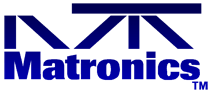 |
Matronics Email Lists Web Forum Interface to the Matronics Email Lists
|
View previous topic :: View next topic |
Author |
Message |
owl40188(at)yahoo.com Guest
|
Posted: Thu Mar 15, 2007 7:36 am Post subject: Axle Extension - Brute Force Method |
|
|
When we had the axle extension group buy I had opted out as the group got very large and I was thinking that we could put another group buy at a later date. These things have a way of sneaking up on you and I ended up working on this part earlier than I had anticipated. Being a bit early for another group buy I brute forced it and got another solution.
I replaced the original 1/2 inch diameter extension and AN4 bolt with a 3/4 inch diameter hex extension and AN6 bolt. I have attached a few pictures for those interested in trying the same modification.
I found the 3/4 inch hex extension at McMasterCarr in 12 inch lengths.
Niko
40188
| - The Matronics RV10-List Email Forum - | | Use the List Feature Navigator to browse the many List utilities available such as the Email Subscriptions page, Archive Search & Download, 7-Day Browse, Chat, FAQ, Photoshare, and much more:
http://www.matronics.com/Navigator?RV10-List |
|
Description: |
|
Filesize: |
197.58 KB |
Viewed: |
273 Time(s) |
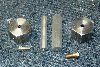
|
Description: |
|
Filesize: |
150.25 KB |
Viewed: |
265 Time(s) |
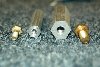
|
Description: |
|
Filesize: |
161.32 KB |
Viewed: |
261 Time(s) |
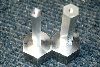
|
|
|
Back to top |
|
 |
indigoonlatigo(at)msn.com Guest
|
Posted: Thu Mar 15, 2007 8:18 am Post subject: Axle Extension - Brute Force Method |
|
|
Tim will tell you, I'll bet that even the AN6 bolt will shear.
The vibration and the fulcrum point of the edge of the hex extension on the
vertical face of the axle mount, cycled thousands and thousands of time will
snap that bolt.
I like to think of this design as the way early dental implants were
designed. The screws used to snap of inside the implant or bend before
snapping.
This is why I love to understand the physics in everything including
dentistry.
John G
Do not archive
Quote: | From: Niko <owl40188(at)yahoo.com>
Reply-To: rv10-list(at)matronics.com
To: Matronics <rv10-list(at)matronics.com>
Subject: Fw: Axle Extension - Brute Force Method
Date: Thu, 15 Mar 2007 08:35:45 -0700 (PDT)
When we had the axle extension group buy I had opted out as the group got
very large and I was thinking that we could put another group buy at a
later date. These things have a way of sneaking up on you and I ended up
working on this part earlier than I had anticipated. Being a bit early for
another group buy I brute forced it and got another solution.
I replaced the original 1/2 inch diameter extension and AN4 bolt with a 3/4
inch diameter hex extension and AN6 bolt. I have attached a few pictures
for those interested in trying the same modification.
I found the 3/4 inch hex extension at McMasterCarr in 12 inch lengths.
Niko
40188
|
Quote: | << AxleExtensionSml1.jpg >>
|
Quote: | << AxleExtensionSml2.jpg >>
|
Quote: | << AxleExtension3Sml.jpg >>
|
| - The Matronics RV10-List Email Forum - | | Use the List Feature Navigator to browse the many List utilities available such as the Email Subscriptions page, Archive Search & Download, 7-Day Browse, Chat, FAQ, Photoshare, and much more:
http://www.matronics.com/Navigator?RV10-List |
|
|
|
Back to top |
|
 |
jesse(at)saintaviation.co Guest
|
Posted: Thu Mar 15, 2007 8:32 am Post subject: Axle Extension - Brute Force Method |
|
|
Looks like a good option also. Thanks for the pics.
Jesse Saint
Saint Aviation, Inc.
jesse(at)saintaviation.com (jesse(at)saintaviation.com)
www.saintaviation.com
Cell: 352-427-0285
Fax: 815-377-3694
From: owner-rv10-list-server(at)matronics.com [mailto:owner-rv10-list-server(at)matronics.com] On Behalf Of Niko
Sent: Thursday, March 15, 2007 11:36 AM
To: Matronics
Subject: Fw: Axle Extension - Brute Force Method
When we had the axle extension group buy I had opted out as the group got very large and I was thinking that we could put another group buy at a later date. These things have a way of sneaking up on you and I ended up working on this part earlier than I had anticipated. Being a bit early for another group buy I brute forced it and got another solution.
