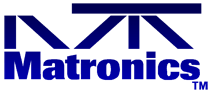 |
Matronics Email Lists Web Forum Interface to the Matronics Email Lists
|
View previous topic :: View next topic |
Author |
Message |
Fred Klein
Joined: 26 Mar 2012 Posts: 503
|
Posted: Sat Aug 04, 2012 9:06 am Post subject: seals for control surfaces |
|
|
Apropos the recent thread on this topic, I found an old posting by John Lawton which may be enlightening:
[quote]In a message dated 5/9/2007 2:59:30 AM Eastern Daylight Time, europa-list(at)matronics.com (europa-list(at)matronics.com) writes:
Quote: | My understanding is that preventing the air going over the flap, in
cruise, reduces drag, resulting in higher cruise speed, which I have
experienced. I don't have the engineering background to completely
understand what is happening to the wing, in flight. That's why I
depend on the guys on the list to keep me straight. I'm more of a "try
it and see" kinda guy... John's advice is based on the success that
the glider guys have had, sealing the gaps. It seems to have worked on
Baby Blue, as well. Continued testing will tell to what degree of
advantage the seals make. It may very well prove that the extra few
knots is not worth the float upon landing. I won't know until I satisfy
myself that I've explored all the angles (and strip widths)...  |
Hey Jeff, et al,
The concept behind seals is pretty simple. In flight the wing creates a low pressure area on the top and high pressure on the bottom. (Bernoulli at it again) This pressure differential will try to equalize through the gap in the flap area and the hinge line of the ailerons. This is also true to some extent on the rudder hinge line and the trim tabs when they are deflected. This equalization causes drag, a lot of drag. So, the idea behind seals, both flap gap and positive seals on ailerons (and rudder and trim tabs), is to prevent this pressure equalization.
On N245E I used PVC weather-strip to create the flap gap seal. The size will depend on how big your gap is between the leading edge of the flap and the flap closeout when retracted. Choose a foam that is slightly thicker than the widest spot in the gap you have. The XS flap closeout looks as if it were designed to be sealed, given the flat area at the bottom rear of the closeout. If you apply the foam strip to the area where the flap "noses" into the closeout when up it will seal this area for cruise flight, but still allow air to flow over the flap when extended. Use a foam that crushes easily when the flap comes in contact with it. You don't want to use a foam that is too stiff or too thick or else your flaps won't fully retract. PVC weather-strip is soft and pliable and works quite well. It is also fairly UV resistant and is very cheap. It's available at any hardware store in various thicknesses. We've found that open cell foams tend to not last very long due to UV and they don't seal as well as closed cell foams like PVC. I also used weather-strip on the ends of my flaps so that they seal against the side of the fuselage when they are in the up position. According to Bruce Carmichael, renowned Aerodynamicist who wrote a book on drag reduction in homebuilts, the wing root/fuselage junction is another area of high drag on most airplanes. Sealing it up helps, too.
Aileron seals are a bit more tricky to employ. Some folks apply Mylar strips over the hinge lines and think they've sealed their ailerons. This is not true. Mylar is not a seal, but rather is applied to help the boundary flow stay attached over the hinge line. Mylar is also somewhat cosmetic in that it hides the hinge line. At high speeds the Mylar will lift up off the wing due to the pressure equalization, thus negating the effects of any sealing the Mylar might be offering. In some cases the Mylar will "buzz" at high speeds.
For sealing ailerons you need to install what are known as positive seals. These seals go from the leading edge of the aileron to the rear of the closeout. There are commercially available materials for this, including various types of cloth and Teflon tapes. Some folks even use cloth tape along the length of the aileron on the undersurface. This is fine on low speed gliders, but I think at the speeds we fly this method likely creates more drag. Personally, I like parachute cloth for making positive seals. Whatever you use it needs to be zero porosity, i.e., allowing no airflow through the material. Parachute cloth is thin, flexible, zero porosity and fits the bill here perfectly. Here at the 'Possum Werks we use Parachute cloth almost exclusively to fabricate positive seals. (it also helps that we have a parachute manufacturer a few miles down the road that gives us their scraps)
First remove the aileron. Then, cut a strip of parachute cloth about 3" wide exactly the length of the aileron. The width you use might take some trial and error to get it right. You don't want it so wide the the material bunches up when the aileron is deflected. 2.5' to 3" width should work on most Europas. Then, yellow contact cement is applied to the leading edge of the aileron, the rear of the closeout and the mating surfaces of the cloth. We use a brand of glue called Plio-bond. It's handy in that it comes in a small bottle with a brush applicator. 3M also makes good contact cement if you can find it. Avoid the water based stuff. It is crap.
Scuff the area to be glued with 180 to enhance the adhesion. Apply the glue in a swath about 3/8" wide to both the seal, the aileron and closeout. Use masking tape to keep your glue line to the prescribed width and remove the tape once the glue is dry. You can also use the masking tape to provide a guide when you scuff the area to be glued, but wipe it with acetone to remove dust before putting the glue on. Allow the glue to dry, usually about 20 minutes, remove the masking tape, then stick the seal to the leading edge of the aileron first, preferably while on your work bench. If you screw something up Xylene will remove the glue easily without harming your paint. The next part takes an extra set of hands.
With one person holding the aileron close to the wing, attach the other half of the cloth to the closeout forming an "S" pattern. Avoid wrinkles. See this drawing for details: http://wingsandwheels.com/page28.htm
Then, reattach the aileron as you would normally do. Check the throw and make sure you are not binding! If you apply the seal correctly you will not even know it is there. I have also sealed my rudder in a similar fashion as well as the trim tabs. They create similar drag when deflected.
