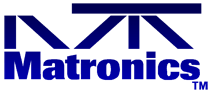 |
Matronics Email Lists Web Forum Interface to the Matronics Email Lists
|
View previous topic :: View next topic |
Author |
Message |
Mauledriver(at)nc.rr.com Guest
|
Posted: Wed Jul 29, 2015 1:11 pm Post subject: Signs of corrosion on tail cone |
|
|
I'm beginning to see signs of corrosion between the top skin and the
side skins of my tailcone. The corrosion is happening underneath the
paint. Inside the tailcone there are a few 'wisps' of grayish corrosion
coming up from the same joint which is riveted to the angle longerons.
Anyone else experiencing this? What are you finding, what have you done?
Plane is hangared except when traveling and only occassionally sees salt
air - and I wash it down after each encounter.
| - The Matronics RV10-List Email Forum - | | Use the List Feature Navigator to browse the many List utilities available such as the Email Subscriptions page, Archive Search & Download, 7-Day Browse, Chat, FAQ, Photoshare, and much more:
http://www.matronics.com/Navigator?RV10-List |
|
|
|
Back to top |
|
 |
cooprv7(at)yahoo.com Guest
|
Posted: Wed Jul 29, 2015 1:59 pm Post subject: Signs of corrosion on tail cone |
|
|
I’m not sure if this will help with corrosion already there, but I sprayed the tailbone with Corrosion X and the film is still there after 7 years and 720 hours. I appreciate you bringing this up though as it wouldn’t hurt to apply again. One gotcha, do NOT apply this until after you paint your airplane, otherwise it will be a bear to get the paint to adhere properly.
Marcus
Quote: | On Jul 30, 2015, at 12:05 AM, Bill Watson <Mauledriver(at)nc.rr.com> wrote:
I'm beginning to see signs of corrosion between the top skin and the side skins of my tailcone. The corrosion is happening underneath the paint. Inside the tailcone there are a few 'wisps' of grayish corrosion coming up from the same joint which is riveted to the angle longerons.
Anyone else experiencing this? What are you finding, what have you done?
Plane is hangared except when traveling and only occassionally sees salt air - and I wash it down after each encounter.
|
| - The Matronics RV10-List Email Forum - | | Use the List Feature Navigator to browse the many List utilities available such as the Email Subscriptions page, Archive Search & Download, 7-Day Browse, Chat, FAQ, Photoshare, and much more:
http://www.matronics.com/Navigator?RV10-List |
|
|
|
Back to top |
|
 |
carl.froehlich(at)verizon Guest
|
Posted: Wed Jul 29, 2015 2:14 pm Post subject: Signs of corrosion on tail cone |
|
|
Is this a quick build?
Carl
Quote: | On Jul 29, 2015, at 2:05 PM, Bill Watson <Mauledriver(at)nc.rr.com> wrote:
I'm beginning to see signs of corrosion between the top skin and the side skins of my tailcone. The corrosion is happening underneath the paint. Inside the tailcone there are a few 'wisps' of grayish corrosion coming up from the same joint which is riveted to the angle longerons.
Anyone else experiencing this? What are you finding, what have you done?
Plane is hangared except when traveling and only occassionally sees salt air - and I wash it down after each encounter.
|
| - The Matronics RV10-List Email Forum - | | Use the List Feature Navigator to browse the many List utilities available such as the Email Subscriptions page, Archive Search & Download, 7-Day Browse, Chat, FAQ, Photoshare, and much more:
http://www.matronics.com/Navigator?RV10-List |
|
|
|
Back to top |
|
 |
Mauledriver(at)nc.rr.com Guest
|
Posted: Wed Jul 29, 2015 5:53 pm Post subject: Signs of corrosion on tail cone |
|
|
Yes, but I build the tailcone. No relationship between the two I would
think.
On 7/29/2015 6:11 PM, Carl Froehlich wrote:
Quote: |
Is this a quick build?
Carl
> On Jul 29, 2015, at 2:05 PM, Bill Watson <Mauledriver(at)nc.rr.com> wrote:
>
>
>
> I'm beginning to see signs of corrosion between the top skin and the side skins of my tailcone. The corrosion is happening underneath the paint. Inside the tailcone there are a few 'wisps' of grayish corrosion coming up from the same joint which is riveted to the angle longerons.