I replaced the original 1/2 inch diameter extension and AN4 bolt with a 3/4 inch diameter hex extension and AN6 bolt. I have attached a few pictures for those interested in trying the same modification.
I found the 3/4 inch hex extension at McMasterCarr in 12 inch lengths.
Niko
40188
[quote][b]
| - The Matronics RV10-List Email Forum - | | Use the List Feature Navigator to browse the many List utilities available such as the Email Subscriptions page, Archive Search & Download, 7-Day Browse, Chat, FAQ, Photoshare, and much more:
http://www.matronics.com/Navigator?RV10-List |
|
|
|
Back to top |
|
 |
owl40188(at)yahoo.com Guest
|
Posted: Thu Mar 15, 2007 9:45 am Post subject: Axle Extension - Brute Force Method |
|
|
I am not sure why you are saying this John. An AN6 bolt, has a tensile strength of 10100lb where as an AN4 bolt has a tensile strength of 4000lb. Additionally the larger hex extension reduces the load on the bolt. I haven't done any analysis on this particular design so I can't tell you for sure if the original design was grossly undersized, however, being that not everyone is having problems I would think that Vans design is not that far off. And this design would have less than a third of the stress in the bolt that Vans design has. I guess time will tell.
One item that might be coming into play is the torque values. If one under torques a bolt its fatigue life may be reduced drastically. Thats because the bolt typically sees only a fraction of the applied load as the rest is going to relieve some of the preload in the joint. If the applied load is higher than the preload due to torque the joint will open up and drastically reduce the life of the bolt. Yes, this does mean the higher the torque the better up to the point where significant deformation of the threads occurs. Although this is just a guess it could very well be that the people having problems with Vans design at this location have not applied enough torque. I do realize that the bolt is being threaded into aluminum and one has to be more carefull
Thousands of cycles by themselves are not a problem. In fact even aluminum (2024) can take more than 100 million cycles if you keep the peak stress below 10 ksi.
Niko
40188
---
| - The Matronics RV10-List Email Forum - | | Use the List Feature Navigator to browse the many List utilities available such as the Email Subscriptions page, Archive Search & Download, 7-Day Browse, Chat, FAQ, Photoshare, and much more:
http://www.matronics.com/Navigator?RV10-List |
|
|
|
Back to top |
|
 |
indigoonlatigo(at)msn.com Guest
|
Posted: Thu Mar 15, 2007 11:05 am Post subject: Axle Extension - Brute Force Method |
|
|
First let me state I am not trying to be a know it all or a smart ass. Nor
am I clairvoyant.
Think about how those rocks were moved to build the pyramids. Think about
how after a tornado or hurricane they find a plastic straw embedded in a
telephone pole. How about how a 110 pound Japanese Aikido practitioner can
bring down a 350 pound muscle man with the greatest of ease.
What the hell am I talking about?
Brute force, or as you state, the thickest of metal, not designed well, will
shatter. The problem is that you need to think of the hex extension as a
lever. The fulcrum point is the edge of the hex where it touches the flat
face of the axle adapter. The other lever arm is the distance between the
bolt and the outside edge of the hex extension(in other wards, the distance
between the fulcrum point back to the bolt.) Think of this also in 360
degrees(this is realy bad)
Now you will true your fairing as best you can so it flies cleanly through
the air, but these reciprocating engines, even the Eggenfellner, will cause
a vibration. Translate that vibration on to the wheel fairing and you will
get a harmonic cycle acting on that long lever arm(The hex extension). The
longer the hex extension the worse the problem. The more mass at the end of
that extension, the worse the problem. The more vibration, worse yet.
Millions of cycles possibly over a single flight. In my opinion, that bolt
doesn't stand a chance. No matter how you torque it.