I can't say specifically what improvements have occurred in N245E as a result of the seals since I've not ever flown it without them. I can tell you that I exceed Europas published numbers with a fixed pitch prop. I can also tell you that on gliders we generally see 2 to 4 points increase in glide and a noticeable decrease in sink rate, even on the old "woodies", after the application of seals. In power planes this translates to faster cruise, better climb rates and better fuel economy.
Anyway, hope it helps!
Regards,
John Lawton
[b]
| - The Matronics Europa-List Email Forum - | | Use the List Feature Navigator to browse the many List utilities available such as the Email Subscriptions page, Archive Search & Download, 7-Day Browse, Chat, FAQ, Photoshare, and much more:
http://www.matronics.com/Navigator?Europa-List |
|
|
|
Back to top |
|
 |
rlborger(at)mac.com Guest
|
Posted: Sat Aug 04, 2012 9:52 am Post subject: seals for control surfaces |
|
|
Fred,
Thanks for digging this up. Very informative. Now, if I could just get my 914 running right…
Blue skies & tailwinds,
Bob Borger
Europa XS Tri, Rotax 914, Airmaster C/S Prop.
Little Toot Sport Biplane, Lycoming Thunderbolt AEIO-320 EXP
3705 Lynchburg Dr.
Corinth, TX 76208-5331
Cel: 817-992-1117
rlborger(at)mac.com (rlborger(at)mac.com)
On Aug 4, 2012, at 12:03 PM, Fred Klein <fklein(at)orcasonline.com (fklein(at)orcasonline.com)> wrote:
Apropos the recent thread on this topic, I found an old posting by John Lawton which may be enlightening:
Quote: | In a message dated 5/9/2007 2:59:30 AM Eastern Daylight Time, europa-list(at)matronics.com (europa-list(at)matronics.com) writes:
Quote: | My understanding is that preventing the air going over the flap, in
cruise, reduces drag, resulting in higher cruise speed, which I have
experienced. I don't have the engineering background to completely
understand what is happening to the wing, in flight. That's why I
depend on the guys on the list to keep me straight. I'm more of a "try
it and see" kinda guy... John's advice is based on the success that
the glider guys have had, sealing the gaps. It seems to have worked on
Baby Blue, as well. Continued testing will tell to what degree of
advantage the seals make. It may very well prove that the extra few
knots is not worth the float upon landing. I won't know until I satisfy
myself that I've explored all the angles (and strip widths)...  |
Hey Jeff, et al,
The concept behind seals is pretty simple. In flight the wing creates a low pressure area on the top and high pressure on the bottom. (Bernoulli at it again) This pressure differential will try to equalize through the gap in the flap area and the hinge line of the ailerons. This is also true to some extent on the rudder hinge line and the trim tabs when they are deflected. This equalization causes drag, a lot of drag. So, the idea behind seals, both flap gap and positive seals on ailerons (and rudder and trim tabs), is to prevent this pressure equalization.
On N245E I used PVC weather-strip to create the flap gap seal. The size will depend on how big your gap is between the leading edge of the flap and the flap closeout when retracted. Choose a foam that is slightly thicker than the widest spot in the gap you have. The XS flap closeout looks as if it were designed to be sealed, given the flat area at the bottom rear of the closeout. If you apply the foam strip to the area where the flap "noses" into the closeout when up it will seal this area for cruise flight, but still allow air to flow over the flap when extended. Use a foam that crushes easily when the flap comes in contact with it. You don't want to use a foam that is too stiff or too thick or else your flaps won't fully retract. PVC weather-strip is soft and pliable and works quite well. It is also fairly UV resistant and is very cheap. It's available at any hardware store in various thicknesses. We've found that open cell foams tend to not last very long due to UV and they don't seal as well as closed cell foams like PVC. I also used weather-strip on the ends of my flaps so that they seal against the side of the fuselage when they are in the up position. According to Bruce Carmichael, renowned Aerodynamicist who wrote a book on drag reduction in homebuilts, the wing root/fuselage junction is another area of high drag on most airplanes. Sealing it up helps, too.
Aileron seals are a bit more tricky to employ. Some folks apply Mylar strips over the hinge lines and think they've sealed their ailerons. This is not true. Mylar is not a seal, but rather is applied to help the boundary flow stay attached over the hinge line. Mylar is also somewhat cosmetic in that it hides the hinge line. At high speeds the Mylar will lift up off the wing due to the pressure equalization, thus negating the effects of any sealing the Mylar might be offering. In some cases the Mylar will "buzz" at high speeds.
For sealing ailerons you need to install what are known as positive seals. These seals go from the leading edge of the aileron to the rear of the closeout. There are commercially available materials for this, including various types of cloth and Teflon tapes. Some folks even use cloth tape along the length of the aileron on the undersurface. This is fine on low speed gliders, but I think at the speeds we fly this method likely creates more drag. Personally, I like parachute cloth for making positive seals. Whatever you use it needs to be zero porosity, i.e., allowing no airflow through the material. Parachute cloth is thin, flexible, zero porosity and fits the bill here perfectly. Here at the 'Possum Werks we use Parachute cloth almost exclusively to fabricate positive seals. (it also helps that we have a parachute manufacturer a few miles down the road that gives us their scraps)
First remove the aileron. Then, cut a strip of parachute cloth about 3" wide exactly the length of the aileron. The width you use might take some trial and error to get it right. You don't want it so wide the the material bunches up when the aileron is deflected. 2.5' to 3" width should work on most Europas. Then, yellow contact cement is applied to the leading edge of the aileron, the rear of the closeout and the mating surfaces of the cloth. We use a brand of glue called Plio-bond. It's handy in that it comes in a small bottle with a brush applicator. 3M also makes good contact cement if you can find it. Avoid the water based stuff. It is crap.
