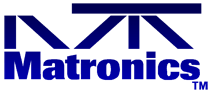 |
Matronics Email Lists Web Forum Interface to the Matronics Email Lists
|
View previous topic :: View next topic |
Author |
Message |
james(at)etravel.org Guest
|
Posted: Fri May 28, 2010 1:35 am Post subject: Gauge wiring best practice |
|
|
Greetings to all,
I've bought a number of UMA's delightful 1-1/4" custom-marked engine
instruments (CHT, EGT, fuel pressure, oil pressure, oil temp. etc.)
and I'm about to start wiring them in to my plane project (Jodel D150
with Lycoming O-235). I've a couple of questions about best practices
and I wonder if you can help.
I would like to make the panel easily disconnectable, and I'm going to
be using something like Tyco AMP MATE-N-LOK connectors for connecting
other things to the panel. (These are multi-way locking connectors,
with crimped pins, supporting various wire gauges -- 10-30AWG at
least).
To connect the UMA instruments, I figure I can go one of two ways:
1) wire each UMA-supplied DB9 connector straight through to the power
bus, ground bus, and sender. The downside is that I'd have to screw /
unscrew many connectors to disconnect the 8 or so UMA instruments,
which might be quick tricky behind the panel.
2) wire all the DB9 connectors to a multi-way MATE-N-LOK plug behind
the panel, and then wire a MATE-N-LOK socket to the various sensors
and whatnot. This would give me the big advantage of being able to
disconnect all engine instruments in one connector.
I don't see any downside to this, but any input would be greatly appreciated.
Secondly, I note that each of the instruments requires a 12V supply
and a ground. Can all these engine instruments be connected together
at the instrument panel and then run to the power bus and ground bus
in two "big" wires, or should I run two separate wires back for each
instrument?
The 12V feeds could be linked together, with the risk of one engine
instrument going u/s knocking out all the others, but this seems like
a smallish risk. Or perhaps I could do a combo approach -- a few
feeds each feeding a couple or three instruments. Any thoughts about
this from you seasoned flyers would be great.
Also, I've read what it says about grounding, etc., in the
Aeroelectric Connection, and the possibility for errors because of
resistance through different ground paths. However, I find that the
UMA instruments have in general four connections: +12V, GND, sensor
+ve, sensor -ve, all connected via a DB-9 socket. Does this mean that
the sensor input has a sort of privileged design because it has its
own ground going direct the instrument? The two grounds could be
connected internally I guess, but I can't work out what difference
that would make!
Very many thanks in anticipation of your advice.
James
| - The Matronics AeroElectric-List Email Forum - | | Use the List Feature Navigator to browse the many List utilities available such as the Email Subscriptions page, Archive Search & Download, 7-Day Browse, Chat, FAQ, Photoshare, and much more:
http://www.matronics.com/Navigator?AeroElectric-List |
|
|
|
Back to top |
|
 |
nuckolls.bob(at)aeroelect Guest
|
Posted: Fri May 28, 2010 9:28 am Post subject: Gauge wiring best practice |
|
|
I would like to make the panel easily disconnectable, and I'm going to
be using something like Tyco AMP MATE-N-LOK connectors for connecting
other things to the panel. (These are multi-way locking connectors,
with crimped pins, supporting various wire gauges -- 10-30AWG at
least).
Keep in mind that every connector interface adds three new
joints to every wire. Running lots of electro-goodies through a
single connector adds a single point of failure for all
those electro-goodies.
To connect the UMA instruments, I figure I can go one of two ways:
1) wire each UMA-supplied DB9 connector straight through to the power
bus, ground bus, and sender. The downside is that I'd have to screw /
unscrew many connectors to disconnect the 8 or so UMA instruments,
which might be quick tricky behind the panel.
2) wire all the DB9 connectors to a multi-way MATE-N-LOK plug behind
the panel, and then wire a MATE-N-LOK socket to the various sensors
and whatnot. This would give me the big advantage of being able to
disconnect all engine instruments in one connector.
I don't see any downside to this, but any input would be greatly appreciated.
You can do this . . . but you'll never find it done
on production aircraft either commercial or military.
It's a little-value-added activity that does add
significant cost-of-ownership and reduces reliability.
You can replace the stock jack-screws with devices
having extended handles designed for access with
the bare fingers.
It's a fact that the majority of d-sub connectors come with
short, slotted-head 4-40 jack screws that are EXCEEDINGLY
difficult to work with in confined spaces traversed by wire
bundles. Theres a host of fingers-only, d-sub retention
systems including Positronics V-series and mil-spec slide
locks. There's also a handy but seldom offered wire-bale-
and-clip that used to be VERY popular on printer connectors.
These are easy to incorporate into new products were you want
to order thousands . . . but unfortunately, they're not
often found as catalog items.
The computer world has offered a variety of extended jack-screw
handles, most of which can be operated with the bare fingers.
My personal choice is the DIY extended jackscrew fabricated
from a piece of 4-40 screw and 3/16" hex threaded spacer.
See:
http://tinyurl.com/34nrdd5
When accessed with the nifty miniature nut-driver from
Xcelite (or similar) one can get a better feel of just
how tight the screw is when replacing it . . . and
it's a light-year away from the inconvenience of
stock, slot-head jack-screws.
Secondly, I note that each of the instruments requires a 12V supply
and a ground. Can all these engine instruments be connected together
at the instrument panel and then run to the power bus and ground bus
in two "big" wires, or should I run two separate wires back for each
instrument?
Failure-tolerant design suggests that every electro-whizzie
be treated as a separate system . . . i.e. no single failure
affects more than one system. Just how much your personal
design goals tolerate risks for merging systems is up to
you. What you propose will FUNCTION as expected as long
as everything is working right.