Here is a little better way. Tim's design for one. After that, where the hex
extension meets the axle adapter, you need a female receptor lathed into the
axle adapter. It needs to have a Morse Taper. The Hex extension needs to
have a corresponding Male, Morse taper. The bolt, properly torqued will
transfer the load to the two tapers and relieve the lateral forces which the
bolt's shaft is subjected to. The bolt will now only serve to hold the two
pieces together. The machining needs to be really clean with no internal
blips or hangups, otherwise these will act as fulcrum points.
Damm, you all better hope that my schedule starts getting busy again,
otherwise I'll drive you crazy.
John G. #409
Do archive this. I think this is an appropriate time for a Yoda qoute.
Suggestions?
Wagers anyone????
[quote]From: Niko <owl40188(at)yahoo.com>
Reply-To: rv10-list(at)matronics.com
To: rv10-list(at)matronics.com
Subject: Re: Fw: Axle Extension - Brute Force Method
Date: Thu, 15 Mar 2007 10:43:08 -0700 (PDT)
I am not sure why you are saying this John. An AN6 bolt, has a tensile
strength of 10100lb where as an AN4 bolt has a tensile strength of 4000lb.
Additionally the larger hex extension reduces the load on the bolt. I
haven't done any analysis on this particular design so I can't tell you for
sure if the original design was grossly undersized, however, being that
not everyone is having problems I would think that Vans design is not that
far off. And this design would have less than a third of the stress in the
bolt that Vans design has. I guess time will tell.
One item that might be coming into play is the torque values. If one
under torques a bolt its fatigue life may be reduced drastically. Thats
because the bolt typically sees only a fraction of the applied load as the
rest is going to relieve some of the preload in the joint. If the applied
load is higher than the preload due to torque the joint will open up and
drastically reduce the life of the bolt. Yes, this does mean the higher
the torque the better up to the point where significant deformation of the
threads occurs. Although this is just a guess it could very well be that
the people having problems with Vans design at this location have not
applied enough torque. I do realize that the bolt is being threaded into
aluminum and one has to be more carefull
Thousands of cycles by themselves are not a problem. In fact even
aluminum (2024) can take more than 100 million cycles if you keep the peak
stress below 10 ksi.
Niko
40188
---
| - The Matronics RV10-List Email Forum - | | Use the List Feature Navigator to browse the many List utilities available such as the Email Subscriptions page, Archive Search & Download, 7-Day Browse, Chat, FAQ, Photoshare, and much more:
http://www.matronics.com/Navigator?RV10-List |
|
|
|
Back to top |
|
 |
Rick S.
Joined: 12 Feb 2006 Posts: 347 Location: Las Vegas
|
Posted: Thu Mar 15, 2007 11:27 am Post subject: Axle Extension - Brute Force Method |
|
|
In the time it took to type that response you could have mounted the delron blocks into the door pockets.
Rick S.
40185
do not archive
| - The Matronics RV10-List Email Forum - | | Use the List Feature Navigator to browse the many List utilities available such as the Email Subscriptions page, Archive Search & Download, 7-Day Browse, Chat, FAQ, Photoshare, and much more:
http://www.matronics.com/Navigator?RV10-List |
|
_________________ Rick S.
RV-10
40185 |
|
Back to top |
|
 |
deej(at)deej.net Guest
|
|
Back to top |
|
 |
Tim Olson
Joined: 25 Jan 2007 Posts: 2881
|
Posted: Thu Mar 15, 2007 11:30 am Post subject: Axle Extension - Brute Force Method |
|
|
Personally, I think that what Niko did is going to work great. The
old one had it's weaknesses, and any enlargement or improvement
will help a great deal and likely make it a non-issue. He's going
with a huge bolt, but not quite as much base on the stem, but
relative to what was kit-supplied, he's quite a bit better. The
hex bar may make it easier to rock in one specific direction,
whereas a rounded piece would be like having that width
throughout an infinite number of corners like on the hex. (hard
to explain that one...but I'm basically saying that he's only got
that huge OD on the corners, and it's lesser on the flats)
So, in the end, I don't see that it'll be a big problem if the
originals worked OK for some people for a while. It may
not be quite as strong, or maybe with the larger bolt he may
be as strong. Either way, he's well over what it originally
was so I sure wouldn't lose any sleep over it at this point.
I do agree with you though John, that the fulcrum point is not only
closer to the bolt, but with the flats it can be even more
close than at the hex corners. Is it a big deal? as long a
the piece has some huge-ness, it will help. On those that we
had made, I just went for the widest base, with a thin enough tip
so that it would easily retrofit and work for anyone....and taper
to save weight.