Scuff the area to be glued with 180 to enhance the adhesion. Apply the glue in a swath about 3/8" wide to both the seal, the aileron and closeout. Use masking tape to keep your glue line to the prescribed width and remove the tape once the glue is dry. You can also use the masking tape to provide a guide when you scuff the area to be glued, but wipe it with acetone to remove dust before putting the glue on. Allow the glue to dry, usually about 20 minutes, remove the masking tape, then stick the seal to the leading edge of the aileron first, preferably while on your work bench. If you screw something up Xylene will remove the glue easily without harming your paint. The next part takes an extra set of hands.
With one person holding the aileron close to the wing, attach the other half of the cloth to the closeout forming an "S" pattern. Avoid wrinkles. See this drawing for details: http://wingsandwheels.com/page28.htm
Then, reattach the aileron as you would normally do. Check the throw and make sure you are not binding! If you apply the seal correctly you will not even know it is there. I have also sealed my rudder in a similar fashion as well as the trim tabs. They create similar drag when deflected.
I can't say specifically what improvements have occurred in N245E as a result of the seals since I've not ever flown it without them. I can tell you that I exceed Europas published numbers with a fixed pitch prop. I can also tell you that on gliders we generally see 2 to 4 points increase in glide and a noticeable decrease in sink rate, even on the old "woodies", after the application of seals. In power planes this translates to faster cruise, better climb rates and better fuel economy.
Anyway, hope it helps!
Regards,
John Lawton
href="http://www.matronics.com/Navigator?Europa-List">http://www.matronics.com/Navigator?Europa-List
href="http://forums.matronics.com/">http://forums.matronics.com
href="http://www.matronics.com/contribution">http://www.matronics.com/contribution
|
| - The Matronics Europa-List Email Forum - | | Use the List Feature Navigator to browse the many List utilities available such as the Email Subscriptions page, Archive Search & Download, 7-Day Browse, Chat, FAQ, Photoshare, and much more:
http://www.matronics.com/Navigator?Europa-List |
|
|
|
Back to top |
|
 |
craigb(at)onthenet.com.au Guest
|
Posted: Sun Aug 05, 2012 1:13 am Post subject: seals for control surfaces |
|
|
While the subject of seals has veered into the subject of Drag, has anyone considered converting the outrigger hinge into a wing fence to help stop spanwise
Flow and thus induced drag in this area. Most of us use the speed kit fairings to reduce drag, surely extending this fairing forward just short of the leading edge and nicely blending it would improve the rather abrupt protrusion of the fairing now and help to stop spanwise flow at the same time.
Just a thought
Regards
Craig
Do Not Archive
[quote][b]
| - The Matronics Europa-List Email Forum - | | Use the List Feature Navigator to browse the many List utilities available such as the Email Subscriptions page, Archive Search & Download, 7-Day Browse, Chat, FAQ, Photoshare, and much more:
http://www.matronics.com/Navigator?Europa-List |
|
|
|
Back to top |
|
 |
grahamsingleton(at)btinte Guest
|
Posted: Sun Aug 05, 2012 1:51 am Post subject: seals for control surfaces |
|
|
Craig
I don't think it would. First it would tend to disrupt the laminar flow on the first 40% of the wing and that would increase it.
Laminar flow is just as important under the wing as on top imho.
Graham
From: craig <craigb(at)onthenet.com.au>
To: europa-list(at)matronics.com
Sent: Sunday, 5 August 2012, 10:13
Subject: RE: seals for control surfaces
While the subject of seals has veered into the subject of Drag, has anyone considered converting the outrigger hinge into a wing fence to help stop spanwise
Flow and thus induced drag in this area. Most of us use the speed kit fairings to reduce drag, surely extending this fairing forward just short of the leading edge and nicely blending it would improve the rather abrupt protrusion of the fairing now and help to stop spanwise flow at the same time.
Just a thought
Regards
Craig
Do Not Archive
[quote]ht; http://www.matronics.com/contrib===============
[b]
| - The Matronics Europa-List Email Forum - | | Use the List Feature Navigator to browse the many List utilities available such as the Email Subscriptions page, Archive Search & Download, 7-Day Browse, Chat, FAQ, Photoshare, and much more:
http://www.matronics.com/Navigator?Europa-List |
|
|
|
Back to top |
|
 |
grahamsingleton(at)btinte Guest
|
Posted: Sun Aug 05, 2012 3:03 am Post subject: seals for control surfaces |
|
|
Well spotted Fred! What John says makes sense to me
Graham
From: Fred Klein <fklein(at)orcasonline.com>
To: europa-list(at)matronics.com
Sent: Saturday, 4 August 2012, 18:03
Subject: seals for control surfaces
Apropos the recent thread on this topic, I found an old posting by John Lawton which may be enlightening:
[quote]In a message dated 5/9/2007 2:59:30 AM Eastern Daylight Time, europa-list(at)matronics.com (europa-list(at)matronics.com) writes:
Quote: | My understanding is that preventing the air going over the flap, in
cruise, reduces drag, resulting in higher cruise speed, which I have
experienced. I don't have the engineering background to completely
understand what is happening to the wing, in flight. That's why I
depend on the guys on the list to keep me straight. I'm more of a "try
it and see" kinda guy... John's advice is based on the success that
the glider guys have had, sealing the gaps. It seems to have worked on
Baby Blue, as well. Continued testing will tell to what degree of
advantage the seals make. It may very well prove that the extra few
knots is not worth the float upon landing. I won't know until I satisfy
myself that I've explored all the angles (and strip widths)...  |
Hey Jeff, et al,
The concept behind seals is pretty simple. In flight the wing creates a low pressure area on the top and high pressure on the bottom. (Bernoulli at it again) This pressure differential will try to equalize through the gap in the flap area and the hinge line of the ailerons. This is also true to some extent on the rudder hinge line and the trim tabs when they are deflected. This equalization causes drag, a lot of drag. So, the idea behind seals, both flap gap and positive seals on ailerons (and rudder and trim tabs), is to prevent this pressure equalization.