>
> Anyone else experiencing this? What are you finding, what have you done?
>
> Plane is hangared except when traveling and only occassionally sees salt air - and I wash it down after each encounter.
>
>
-----
No virus found in this message.
Checked by AVG - www.avg.com
|
| - The Matronics RV10-List Email Forum - | | Use the List Feature Navigator to browse the many List utilities available such as the Email Subscriptions page, Archive Search & Download, 7-Day Browse, Chat, FAQ, Photoshare, and much more:
http://www.matronics.com/Navigator?RV10-List |
|
|
|
Back to top |
|
 |
rv10pro(at)gmail.com Guest
|
Posted: Thu Jul 30, 2015 6:11 am Post subject: Signs of corrosion on tail cone |
|
|
#1 Surface preparation. Many on this list talk of Acetone or Alcohol cleaning. Aluminum begins Aluminum Oxide within an hour of scotchbrighting. Doing the work in a high humidity environment or an area under the influence of Salt vapor can impact the surface prep in short order. Correction: do an evaporation test of the solvent used on a piece of clear glass and see if after evaporation, deposits form. Prime within 15 minutes of scotchbrighting never hours or days.
#2 Galvanic action by use of the airframe as the ground path from adjacent electrical circuits is another. Run a separate return path from lighting components forward to a more substantial frame member not in contact with exterior skin if using single wire power runs.
#3 Use of chemicals which promotes Hydrolysis. The old Simple Green before they reformulated Aviation grade was notorious. Wicking action is best reduced by wet sealing the two skins with a roller of thin proseal. RTV is not a cure all.
#4 "Faying action" between two close sheet metal items attached together wick most alkaline cleaners into the joints mentioned. Clear rinse the joints with de-ionized water and pay particular attention to the areas showing signs. Oxidation once started must be removed. The cause corrected and the treated skin recoated with an Alodine or similar treatment. It is remotely possible the primer had some impact on the outcome.
Least desireable Corrective Action: remove the skin and treat before the corrosion reaches 10% in skin depth.
Note: Cessna had a very large batch of aircraft twenty years ago with Filiform corrosion which showed YEARS later. The research found they were parking the prepped aircraft outside overnight provided Acid Rain vapor to condense on the material. The skin was dry and "Clean" but the acid residual began working between the skin and final coats - after application. Only solution, soda blast, properly reprep the surface and reapply a corrective topcoat.
The type of corrosion found helps determine the cause and corrective action. Just shooting blind on a sensitive issue. Good Luck with the solution.
John C.
#40600
On Wed, Jul 29, 2015 at 6:49 PM, Bill Watson <Mauledriver(at)nc.rr.com (Mauledriver(at)nc.rr.com)> wrote:
[quote]--> RV10-List message posted by: Bill Watson <Mauledriver(at)nc.rr.com (Mauledriver(at)nc.rr.com)>
Yes, but I build the tailcone. No relationship between the two I would think.
On 7/29/2015 6:11 PM, Carl Froehlich wrote:
Quote: | --> RV10-List message posted by: Carl Froehlich <carl.froehlich(at)verizon.net (carl.froehlich(at)verizon.net)>
Is this a quick build?
Carl
Quote: | On Jul 29, 2015, at 2:05 PM, Bill Watson <Mauledriver(at)nc.rr.com (Mauledriver(at)nc.rr.com)> wrote:
--> RV10-List message posted by: Bill Watson <Mauledriver(at)nc.rr.com (Mauledriver(at)nc.rr.com)>
I'm beginning to see signs of corrosion between the top skin and the side skins of my tailcone. The corrosion is happening underneath the paint. Inside the tailcone there are a few 'wisps' of grayish corrosion coming up from the same joint which is riveted to the angle longerons.
Anyone else experiencing this? What are you finding, what have you done?
Plane is hangared except when traveling and only occassionally sees salt air - and I wash it down after each encounter.
|
-----
No virus found in this message.