Tim Olson - RV-10 N104CD - Flying
do not archive
Niko wrote:
[quote] I am not sure why you are saying this John. An AN6 bolt, has a tensile
strength of 10100lb where as an AN4 bolt has a tensile strength of
4000lb. Additionally the larger hex extension reduces the load on the
bolt. I haven't done any analysis on this particular design so I can't
tell you for sure if the original design was grossly undersized,
however, being that not everyone is having problems I would think that
Vans design is not that far off. And this design would have less than a
third of the stress in the bolt that Vans design has. I guess time will
tell.
One item that might be coming into play is the torque values. If one
under torques a bolt its fatigue life may be reduced drastically. Thats
because the bolt typically sees only a fraction of the applied load as
the rest is going to relieve some of the preload in the joint. If the
applied load is higher than the preload due to torque the joint will
open up and drastically reduce the life of the bolt. Yes, this does
mean the higher the torque the better up to the point where significant
deformation of the threads occurs. Although this is just a guess it
could very well be that the people having problems with Vans design at
this location have not applied enough torque. I do realize that the
bolt is being threaded into aluminum and one has to be more carefull
Thousands of cycles by themselves are not a problem. In fact even
aluminum (2024) can take more than 100 million cycles if you keep the
peak stress below 10 ksi.
Niko
40188
---
| - The Matronics RV10-List Email Forum - | | Use the List Feature Navigator to browse the many List utilities available such as the Email Subscriptions page, Archive Search & Download, 7-Day Browse, Chat, FAQ, Photoshare, and much more:
http://www.matronics.com/Navigator?RV10-List |
|
|
|
Back to top |
|
 |
indigoonlatigo(at)msn.com Guest
|
Posted: Thu Mar 15, 2007 12:42 pm Post subject: Axle Extension - Brute Force Method |
|
|
Unfortunately I work far away from my plane and when I am not working with
my hands in my job, I often waist time.
Hoping you all don't all feel it was a waist of my time writing it or yours
reading it.
I still counter, hugeness only goes so far. I will hope it lasts until the
time Tim offers another order.
Did anyone visit the GE 1.5MW fan site? Please don't say a waist of time.
Send patients so I shut up.
John G. Do not archive
Quote: | From: Rick <ricksked(at)earthlink.net>
Reply-To: rv10-list(at)matronics.com
To: rv10-list(at)matronics.com
Subject: Re: Fw: Axle Extension - Brute Force Method
Date: Thu, 15 Mar 2007 15:27:13 -0400 (EDT)
In the time it took to type that response you could have mounted the delron
blocks into the door pockets.
Rick S.
40185
do not archive
|
| - The Matronics RV10-List Email Forum - | | Use the List Feature Navigator to browse the many List utilities available such as the Email Subscriptions page, Archive Search & Download, 7-Day Browse, Chat, FAQ, Photoshare, and much more:
http://www.matronics.com/Navigator?RV10-List |
|
|
|
Back to top |
|
 |
Rick S.
Joined: 12 Feb 2006 Posts: 347 Location: Las Vegas
|
|
Back to top |
|
 |
Rick S.
Joined: 12 Feb 2006 Posts: 347 Location: Las Vegas
|
Posted: Thu Mar 15, 2007 12:59 pm Post subject: Axle Extension - Brute Force Method |
|
|
"I still counter, hugeness only goes so far."
So are you saying that size matters or doesn't matter? Or maybe big is good but ya gotta kiss her too?
"Did anyone visit the GE 1.5MW fan site? Please don't say a waist of time".
I agree...not taking advantage of free air is a big "WAIST" which goes back to that hugeness you keep referring too!!
Quitting time for me must be getting punchy...time to go sand, again, and again.
All in fun Doc!!
Rick S.
40185
do not archive
| - The Matronics RV10-List Email Forum - | | Use the List Feature Navigator to browse the many List utilities available such as the Email Subscriptions page, Archive Search & Download, 7-Day Browse, Chat, FAQ, Photoshare, and much more:
http://www.matronics.com/Navigator?RV10-List |
|
_________________ Rick S.
RV-10
40185 |
|
Back to top |
|
 |
indigoonlatigo(at)msn.com Guest
|
Posted: Thu Mar 15, 2007 2:20 pm Post subject: Axle Extension - Brute Force Method |
|
|
Okay Rick,
Well, without tools I can't lift a really fat guy off the ground. Big guys
are better on the front line for blocking and filling in open spaces. In
these cases, hugeness matters, but here is one for you...