On N245E I used PVC weather-strip to create the flap gap seal. The size will depend on how big your gap is between the leading edge of the flap and the flap closeout when retracted. Choose a foam that is slightly thicker than the widest spot in the gap you have. The XS flap closeout looks as if it were designed to be sealed, given the flat area at the bottom rear of the closeout. If you apply the foam strip to the area where the flap "noses" into the closeout when up it will seal this area for cruise flight, but still allow air to flow over the flap when extended. Use a foam that crushes easily when the flap comes in contact with it. You don't want to use a foam that is too stiff or too thick or else your flaps won't fully retract. PVC weather-strip is soft and pliable and works quite well. It is also fairly UV resistant and is very cheap. It's available at any hardware store in various thicknesses. We've found that open cell foams tend to not last very long due to UV and they don't seal as well as closed cell foams like PVC. I also used weather-strip on the ends of my flaps so that they seal against the side of the fuselage when they are in the up position. According to Bruce Carmichael, renowned Aerodynamicist who wrote a book on drag reduction in homebuilts, the wing root/fuselage junction is another area of high drag on most airplanes. Sealing it up helps, too.
Aileron seals are a bit more tricky to employ. Some folks apply Mylar strips over the hinge lines and think they've sealed their ailerons. This is not true. Mylar is not a seal, but rather is applied to help the boundary flow stay attached over the hinge line. Mylar is also somewhat cosmetic in that it hides the hinge line. At high speeds the Mylar will lift up off the wing due to the pressure equalization, thus negating the effects of any sealing the Mylar might be offering. In some cases the Mylar will "buzz" at high speeds.
For sealing ailerons you need to install what are known as positive seals. These seals go from the leading edge of the aileron to the rear of the closeout. There are commercially available materials for this, including various types of cloth and Teflon tapes. Some folks even use cloth tape along the length of the aileron on the undersurface. This is fine on low speed gliders, but I think at the speeds we fly this method likely creates more drag. Personally, I like parachute cloth for making positive seals. Whatever you use it needs to be zero porosity, i.e., allowing no airflow through the material. Parachute cloth is thin, flexible, zero porosity and fits the bill here perfectly. Here at the 'Possum Werks we use Parachute cloth almost exclusively to fabricate positive seals. (it also helps that we have a parachute manufacturer a few miles down the road that gives us their scraps)
First remove the aileron. Then, cut a strip of parachute cloth about 3" wide exactly the length of the aileron. The width you use might take some trial and error to get it right. You don't want it so wide the the material bunches up when the aileron is deflected. 2.5' to 3" width should work on most Europas. Then, yellow contact cement is applied to the leading edge of the aileron, the rear of the closeout and the mating surfaces of the cloth. We use a brand of glue called Plio-bond. It's handy in that it comes in a small bottle with a brush applicator. 3M also makes good contact cement if you can find it. Avoid the water based stuff. It is crap.
Scuff the area to be glued with 180 to enhance the adhesion. Apply the glue in a swath about 3/8" wide to both the seal, the aileron and closeout. Use masking tape to keep your glue line to the prescribed width and remove the tape once the glue is dry. You can also use the masking tape to provide a guide when you scuff the area to be glued, but wipe it with acetone to remove dust before putting the glue on. Allow the glue to dry, usually about 20 minutes, remove the masking tape, then stick the seal to the leading edge of the aileron first, preferably while on your work bench. If you screw something up Xylene will remove the glue easily without harming your paint. The next part takes an extra set of hands.
With one person holding the aileron close to the wing, attach the other half of the cloth to the closeout forming an "S" pattern. Avoid wrinkles. See this drawing for details: http://wingsandwheels.com/page28.htm
Then, reattach the aileron as you would normally do. Check the throw and make sure you are not binding! If you apply the seal correctly you will not even know it is there. I have also sealed my rudder in a similar fashion as well as the trim tabs. They create similar drag when deflected.
I can't say specifically what improvements have occurred in N245E as a result of the seals since I've not ever flown it without them. I can tell you that I exceed Europas published numbers with a fixed pitch prop. I can also tell you that on gliders we generally see 2 to 4 points increase in glide and a noticeable decrease in sink rate, even on the old "woodies", after the application of seals. In power planes this translates to faster cruise, better climb rates and better fuel economy.
Anyway, hope it helps!