Checked by AVG - www.avg.com
|
===========
-List" rel="noreferrer" target="_blank">http://www.matronics.com/Navigator?RV10-List
===========
FORUMS -
eferrer" target="_blank">http://forums.matronics.com
===========
b Site -
-Matt Dralle, List Admin.
rel="noreferrer" target="_blank">http://www.matronics.com/contribution
===========
[b]
| - The Matronics RV10-List Email Forum - | | Use the List Feature Navigator to browse the many List utilities available such as the Email Subscriptions page, Archive Search & Download, 7-Day Browse, Chat, FAQ, Photoshare, and much more:
http://www.matronics.com/Navigator?RV10-List |
|
|
|
Back to top |
|
 |
Kellym
Joined: 10 Jan 2006 Posts: 1705 Location: Sun Lakes AZ
|
Posted: Thu Jul 30, 2015 6:42 am Post subject: Signs of corrosion on tail cone |
|
|
I will agree with all John wrote except the electrical ground issue.
Given that type certified aircraft from the end of WWII on have used the
airframe as a ground path, you would expect to see such problems if it
were an issue, within say 30-40 years. Hasn't happened. My current
aircraft is 50 yrs old. Not one bit of corrosion around any of the power
consuming items that are grounded to the airframe, nor the ground attach
points. IIRC Bob Nuckolls of AeroElectric connection says only
electronics need central grounding, NOT lights, pitot heat, and other
high current devices. Given he was the expert for Cessna, then Beech, I
tend to listen to his opinions.
I will not that where Vans uses aluminum angle for longerons, etc. that
aluminum angle is NOT Alclad, and requires some form of primer or
anodizing. I don't believe any of the material Vans supplies has any
primer, except in the quick build components, and I'm not sure they do
anything between the skins and the longerons. Heck, on mine they didn't
even bother to countersink the longerons where they attached to dimpled
skins.
On 7/30/2015 7:08 AM, John Cox wrote:
Quote: | #1 Surface preparation. Many on this list talk of Acetone or Alcohol
cleaning. Aluminum begins Aluminum Oxide within an hour of
scotchbrighting. Doing the work in a high humidity environment or an
area under the influence of Salt vapor can impact the surface prep in
short order. Correction: do an evaporation test of the solvent used
on a piece of clear glass and see if after evaporation, deposits
form. Prime within 15 minutes of scotchbrighting never hours or days.
#2 Galvanic action by use of the airframe as the ground path from
adjacent electrical circuits is another. Run a separate return path
from lighting components forward to a more substantial frame member
not in contact with exterior skin if using single wire power runs.
#3 Use of chemicals which promotes Hydrolysis. The old Simple Green
before they reformulated Aviation grade was notorious. Wicking action
is best reduced by wet sealing the two skins with a roller of thin
proseal. RTV is not a cure all.
|
| - The Matronics RV10-List Email Forum - | | Use the List Feature Navigator to browse the many List utilities available such as the Email Subscriptions page, Archive Search & Download, 7-Day Browse, Chat, FAQ, Photoshare, and much more:
http://www.matronics.com/Navigator?RV10-List |
|
_________________ Kelly McMullen
A&P/IA, EAA Tech Counselor # 5286
KCHD |
|
Back to top |
|
 |
rv10pro(at)gmail.com Guest
|
Posted: Thu Jul 30, 2015 7:13 am Post subject: Signs of corrosion on tail cone |
|
|
Improper surface prep can and does lead to issues. Did someone state Van's preps parts?? Not the company I know so well. I will assume Bill did everything "Top Notch". Washing of aircraft is another issue not discussed on this forum, yet.
Can give examples of electrolysis doing corrosion damage but was not intending to counter the disciples of Mr. Nuckholls. SFAR88 has manufacturers rethinking due to FAA mandate the issues of electric current beyond electronics. On our airliners which get 4400-4500 hours per year, the damage is accelerated. Just a perspective. Maybe Acid Rain can be blamed since Mr Nuckoll's was not retired at the time at Cessna when the filliform was such a large issue.