"Size matters not, look at me. judge me by size, do you"
As Yoda lifts the RV10(X wing fighter) out of the swamp, Luke says,"I can't
believe it."
Yoda:"That is why you fail"
Basically, don't under estimate the laws of physics or the 'Force'
Remember, shear is different from tensil and compression. I think in this
case, you have all three working on that bolt.
I am leaving work and going for a run. Have fun guys, gals
Dr. G
Quote: | From: Rick <ricksked(at)earthlink.net>
Reply-To: rv10-list(at)matronics.com
To: rv10-list(at)matronics.com
Subject: Re: Fw: Axle Extension - Brute Force Method
Date: Thu, 15 Mar 2007 16:59:03 -0400 (EDT)
"I still counter, hugeness only goes so far."
So are you saying that size matters or doesn't matter? Or maybe big is good
but ya gotta kiss her too?
"Did anyone visit the GE 1.5MW fan site? Please don't say a waist of time".
I agree...not taking advantage of free air is a big "WAIST" which goes back
to that hugeness you keep referring too!!
Quitting time for me must be getting punchy...time to go sand, again,
and again.
All in fun Doc!!
Rick S.
40185
do not archive
|
| - The Matronics RV10-List Email Forum - | | Use the List Feature Navigator to browse the many List utilities available such as the Email Subscriptions page, Archive Search & Download, 7-Day Browse, Chat, FAQ, Photoshare, and much more:
http://www.matronics.com/Navigator?RV10-List |
|
|
|
Back to top |
|
 |
owl40188(at)yahoo.com Guest
|
Posted: Thu Mar 15, 2007 2:26 pm Post subject: Axle Extension - Brute Force Method |
|
|
Well John, I don't think you are being a smart ass and you have not offended me in any way. I am just writing this for an informational point of view as I have gotten a lot of usefull information from this group and I am trying to give back a little.
There is a big difference between a "poor" design and margin of safety. A poor structural design simply means its inefficient in carrying loads it does not mean that it will fail. The RV10s, small Cessnas, and small Pipers are filled with design details which are considered "poor" because they are structurally inefficient but they have adequate margins of safety and they work. They are just heavy but they are simple cheap methods of doing a task and frankly I believe in most cases appropriate for the aircraft they are being used in.
The current axle extension design that Van's has is not a bad design its simply a bit undersized. It works in heel-toe action what you are calling a fulcrum. This is not a mystical design. The load on the bolt for a given configuration can be easily calculated and sized appropriately. By the way this same concept is being used to carry the horizontal stabilizer vertical load at the front spar location in the RV10. If you look at the joint closely you will notice that the two angle fittings will have heel toe action at the base. This by the way identical to design Piper uses on some of its aircraft and it works. I can only surmise that its one of the many details Vans has copied from someone else. Its not the lightest or most elegant solution but it gets the job done, its simple and its cheap. Another example is the use of 6061 aluminum which is considered very weak not typically not used in more advanced aircraft. the AN3 bolts we use are also not used in more advanced designs as they are at the low end of steels capability and there are much stronger bolts for the same weight.
In the design change I made I increased the diameter of the hex extension by 50% which inturn lowered the heel toe load by the same amount as the moment arm has increased. This results in about a 30% decrease in stress in the bolt. Increasing the diameter of the bolt increased the bolt area by 2.25 times and resulted in a corresponding decrease in the bolt stress. If you take these two changes together the operating stress in the new bolt is about 30% of Van's design (70% reduction in stress.) This is not a guess or heresay, this is the rough number using a simplistic analysis method. Since in general a 10% decrease in stess will double the fatigue life this should result in approximately 2000 fold increase in fatigue life. You can see this from a typical steel fatigue curve. See attached figure for 4130 steel which indicates much more than 3 orders of magnitude improvement in life for a 70% reduction in stress (red vs blue line.) In fact it appears that for 4130 we would be operating below its endurance limit so we would be approaching infinite life. What I haven't considered here is the preload in the bolt which also tilts the scale on the side of the larger bolt.