Regards,
John Lawton
http://www="nofollow" target="_blank" href="http://forums.matronics.com/">http:/www.matronics.com/contribution">http://www.matronics.com/contribution============
[b]
| - The Matronics Europa-List Email Forum - | | Use the List Feature Navigator to browse the many List utilities available such as the Email Subscriptions page, Archive Search & Download, 7-Day Browse, Chat, FAQ, Photoshare, and much more:
http://www.matronics.com/Navigator?Europa-List |
|
|
|
Back to top |
|
 |
frans(at)privatepilots.nl Guest
|
Posted: Mon Aug 06, 2012 1:50 am Post subject: seals for control surfaces |
|
|
On 08/04/2012 07:03 PM, Fred Klein wrote:
Quote: | Apropos the recent thread on this topic, I found an old posting by John
Lawton which may be enlightening:
|
Thanks Fred!
Quote: | > and the trim tabs when they are deflected. This equalization causes
> drag, a lot of drag. So, the idea behind seals, both flap gap and
> positive seals on ailerons (and rudder and trim tabs), is to prevent
> this pressure equalization.
|
I never understood why these seals are not standard on the Europa. I
have seen them on other brands of homebuilts. Not only do they enhance
the performance, but they are also esthetically more attractive than
just a (often uneven) gap or a hinge line.
Quote: | > On N245E I used PVC weather-strip to create the flap gap seal. The
> size will depend on how big your gap is between the leading edge of
> the flap and the flap closeout when retracted. Choose a foam that is
> slightly thicker than the widest spot in the gap you have. The XS flap
> closeout looks as if it were designed to be sealed, given the flat
> area at the bottom rear of the closeout.
|
How much air is going to this gap with the flaps extended? Is it
possible to make the underside of the wing flush with the flaps when the
flaps are retracted? This would reduce the size of the gap with the
flaps extended, does this have consequences?
Quote: | > According to Bruce Carmichael, renowned Aerodynamicist who wrote a
> book on drag reduction in homebuilts, the wing root/fuselage
> junction is another area of high drag on most airplanes. Sealing it
> up helps, too.
|
Especially on the Europa, where both the wing and fuselage have a very
low pressure area at the same datum, the only good solution is to fill
in this area, like with Fred Klein's wing root fairings.
Another important thing here is to seal the doors properly. Otherwise
the suction will cause the doors to bulge out, releasing massive amounts
of turbulent air.
Quote: | > Aileron seals are a bit more tricky to employ. Some folks apply Mylar
> strips over the hinge lines and think they've sealed their ailerons.
> This /is not/ true. Mylar /is not/ a seal, but rather is applied to
> help the boundary flow stay attached over the hinge line. Mylar is
> also somewhat cosmetic in that it hides the hinge line. At high speeds
> the Mylar will lift up off the wing due to the pressure equalization,
|
What if you seal both surfaces of the ailerons? The seal where the
highest pressure is (most likely the one at the underside of the wing)
will be pushed snug against the surface, blocking any leakage.
I have seals on the flaps and aileron and haven't observed any lifting
of the seals during flight.
Quote: | > For sealing ailerons you need to install what are known as positive
> seals. These seals go from the leading edge of the aileron to the rear
> of the closeout.
|
I find this a bit tricky. I can imagine that with such seals, inside the
closeout, can deform, get loose, wrap up, bulge out, and somehow jam the
ailerons. With standard Mylar seals applied on the outside you can't
think of any serious failure. If they get loose, they will just fly away.
Quote: | > In power planes
> this translates to faster cruise, better climb rates and better fuel
> economy.
|
I think many of us have invested more time and money for less
performance gain...
Frans
| - The Matronics Europa-List Email Forum - | | Use the List Feature Navigator to browse the many List utilities available such as the Email Subscriptions page, Archive Search & Download, 7-Day Browse, Chat, FAQ, Photoshare, and much more:
http://www.matronics.com/Navigator?Europa-List |
|
|
|
Back to top |
|
 |
Fred Klein
Joined: 26 Mar 2012 Posts: 503
|
Posted: Mon Aug 06, 2012 6:19 am Post subject: seals for control surfaces |
|
|
Frans...see indented comments below...Fred
On Aug 6, 2012, at 3:42 AM, Frans Veldman wrote:
Quote: | How much air is going to this gap with the flaps extended? Is it
possible to make the underside of the wing flush with the flaps when the
flaps are retracted? |
..."possible"...but not necessarily desireable...this type of gap seal was installed on Cessna 180s with decidedly mixed results...though it was a factory engineered mod which (presumably) thru testing showed benefits, many Cessna owners have faulted them as the source of nasty manners during landings & takeoffs...I found a current thread on the subject w/ the help of Mr. Google, and by chance had a lengthy conversation w/ a 180 owner this weekend who is very happy that he removed them.
Quote: | This would reduce the size of the gap with the flaps extended, does this have consequences?
|
I would think so, and not necessarily positive. I'd classify the Europa flap as a "slotted flap" which is generally designed to allow substantial airflow thru the slot which I believe is intended to promote the attachment of the boundary layer to the upper surface of the flap...a good thing, no?
I would think that if the compressible flap gap seal which John Lawton recommends was sliced from a circular rod of closed cell foam (known as "backer rod" and used in the US for sealing the joint between concrete and the sill plate of a wood wall) would have minimal disruption of airflow thru the slot.
As you can read from my use of terms that I have only a fuzzy awareness of this stuff, so take my comments with a grain of salt.