Not a supporter of Mr. Scott's mantra "Just Build It". Build it safe, enjoy flight, live LONG.
jc
On Thu, Jul 30, 2015 at 7:38 AM, Kelly McMullen <kellym(at)aviating.com (kellym(at)aviating.com)> wrote:
[quote]--> RV10-List message posted by: Kelly McMullen <kellym(at)aviating.com (kellym(at)aviating.com)>
I will agree with all John wrote except the electrical ground issue. Given that type certified aircraft from the end of WWII on have used the airframe as a ground path, you would expect to see such problems if it were an issue, within say 30-40 years. Hasn't happened. My current aircraft is 50 yrs old. Not one bit of corrosion around any of the power consuming items that are grounded to the airframe, nor the ground attach points. IIRC Bob Nuckolls of AeroElectric connection says only electronics need central grounding, NOT lights, pitot heat, and other high current devices. Given he was the expert for Cessna, then Beech, I tend to listen to his opinions.
I will not that where Vans uses aluminum angle for longerons, etc. that aluminum angle is NOT Alclad, and requires some form of primer or anodizing. I don't believe any of the material Vans supplies has any primer, except in the quick build components, and I'm not sure they do anything between the skins and the longerons. Heck, on mine they didn't even bother to countersink the longerons where they attached to dimpled skins.
On 7/30/2015 7:08 AM, John Cox wrote:
Quote: | #1 Surface preparation. Many on this list talk of Acetone or Alcohol cleaning. Aluminum begins Aluminum Oxide within an hour of scotchbrighting. Doing the work in a high humidity environment or an area under the influence of Salt vapor can impact the surface prep in short order. Correction: do an evaporation test of the solvent used on a piece of clear glass and see if after evaporation, deposits form. Prime within 15 minutes of scotchbrighting never hours or days.
#2 Galvanic action by use of the airframe as the ground path from adjacent electrical circuits is another. Run a separate return path from lighting components forward to a more substantial frame member not in contact with exterior skin if using single wire power runs.
#3 Use of chemicals which promotes Hydrolysis. The old Simple Green before they reformulated Aviation grade was notorious. Wicking action is best reduced by wet sealing the two skins with a roller of thin proseal. RTV is not a cure all.
|
===========
-List" rel="noreferrer" target="_blank">http://www.matronics.com/Navigator?RV10-List
===========
FORUMS -
eferrer" target="_blank">http://forums.matronics.com
===========
b Site -
-Matt Dralle, List Admin.
rel="noreferrer" target="_blank">http://www.matronics.com/contribution
===========
[b]
| - The Matronics RV10-List Email Forum - | | Use the List Feature Navigator to browse the many List utilities available such as the Email Subscriptions page, Archive Search & Download, 7-Day Browse, Chat, FAQ, Photoshare, and much more:
http://www.matronics.com/Navigator?RV10-List |
|
|
|
Back to top |
|
 |
Kellym
Joined: 10 Jan 2006 Posts: 1705 Location: Sun Lakes AZ
|
Posted: Thu Jul 30, 2015 7:30 am Post subject: Signs of corrosion on tail cone |
|
|
Vans quick build components do get primer, I believe AFTER they are
assembled.
Cessna's corrosion had nothing to do with electrics. It had to do with
your mention of the overnight outside AND they eliminated one of the two
components of the primer they were using. It was supposed to be done on
two phases, not a single coat.
On 7/30/2015 8:09 AM, John Cox wrote:
Quote: | Improper surface prep can and does lead to issues. Did someone state
Van's preps parts?? Not the company I know so well. I will assume
Bill did everything "Top Notch". Washing of aircraft is another issue
not discussed on this forum, yet.
Can give examples of electrolysis doing corrosion damage but was not
intending to counter the disciples of Mr. Nuckholls. SFAR88 has
manufacturers rethinking due to FAA mandate the issues of electric
current beyond electronics. On our airliners which get 4400-4500
hours per year, the damage is accelerated. Just a perspective. Maybe
Acid Rain can be blamed since Mr Nuckoll's was not retired at the time
at Cessna when the filliform was such a large issue.
Not a supporter of Mr. Scott's mantra "Just Build It". Build it safe,
enjoy flight, live LONG.
jc
On Thu, Jul 30, 2015 at 7:38 AM, Kelly McMullen <kellym(at)aviating.com
<mailto:kellym(at)aviating.com>> wrote:
<kellym(at)aviating.com <mailto:kellym(at)aviating.com>>
I will agree with all John wrote except the electrical ground
issue. Given that type certified aircraft from the end of WWII on
have used the airframe as a ground path, you would expect to see
such problems if it were an issue, within say 30-40 years. Hasn't
happened. My current aircraft is 50 yrs old. Not one bit of
corrosion around any of the power consuming items that are
grounded to the airframe, nor the ground attach points. IIRC Bob
Nuckolls of AeroElectric connection says only electronics need
central grounding, NOT lights, pitot heat, and other high current
devices. Given he was the expert for Cessna, then Beech, I tend to
listen to his opinions.