Lets conservatively say that these bolts fail in 50 hrs of flying, then a 2000 fold increase will give me a life of 100,000hrs using a scatter factor of 3 which is typicall for aircraft I would expect at least a 33000hr life which I believe is adequate. And there are aircraft flying with the original design with hundereds of hours with no failures. Truth of the matter is that this design is probably adequate with a 3/4" hex extension and only an AN5 bolt.
My conclusion is that the revised design is adequate. If someone doesn't think so that's okay too.
Niko
40188
---
| - The Matronics RV10-List Email Forum - | | Use the List Feature Navigator to browse the many List utilities available such as the Email Subscriptions page, Archive Search & Download, 7-Day Browse, Chat, FAQ, Photoshare, and much more:
http://www.matronics.com/Navigator?RV10-List |
|
|
|
Back to top |
|
 |
indigoonlatigo(at)msn.com Guest
|
Posted: Fri Mar 16, 2007 6:02 am Post subject: Axle Extension - Brute Force Method |
|
|
Excellent and well thought out response. I agree with you on all the
mathmatical analysis, not that I did it or checked it. I still think it is
not a good design, regardless of how much beef you put into it.
I do not agree however that the fastening of the HS is the same meathod. The
design for the wheel faring is a single axis, like a flag pole.
The HS angle brackets, two total, each has two bolts for a total of four. In
addition, the forks that anchor the rear spar, if I recal correctly, has
another two bolts per fork for a total of four. So all said, there are eight
bolts, four working in both shear and tension on the main spar and four
working more in shear on the rear spar. I like to think of it like a four
legged stool with all the legs anchored to the ground. It is very stable
with little change that lateral loads will be able to impart any damage to
anyone of the eight bolts.
The wheel faring, I see it as a one legged stool anchored into the ground.
In this case, Rick, size matters, because that guy that kept agreeing to
Supersized orders at MCDonalds(Drives a Hummer and leaves his light on all
day long when no one is home) is gonna find himself on that ground with no
one to help him get up. Like a rollie polli bug that's stuck on its back.
If the faring attachment mechanis breaks and if the faring only drags on the
ground, no problem.
But is it tears off, gets sucked up under the tire and then thrown, damaging
the bottom of the plane, wing or break line than it is a problem. We worked
way too hard to make these planes look great and function well to suffer
that fate.
Get the name of Tim's contact and run another order. I would make you one if
I had the lathe.
Thanks for listening.
Rick, little green men were chaising me, thats why I was running. They were
LITTLE, and when I turned around and chaised them, they led me to their pot
of GOLD. Still can't afford that glass panel.
No dentistry today, only kindergarden teaching and then plane building. No
more posts.
JOhn G #409
[quote]From: Niko <owl40188(at)yahoo.com>
Reply-To: rv10-list(at)matronics.com
To: rv10-list(at)matronics.com
Subject: Re: Fw: Axle Extension - Brute Force Method
Date: Thu, 15 Mar 2007 15:26:25 -0700 (PDT)
Well John, I don't think you are being a smart ass and you have not
offended me in any way. I am just writing this for an informational point
of view as I have gotten a lot of usefull information from this group and I
am trying to give back a little.
There is a big difference between a "poor" design and margin of safety. A
poor structural design simply means its inefficient in carrying loads it
does not mean that it will fail. The RV10s, small Cessnas, and small
Pipers are filled with design details which are considered "poor" because
they are structurally inefficient but they have adequate margins of safety
and they work. They are just heavy but they are simple cheap methods of
doing a task and frankly I believe in most cases appropriate for the
aircraft they are being used in.
The current axle extension design that Van's has is not a bad design its
simply a bit undersized. It works in heel-toe action what you are calling
a fulcrum. This is not a mystical design. The load on the bolt for a
given configuration can be easily calculated and sized appropriately. By
the way this same concept is being used to carry the horizontal stabilizer
vertical load at the front spar location in the RV10. If you look at the
joint closely you will notice that the two angle fittings will have heel
toe action at the base. This by the way identical to design Piper uses on
some of its aircraft and it works. I can only surmise that its one of the
many details Vans has copied from someone else. Its not the lightest or
most elegant solution but it gets the job done, its simple and its cheap.