Fred
[quote][b]
| - The Matronics Europa-List Email Forum - | | Use the List Feature Navigator to browse the many List utilities available such as the Email Subscriptions page, Archive Search & Download, 7-Day Browse, Chat, FAQ, Photoshare, and much more:
http://www.matronics.com/Navigator?Europa-List |
|
|
|
Back to top |
|
 |
frans(at)privatepilots.nl Guest
|
Posted: Mon Aug 06, 2012 12:06 pm Post subject: seals for control surfaces |
|
|
On 08/06/2012 04:18 PM, Fred Klein wrote:
Quote: | > How much air is going to this gap with the flaps extended? Is it
> possible to make the underside of the wing flush with the flaps when the
> flaps are retracted?
..."possible"...but not necessarily desireable...this type of gap seal
was installed on Cessna 180s with decidedly mixed results...
|
I know it was an option on Cessna's but I didn't know about the mixed
results.
Quote: | > This would reduce the size of the gap with the flaps extended, does
> this have consequences?
I would think so, and not necessarily positive. I'd classify the Europa
flap as a "slotted flap" which is generally designed to allow
substantial airflow thru the slot which I believe is intended to promote
the attachment of the boundary layer to the upper surface of the
flap...a good thing, no?
|
Yes. But the current slot is a 90 degree corner, and apperently you can
also put cell foam in it as a seal. Id doesn't look like it allows lot
of air through. That's why I wondered whether some "lip" at the bottom
of this slot would make things different.
Quote: | I would think that if the compressible flap gap seal which John Lawton
recommends was sliced from a circular rod of closed cell foam (known as
"backer rod" and used in the US for sealing the joint between concrete
and the sill plate of a wood wall) would have minimal disruption of
airflow thru the slot.
|
Yes, but he mentions in the email that "the XS-wing looks like it has
been designed with a seal in mind, because it has a flat area at the
bottom of the slot." But at the bottom of the slot the gap is at its
widest point, far too wide for a foam seal. So I'm a bit confused here
as what he means.
Quote: | As you can read from my use of terms that I have only a fuzzy awareness
of this stuff, so take my comments with a grain of salt.
|
Same here. I hope to find someone who can shed some more light onto this
matter.
Frans
| - The Matronics Europa-List Email Forum - | | Use the List Feature Navigator to browse the many List utilities available such as the Email Subscriptions page, Archive Search & Download, 7-Day Browse, Chat, FAQ, Photoshare, and much more:
http://www.matronics.com/Navigator?Europa-List |
|
|
|
Back to top |
|
 |
klinefelter.kevin(at)gmai Guest
|
Posted: Mon Aug 06, 2012 6:06 pm Post subject: seals for control surfaces |
|
|
Frans, I think he means put the foam PVC weatherstrip about where the gap between the forward most part of the retracted flap and the closeout is. So when the flap is retracted, the "leading edge" of the flap just touches and even compresses the foam. This should help keep the higher pressure air under the wing from going up top.
So there is no "lip" at the bottom of the slot, the foam strip is attached up the closeout a bit where the space between the leading edge of the flap and the closeout is smallest. I have been flying my Mono this way for quite a while now and have not noticed any negative effects.
So the objective here is to keep the higher pressure air down where it belongs, not to "smooth out" the gap between the lower wing and flap bottom surface.
I think if you attached a Mylar strip to the bottom of the wing to span the gap to the flap, it would screw up the air flow thru the "slot" when the flap is down, making our slotted flaps less effective... I think.
Kevin
On Aug 6, 2012, at 1:58 PM, Frans Veldman <frans(at)privatepilots.nl> wrote:
Quote: |
On 08/06/2012 04:18 PM, Fred Klein wrote:
>> How much air is going to this gap with the flaps extended? Is it
>> possible to make the underside of the wing flush with the flaps when the
>> flaps are retracted?
>
> ..."possible"...but not necessarily desireable...this type of gap seal
> was installed on Cessna 180s with decidedly mixed results...
I know it was an option on Cessna's but I didn't know about the mixed
results.
>> This would reduce the size of the gap with the flaps extended, does
>> this have consequences?
>
> I would think so, and not necessarily positive. I'd classify the Europa
> flap as a "slotted flap" which is generally designed to allow
> substantial airflow thru the slot which I believe is intended to promote
> the attachment of the boundary layer to the upper surface of the
> flap...a good thing, no?
Yes. But the current slot is a 90 degree corner, and apperently you can
also put cell foam in it as a seal. Id doesn't look like it allows lot
of air through. That's why I wondered whether some "lip" at the bottom
of this slot would make things different.
> I would think that if the compressible flap gap seal which John Lawton
> recommends was sliced from a circular rod of closed cell foam (known as
> "backer rod" and used in the US for sealing the joint between concrete
> and the sill plate of a wood wall) would have minimal disruption of
> airflow thru the slot.
Yes, but he mentions in the email that "the XS-wing looks like it has
been designed with a seal in mind, because it has a flat area at the
bottom of the slot." But at the bottom of the slot the gap is at its
widest point, far too wide for a foam seal. So I'm a bit confused here
as what he means.
> As you can read from my use of terms that I have only a fuzzy awareness
> of this stuff, so take my comments with a grain of salt.
Same here. I hope to find someone who can shed some more light onto this
matter.