I will not that where Vans uses aluminum angle for longerons, etc.
that aluminum angle is NOT Alclad, and requires some form of
primer or anodizing. I don't believe any of the material Vans
supplies has any primer, except in the quick build components, and
I'm not sure they do anything between the skins and the longerons.
Heck, on mine they didn't even bother to countersink the longerons
where they attached to dimpled skins.
On 7/30/2015 7:08 AM, John Cox wrote:
#1 Surface preparation. Many on this list talk of Acetone or
Alcohol cleaning. Aluminum begins Aluminum Oxide within an
hour of scotchbrighting. Doing the work in a high humidity
environment or an area under the influence of Salt vapor can
impact the surface prep in short order. Correction: do an
evaporation test of the solvent used on a piece of clear glass
and see if after evaporation, deposits form. Prime within 15
minutes of scotchbrighting never hours or days.
#2 Galvanic action by use of the airframe as the ground path
from adjacent electrical circuits is another. Run a separate
return path from lighting components forward to a more
substantial frame member not in contact with exterior skin if
using single wire power runs.
#3 Use of chemicals which promotes Hydrolysis. The old Simple
Green before they reformulated Aviation grade was notorious.
Wicking action is best reduced by wet sealing the two skins
with a roller of thin proseal. RTV is not a cure all.
===========
-List" rel="noreferrer"
target="_blank">http://www.matronics.com/Navigator?RV10-List
===========
FORUMS -
eferrer" target="_blank">http://forums.matronics.com
===========
b Site -
-Matt Dralle, List Admin.
rel="noreferrer" target="_blank">http://www.matronics.com/contribution
===========
http://www.matronics.com/contribution
|
| - The Matronics RV10-List Email Forum - | | Use the List Feature Navigator to browse the many List utilities available such as the Email Subscriptions page, Archive Search & Download, 7-Day Browse, Chat, FAQ, Photoshare, and much more:
http://www.matronics.com/Navigator?RV10-List |
|
_________________ Kelly McMullen
A&P/IA, EAA Tech Counselor # 5286
KCHD |
|
Back to top |
|
 |
Bob Turner
Joined: 03 Jan 2009 Posts: 885 Location: Castro Valley, CA
|
Posted: Sat Aug 01, 2015 9:01 am Post subject: Re: Signs of corrosion on tail cone |
|
|
I'd suggest getting a spray can of Corrosion X or ACF-50 and spraying along that joint and the angle. That stuff penetrates everywhere. It will not repair damage done but may stop or slow further damage.
| - The Matronics RV10-List Email Forum - | | Use the List Feature Navigator to browse the many List utilities available such as the Email Subscriptions page, Archive Search & Download, 7-Day Browse, Chat, FAQ, Photoshare, and much more:
http://www.matronics.com/Navigator?RV10-List |
|
_________________ Bob Turner
RV-10 QB |
|
Back to top |
|
 |
Mauledriver(at)nc.rr.com Guest
|
Posted: Sat Aug 01, 2015 12:09 pm Post subject: Signs of corrosion on tail cone |
|
|
Thanks John, a lot of good stuff there!
Looks like I have some form of filiform corrosion. I sure looks like 'something' leaked out from the seam after painting.
I primed the tail feathers with epoxy primer, the tailcone with Dupont wash primer, finished off the QB kit with rattle can primer, I did not prime the angle longerons (!)
The paint job included PreKote, epoxy primer and a Dupont Polyurethane.
My plan of action looks like 1) mechanically remove paint where corrosion is evident, 2)remove corrosion, clean, (conversion?), 3) prime and paint. Then apply one of the penetrating corrosion protection products to the inside of the tail cone along the seam.