Also, I've read what it says about grounding, etc., in the
AeroElectric Connection, and the possibility for errors because of
resistance through different ground paths. However, I find that the
UMA instruments have in general four connections: +12V, GND, sensor
+ve, sensor -ve, all connected via a DB-9 socket. Does this mean that
the sensor input has a sort of privileged design because it has its
own ground going direct the instrument? The two grounds could be
connected internally I guess, but I can't work out what difference
that would make!
Probably no functional differences. However, it's
been my observation over the years that spending a lot
of time adding complexity for some perceived future
convenience has a poor return on investment. Suggest
you 'enhance' the stock jack-screws and wire each
instrument as a stand-alone system while minimizing
features shared with other systems.
Bob . . .
| - The Matronics AeroElectric-List Email Forum - | | Use the List Feature Navigator to browse the many List utilities available such as the Email Subscriptions page, Archive Search & Download, 7-Day Browse, Chat, FAQ, Photoshare, and much more:
http://www.matronics.com/Navigator?AeroElectric-List |
|
|
|
Back to top |
|
 |
james(at)etravel.org Guest
|
Posted: Sun May 30, 2010 5:01 am Post subject: Gauge wiring best practice |
|
|
Bob,
Thanks for the insights. Perhaps with some smallish changes to the
panel, to make it easily removable, it will become easier to implement
a fewer-connections electrical installation. The standard DB9s _are_
a pain, but your suggestions, and the others', are definitely going to
make life easier...
James
On Fri, May 28, 2010 at 6:29 PM, Robert L. Nuckolls, III
<nuckolls.bob(at)aeroelectric.com> wrote:
Quote: |
<nuckolls.bob(at)aeroelectric.com>
I would like to make the panel easily disconnectable, and I'm going to
be using something like Tyco AMP MATE-N-LOK connectors for connecting
other things to the panel. (These are multi-way locking connectors,
with crimped pins, supporting various wire gauges -- 10-30AWG at
least).
Keep in mind that every connector interface adds three new
joints to every wire. Running lots of electro-goodies through a
single connector adds a single point of failure for all
those electro-goodies.
To connect the UMA instruments, I figure I can go one of two ways:
1) wire each UMA-supplied DB9 connector straight through to the power
bus, ground bus, and sender. The downside is that I'd have to screw /
unscrew many connectors to disconnect the 8 or so UMA instruments,
which might be quick tricky behind the panel.
2) wire all the DB9 connectors to a multi-way MATE-N-LOK plug behind
the panel, and then wire a MATE-N-LOK socket to the various sensors
and whatnot. This would give me the big advantage of being able to
disconnect all engine instruments in one connector.
I don't see any downside to this, but any input would be greatly
appreciated.
You can do this . . . but you'll never find it done
on production aircraft either commercial or military.
It's a little-value-added activity that does add
significant cost-of-ownership and reduces reliability.
You can replace the stock jack-screws with devices
having extended handles designed for access with
the bare fingers.
It's a fact that the majority of d-sub connectors come with
short, slotted-head 4-40 jack screws that are EXCEEDINGLY
difficult to work with in confined spaces traversed by wire
bundles. Theres a host of fingers-only, d-sub retention
systems including Positronics V-series and mil-spec slide
locks. There's also a handy but seldom offered wire-bale-
and-clip that used to be VERY popular on printer connectors.
These are easy to incorporate into new products were you want
to order thousands . . . but unfortunately, they're not
often found as catalog items.
The computer world has offered a variety of extended jack-screw
handles, most of which can be operated with the bare fingers.
My personal choice is the DIY extended jackscrew fabricated
from a piece of 4-40 screw and 3/16" hex threaded spacer.
See:
http://tinyurl.com/34nrdd5
When accessed with the nifty miniature nut-driver from
Xcelite (or similar) one can get a better feel of just
how tight the screw is when replacing it . . . and
it's a light-year away from the inconvenience of
stock, slot-head jack-screws.
Secondly, I note that each of the instruments requires a 12V supply
and a ground. Can all these engine instruments be connected together
at the instrument panel and then run to the power bus and ground bus
in two "big" wires, or should I run two separate wires back for each
instrument?
Failure-tolerant design suggests that every electro-whizzie
be treated as a separate system . . . i.e. no single failure
affects more than one system. Just how much your personal
design goals tolerate risks for merging systems is up to
you. What you propose will FUNCTION as expected as long
as everything is working right.
Also, I've read what it says about grounding, etc., in the
AeroElectric Connection, and the possibility for errors because of
resistance through different ground paths. However, I find that the
UMA instruments have in general four connections: +12V, GND, sensor
+ve, sensor -ve, all connected via a DB-9 socket. Does this mean that
the sensor input has a sort of privileged design because it has its
own ground going direct the instrument? The two grounds could be
connected internally I guess, but I can't work out what difference
that would make!
Probably no functional differences. However, it's
been my observation over the years that spending a lot
of time adding complexity for some perceived future
convenience has a poor return on investment. Suggest
you 'enhance' the stock jack-screws and wire each
instrument as a stand-alone system while minimizing
features shared with other systems.
Bob . . .
|
| - The Matronics AeroElectric-List Email Forum - | | Use the List Feature Navigator to browse the many List utilities available such as the Email Subscriptions page, Archive Search & Download, 7-Day Browse, Chat, FAQ, Photoshare, and much more:
http://www.matronics.com/Navigator?AeroElectric-List |
|
|
|
Back to top |
|
 |
|
|
You cannot post new topics in this forum You cannot reply to topics in this forum You cannot edit your posts in this forum You cannot delete your posts in this forum You cannot vote in polls in this forum You cannot attach files in this forum You can download files in this forum
|
Powered by phpBB © 2001, 2005 phpBB Group
|