Frans
|
| - The Matronics Europa-List Email Forum - | | Use the List Feature Navigator to browse the many List utilities available such as the Email Subscriptions page, Archive Search & Download, 7-Day Browse, Chat, FAQ, Photoshare, and much more:
http://www.matronics.com/Navigator?Europa-List |
|
|
|
Back to top |
|
 |
Fred Klein
Joined: 26 Mar 2012 Posts: 503
|
Posted: Mon Aug 06, 2012 6:12 pm Post subject: seals for control surfaces |
|
|
Frans...indented comments below...Fred
On Aug 6, 2012, at 1:58 PM, Frans Veldman wrote:
Quote: | --> Europa-List message posted by: Frans Veldman <frans(at)privatepilots.nl (frans(at)privatepilots.nl)>
On 08/06/2012 04:18 PM, Fred Klein wrote:
Quote: | Quote: | How much air is going to this gap with the flaps extended? Is it
|
Quote: | possible to make the underside of the wing flush with the flaps when the
|
Quote: | flaps are retracted?
|
..."possible"...but not necessarily desireable...this type of gap seal
was installed on Cessna 180s with decidedly mixed results...
|
I know it was an option on Cessna's but I didn't know about the mixed
results.
Quote: | Quote: | This would reduce the size of the gap with the flaps extended, does
|
Quote: | this have consequences?
|
I would think so, and not necessarily positive. I'd classify the Europa
flap as a "slotted flap" which is generally designed to allow
substantial airflow thru the slot which I believe is intended to promote
the attachment of the boundary layer to the upper surface of the
flap...a good thing, no?
|
Yes. But the current slot is a 90 degree corner,
|
true enough...but I measure the radius of the corner of the closeout at about 3/8" and the radius of the forward portion of the lower surface of the flap at approximately 3/4" which invite the air to flow up thru the slot...
Quote: | and apperently you can also put cell foam in it as a seal. Id doesn't look like it allows lot of air through.
|
well...I guess "a lot" depends upon one's point of view...recognise that the air is flowing from high pressure / low velocity to low pressure / high velocity so I'd say that a lot of air is being sucked up into the gap and blown out the rear across the top surface of the flap.
Quote: | That's why I wondered whether some "lip" at the bottom
of this slot would make things different.
|
On my plane, such a "lip"...if it is intended to provide a smooth, continuous bridge over the gap between flap and wing when flap is retracted...would have to be between 1.5" and 2" wide, and stiff enough so that it would not just get sucked up into the gap the first time the flaps are deployed...and if it were sufficiently stiff, it would seem to me that at that width it would seriously degrade the air flow thru the slot w/ flap deployed.
Quote: |
Quote: | I would think that if the compressible flap gap seal which John Lawton
recommends was sliced from a circular rod of closed cell foam (known as
"backer rod" and used in the US for sealing the joint between concrete
and the sill plate of a wood wall) would have minimal disruption of
airflow thru the slot.
|
Yes, but he mentions in the email that "the XS-wing looks like it has
been designed with a seal in mind, because it has a flat area at the
bottom of the slot."
|
Lawton wrote:
The XS flap closeout looks as if it were designed to be sealed, given the flat area at the bottom rear of the closeout. If you apply the foam strip to the area where the flap "noses" into the closeout when up it will seal this area for cruise flight, but still allow air to flow over the flap when extended.
Notice that John does not advocate placing the compressible foam seal at the lowermost portion of the flat area but rather "where the flap 'noses' into the closeout" when flap is in the retracted position; on my plane, this location is about 1" up from the lower.surface of the wing. This location, at least on my plane, is the place where the "slot" is narrowest when the flap is retracted, and widest when the flap is deployed. Thus the location is optimal for using the thinnest seal w/ minimal interference of air flow when flap is deployed. I plan to use3/8" diameter backer rod sliced in half.
Quote: | But at the bottom of the slot the gap is at its widest point, far too wide for a foam seal. So I'm a bit confused here
as what he means.
|
When John wrote "bottom of the slot", I did not infer that he intended the literally lowest point of the slot but rather the portion of the closeout which is flat and vertical.
Indeed, gap at the literal "bottom of the slot" which would include the radii of the closeout and the forwardmost portion of the lower surface of the flat on my plane would require that 1.5" to 2" wide "lip".
Quote: | Quote: | As you can read from my use of terms that I have only a fuzzy awareness
of this stuff, so take my comments with a grain of salt.
|
Same here. I hope to find someone who can shed some more light onto this
matter.
|
Piry we don't have a resident aerodynamicist to keep us luftmensch in chek,
Fred
[quote][b]
| - The Matronics Europa-List Email Forum - | | Use the List Feature Navigator to browse the many List utilities available such as the Email Subscriptions page, Archive Search & Download, 7-Day Browse, Chat, FAQ, Photoshare, and much more:
http://www.matronics.com/Navigator?Europa-List |
|
|
|
Back to top |
|
 |
grahamsingleton(at)btinte Guest
|
Posted: Mon Aug 06, 2012 10:49 pm Post subject: seals for control surfaces |
|
|
Fred, hopefully Ivan might have an opinion on this, I know he's been away but should be back now. Ivan?
If you look at the definitive digital co ordinates of the section you will see first of all that the bottom surface is not flat but slightly convex,
so there is a slight reflex at the trailing edge. This will have an effect on drag in the cruise. I think it's important to have smooth airflow through the gap
when the flap is deployed to keep airflow attached over the flap. I don't think we need to seal the LE of the flap flap up because we aren't looking for optimum lift
we want minimum drag in any case the pressure top and bottom will be almost equal at this point. The control surfaces are different, here we want more effect without increasing drag.