On 7/30/2015 10:08 AM, John Cox wrote:
[quote] #1 Surface preparation. Many on this list talk of Acetone or Alcohol cleaning. Aluminum begins Aluminum Oxide within an hour of scotchbrighting. Doing the work in a high humidity environment or an area under the influence of Salt vapor can impact the surface prep in short order. Correction: do an evaporation test of the solvent used on a piece of clear glass and see if after evaporation, deposits form. Prime within 15 minutes of scotchbrighting never hours or days.
#2 Galvanic action by use of the airframe as the ground path from adjacent electrical circuits is another. Run a separate return path from lighting components forward to a more substantial frame member not in contact with exterior skin if using single wire power runs.
#3 Use of chemicals which promotes Hydrolysis. The old Simple Green before they reformulated Aviation grade was notorious. Wicking action is best reduced by wet sealing the two skins with a roller of thin proseal. RTV is not a cure all.
#4 "Faying action" between two close sheet metal items attached together wick most alkaline cleaners into the joints mentioned. Clear rinse the joints with de-ionized water and pay particular attention to the areas showing signs. Oxidation once started must be removed. The cause corrected and the treated skin recoated with an Alodine or similar treatment. It is remotely possible the primer had some impact on the outcome.
Least desireable Corrective Action: remove the skin and treat before the corrosion reaches 10% in skin depth.
Note: Cessna had a very large batch of aircraft twenty years ago with Filiform corrosion which showed YEARS later. The research found they were parking the prepped aircraft outside overnight provided Acid Rain vapor to condense on the material. The skin was dry and "Clean" but the acid residual began working between the skin and final coats - after application. Only solution, soda blast, properly reprep the surface and reapply a corrective topcoat.
The type of corrosion found helps determine the cause and corrective action. Just shooting blind on a sensitive issue. Good Luck with the solution.
John C.
#40600
On Wed, Jul 29, 2015 at 6:49 PM, Bill Watson <Mauledriver(at)nc.rr.com (Mauledriver(at)nc.rr.com)> wrote:
Quote: | --> RV10-List message posted by: Bill Watson <Mauledriver(at)nc.rr.com (Mauledriver(at)nc.rr.com)>
Yes, but I build the tailcone. No relationship between the two I would think.
On 7/29/2015 6:11 PM, Carl Froehlich wrote:
Quote: | --> RV10-List message posted by: Carl Froehlich <carl.froehlich(at)verizon.net (carl.froehlich(at)verizon.net)>
Is this a quick build?
Carl
Quote: | On Jul 29, 2015, at 2:05 PM, Bill Watson <Mauledriver(at)nc.rr.com (Mauledriver(at)nc.rr.com)> wrote:
--> RV10-List message posted by: Bill Watson <Mauledriver(at)nc.rr.com (Mauledriver(at)nc.rr.com)>
I'm beginning to see signs of corrosion between the top skin and the side skins of my tailcone. The corrosion is happening underneath the paint. Inside the tailcone there are a few 'wisps' of grayish corrosion coming up from the same joint which is riveted to the angle longerons.
Anyone else experiencing this? What are you finding, what have you done?
Plane is hangared except when traveling and only occassionally sees salt air - and I wash it down after each encounter.
|
-----
No virus found in this message.
Checked by AVG - www.avg.com
|
===========
-List" rel="noreferrer" target="_blank">http://www.matronics.com/Navigator?RV10-List
===========
FORUMS -
eferrer" target="_blank">http://forums.matronics.com
===========
b Site -
-Matt Dralle, List Admin.
rel="noreferrer" target="_blank">http://www.matronics.com/contribution
===========
|
No virus found in this message.
Checked by AVG - www.avg.com
Date: 07/30/15 [b]
| - The Matronics RV10-List Email Forum - | | Use the List Feature Navigator to browse the many List utilities available such as the Email Subscriptions page, Archive Search & Download, 7-Day Browse, Chat, FAQ, Photoshare, and much more:
http://www.matronics.com/Navigator?RV10-List |
|
|
|
Back to top |
|
 |
|
|
You cannot post new topics in this forum You cannot reply to topics in this forum You cannot edit your posts in this forum You cannot delete your posts in this forum You cannot vote in polls in this forum You cannot attach files in this forum You can download files in this forum
|
Powered by phpBB © 2001, 2005 phpBB Group
|