Another example is the use of 6061 aluminum which is considered very weak
not typically not used in more advanced aircraft. the AN3 bolts we use are
also not used in more
advanced designs as they are at the low end of steels capability and
there are much stronger bolts for the same weight.
In the design change I made I increased the diameter of the hex extension
by 50% which inturn lowered the heel toe load by the same amount as the
moment arm has increased. This results in about a 30% decrease in stress
in the bolt. Increasing the diameter of the bolt increased the bolt area
by 2.25 times and resulted in a corresponding decrease in the bolt stress.
If you take these two changes together the operating stress in the new bolt
is about 30% of Van's design (70% reduction in stress.) This is not a
guess or heresay, this is the rough number using a simplistic analysis
method. Since in general a 10% decrease in stess will double the fatigue
life this should result in approximately 2000 fold increase in fatigue
life. You can see this from a typical steel fatigue curve. See attached
figure for 4130 steel which indicates much more than 3 orders of magnitude
improvement in life for a 70% reduction in stress (red vs blue line.) In
fact it appears that for 4130 we
would be operating below its endurance limit so we would be approaching
infinite life. What I haven't considered here is the preload in the bolt
which also tilts the scale on the side of the larger bolt.
Lets conservatively say that these bolts fail in 50 hrs of flying, then a
2000 fold increase will give me a life of 100,000hrs using a scatter factor
of 3 which is typicall for aircraft I would expect at least a 33000hr life
which I believe is adequate. And there are aircraft flying with the
original design with hundereds of hours with no failures. Truth of the
matter is that this design is probably adequate with a 3/4" hex extension
and only an AN5 bolt.
My conclusion is that the revised design is adequate. If someone doesn't
think so that's okay too.
Niko
40188
---
| - The Matronics RV10-List Email Forum - | | Use the List Feature Navigator to browse the many List utilities available such as the Email Subscriptions page, Archive Search & Download, 7-Day Browse, Chat, FAQ, Photoshare, and much more:
http://www.matronics.com/Navigator?RV10-List |
|
|
|
Back to top |
|
 |
owl40188(at)yahoo.com Guest
|
Posted: Fri Mar 16, 2007 9:18 am Post subject: Axle Extension - Brute Force Method |
|
|
I also like the design Tim came up particularly the reduced section on the outboard side to save weight thats why I initially got into the group buy. The basic concept though that both Tim and I used is no different than Van's. Its the same design concept just a bit beefier. Its single bolt though the axle nut and still has plenty of heel toe action just different amounts of heel toe and different strength bolts.
Since you told me to "Get the name of Tim's contact and run another order" I would say maybe you need to stop shooting from the hip and show some data if you are claiming something will fail or is undersized . I do appreciate the thought of you making one for me though. If you ever do get a lathe I would like the 3/4 inch hex bar rounded at the outboard end and the diameter reduced to 1/2 inch on the outboard end. You can keep the inboard edge just the way it is. This will save a bit of weight which also reduces the load on the bolt. If you can anodize it also that will make it look really nice.
As far as the horizontal stabilizer, the heel toe action is definitely there. If I get some time this weekend I might draw some figures and elaborate, or maybe people are getting tired of this subject and its best to let it go and get back to priming discussions.
Either way best wishes in your building and do what you feel comfortable with as long as you don't reduce sizes from Van's design.
By the way for anyone wanting to do something similar, this is just my opinion as to what is adequate and I might be wrong and have been wrong before.
Is everyone priming their parts? I hope you realize your airplane might come apart in flight if you don't.
Do not archive.
Niko
40188
---
| - The Matronics RV10-List Email Forum - | | Use the List Feature Navigator to browse the many List utilities available such as the Email Subscriptions page, Archive Search & Download, 7-Day Browse, Chat, FAQ, Photoshare, and much more:
http://www.matronics.com/Navigator?RV10-List |
|
|
|
Back to top |
|
 |
|
|
You cannot post new topics in this forum You cannot reply to topics in this forum You cannot edit your posts in this forum You cannot delete your posts in this forum You cannot vote in polls in this forum You cannot attach files in this forum You can download files in this forum
|
Powered by phpBB © 2001, 2005 phpBB Group
|