Graham
From: Fred Klein <fklein(at)orcasonline.com>
To: europa-list(at)matronics.com
Sent: Tuesday, 7 August 2012, 3:11
Subject: Re: Europa-List: seals for control surfaces
Frans...indented comments below...Fred
On Aug 6, 2012, at 1:58 PM, Frans Veldman wrote:
Quote: | --> Europa-List message posted by: Frans Veldman <frans(at)privatepilots.nl (frans(at)privatepilots.nl)>
On 08/06/2012 04:18 PM, Fred Klein wrote:
Quote: | Quote: | How much air is going to this gap with the flaps extended? Is it
|
Quote: | possible to make the underside of the wing flush with the flaps when the
|
Quote: | flaps are retracted?
|
..."possible"...but not necessarily desireable...this type of gap seal
was installed on Cessna 180s with decidedly mixed results...
|
I know it was an option on Cessna's but I didn't know about the mixed
results.
Quote: | Quote: | This would reduce the size of the gap with the flaps extended, does
|
Quote: | this have consequences?
|
I would think so, and not necessarily positive. I'd classify the Europa
flap as a "slotted flap" which is generally designed to allow
substantial airflow thru the slot which I believe is intended to promote
the attachment of the boundary layer to the upper surface of the
flap...a good thing, no?
|
Yes. But the current slot is a 90 degree corner,
|
true enough...but I measure the radius of the corner of the closeout at about 3/8" and the radius of the forward portion of the lower surface of the flap at approximately 3/4" which invite the air to flow up thru the slot...
Quote: | and apperently you can also put cell foam in it as a seal. Id doesn't look like it allows lot of air through.
|
well...I guess "a lot" depends upon one's point of view...recognise that the air is flowing from high pressure / low velocity to low pressure / high velocity so I'd say that a lot of air is being sucked up into the gap and blown out the rear across the top surface of the flap.
Quote: | That's why I wondered whether some "lip" at the bottom
of this slot would make things different.
|
On my plane, such a "lip"...if it is intended to provide a smooth, continuous bridge over the gap between flap and wing when flap is retracted...would have to be between 1.5" and 2" wide, and stiff enough so that it would not just get sucked up into the gap the first time the flaps are deployed...and if it were sufficiently stiff, it would seem to me that at that width it would seriously degrade the air flow thru the slot w/ flap deployed.
Quote: |
Quote: | I would think that if the compressible flap gap seal which John Lawton
recommends was sliced from a circular rod of closed cell foam (known as
"backer rod" and used in the US for sealing the joint between concrete
and the sill plate of a wood wall) would have minimal disruption of
airflow thru the slot.
|
Yes, but he mentions in the email that "the XS-wing looks like it has
been designed with a seal in mind, because it has a flat area at the
bottom of the slot."
|
Lawton wrote:
The XS flap closeout looks as if it were designed to be sealed, given the flat area at the bottom rear of the closeout. If you apply the foam strip to the area where the flap "noses" into the closeout when up it will seal this area for cruise flight, but still allow air to flow over the flap when extended.
Notice that John does not advocate placing the compressible foam seal at the lowermost portion of the flat area but rather "where the flap 'noses' into the closeout" when flap is in the retracted position; on my plane, this location is about 1" up from the lower.surface of the wing. This location, at least on my plane, is the place where the "slot" is narrowest when the flap is retracted, and widest when the flap is deployed. Thus the location is optimal for using the thinnest seal w/ minimal interference of air flow when flap is deployed. I plan to use3/8" diameter backer rod sliced in half.
Quote: | But at the bottom of the slot the gap is at its widest point, far too wide for a foam seal. So I'm a bit confused here
as what he means.
|
When John wrote "bottom of the slot", I did not infer that he intended the literally lowest point of the slot but rather the portion of the closeout which is flat and vertical.
Indeed, gap at the literal "bottom of the slot" which would include the radii of the closeout and the forwardmost portion of the lower surface of the flat on my plane would require that 1.5" to 2" wide "lip".
Quote: | Quote: | As you can read from my use of terms that I have only a fuzzy awareness
of this stuff, so take my comments with a grain of salt.
|
Same here. I hope to find someone who can shed some more light onto this
matter.
|
Piry we don't have a resident aerodynamicist to keep us luftmensch in chek,
Fred
[quote]http://www.matro====================
[b]
| - The Matronics Europa-List Email Forum - | | Use the List Feature Navigator to browse the many List utilities available such as the Email Subscriptions page, Archive Search & Download, 7-Day Browse, Chat, FAQ, Photoshare, and much more:
http://www.matronics.com/Navigator?Europa-List |
|
|
|
Back to top |
|
 |
tennant
Joined: 19 Apr 2011 Posts: 121
|
Posted: Tue Aug 07, 2012 12:24 am Post subject: Re: seals for control surfaces |
|
|
Just my 10c.
I have been flying with mylar seals on the upper flap joints and ailerons for 15 years.
No great float on landing.
No lifting of the seals on the ailerons up to VNE.
No idea if they have improved performance as I have always had them but I measured again on the weekend and have 119 Kts TAS at 16 L/Hr and 124 Kts TAS at 17 L/Hr at 3 - 4000 ft. I have no idea if that is good or bad for a 912 (80HP) classic mono.
Barry
| - The Matronics Europa-List Email Forum - | | Use the List Feature Navigator to browse the many List utilities available such as the Email Subscriptions page, Archive Search & Download, 7-Day Browse, Chat, FAQ, Photoshare, and much more:
http://www.matronics.com/Navigator?Europa-List |
|
_________________ Barry Tennant
D-EHBT
At EDLM - Germany |
|
Back to top |
|
 |
|
|
You cannot post new topics in this forum You cannot reply to topics in this forum You cannot edit your posts in this forum You cannot delete your posts in this forum You cannot vote in polls in this forum You cannot attach files in this forum You can download files in this forum
|
Powered by phpBB © 2001, 2005 phpBB Group
|